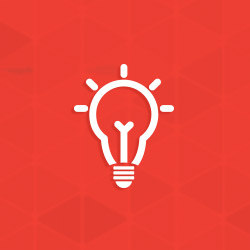
HDG vs. Bare Steel for Buried Solar Posts
Is HDG Necessary for Buried Solar Posts?
As the typical design life for solar farm infrastructure is 25-50 years, hot-dip galvanizing (HDG) is a leading choice to provide durable corrosion protection and a reliable power source while combatting constant exposure to the sun’s unforgiving heat and UV rays. Unaffected by UVA and UVB rays, hot-dip galvanized steel is often utilized for solar panel frames, mounts, and posts where the maintenance-free longevity achievable in atmospheric environments (72-120+ years) is well beyond typical design requirements for these members.
What about below ground? The AGA publishes a chart for estimating HDG performance in soil based on real world corrosion data and the main factors that dictate the corrosivity of zinc in soil: moisture content, pH level, and chloride content. In most soil conditions, hot-dip galvanized steel provides a service life over 75 years. The best soil types for hot-dip galvanized steel are sandy, coarse soils with low retained moisture levels, while the worst soil types for hot-dip galvanized steel are dense soils with high retained moisture levels and swampy soils with high moisture and low pH values.
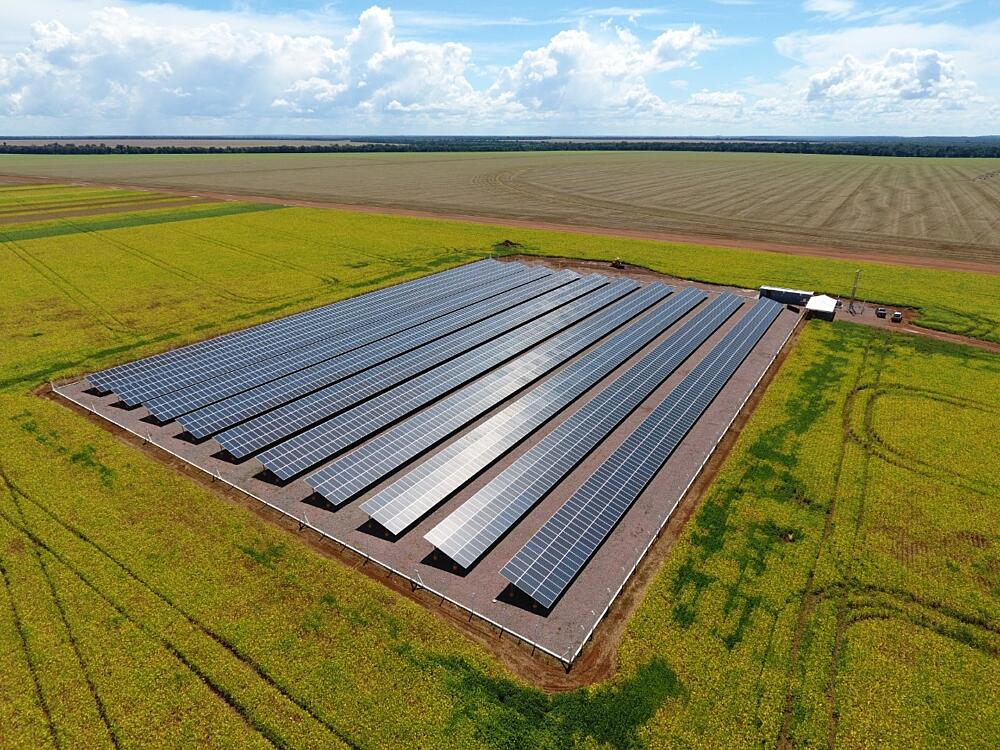
With an understanding of the maintenance-free longevity HDG can provide, it can be tempting to consider bare steel, a higher steel grade, or corrosion-resistant steel alloys for solar projects in rural and/or desert climates in lieu of hot-dip galvanizing. However, efforts to save slightly on initial cost for a corrosion protection system where soil conditions seem favorable can lead to unintended consequences while the benefits of hot-dip galvanizing a solar project is demonstrated:
- With more than 200 different types of soil identified in North America, the corrosion rate of steel in soils is varied and hard to predict with certainty when extrapolating from corrosion models to justify the use of uncoated steel. Further, increased steel thickness will increase longevity somewhat but it will not change the corrosion rate of steel. Meanwhile, HDG provides demonstrated longevity to meet typical solar infrastructure design life requirements and additional insurance to ensure a maintenance-free project 1, 2
- Bare steel embedded in soils of low corrosivity are not fully protected in instances where solar structures are installed downwind from a chemical plant or exposed to airborne pollutants. Meanwhile, hot-dip galvanizing provides durable corrosion protection above ground, below ground, and the transition zone.
- Inspection is simplified since the presence of steel corrosion is very easily distinguished from the presence of the galvanized coating.
- HDG provides additional protection against pitting corrosion. The area-averaged corrosion rates of galvanized steel are 3-6 times lower than those of bare steel in the buried environments surveyed, but the pitting corrosion rates of galvanized steel are 4-20 times lower than those of bare steel in the same environment. 3
- A great percentage of solar utilities are placed in deserts where environmental corrosion is low, but abrasion can be high due to strong winds. Hot-dip galvanizing increases abrasion resistance though increased material thickness and material hardness. Three of the four individual coating layers are harder than the underlying steel making it incredibly difficult to damage even during burial.
- The hot-dip galvanizing finish remains durable through rough handling during shipping, installation, and in-service.
- Hot-dip galvanizing is unaffected by continuous exposure to extreme temperatures between -40 F and 392 F, making it suitable for rugged and isolated climates.
The future of solar energy is also an exciting field of innovation. Should technological advances require installation upgrades that require full replacement of all steel support structures, hot-dip galvanized posts will be in good shape to re-use (or in harsher conditions, re-galvanize) for the next generation of solar posts, saving time and money down the road.
When the time comes to specify a new solar field project, consider hot-dip galvanizing as a strategic corrosion protection system for keeping our solar energy infrastructure corrosion free and environmentally friendly for generations to come.
Examples of successful batch hot-dip galvanized solar panel projects in North America can be found within the AGA Project Gallery:
Footnotes:
- Corrpro Companies, Inc. (1991). Condition and Corrosion Survey on Soil Side Durability of Corrugated Steel Pipe: Final Report. Prepared by Corrpro Companies for the National Corrugated Steel Pipe Association (NCSPA) in cooperation with the American Iron and Steel Institute (AISI).
- Kinstler, T. (2002).Major Factors Influencing Soil Corrosivity [PowerPoint slides]. American Galvanizers Association TechForum Conference. Toronto, ON, CA.
- Zhang, X. (1996).Corrosion and Electrochemistry of Zinc; Plenum Press: New York, NY, U.S.A.
© 2025 American Galvanizers Association. The material provided herein has been developed to provide accurate and authoritative information about after-fabrication hot-dip galvanized steel. This material provides general information only and is not intended as a substitute for competent professional examination and verification as to suitability and applicability. The information provided herein is not intended as a representation or warranty on the part of the AGA. Anyone making use of this information assumes all liability arising from such use.