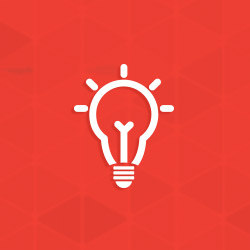
Examples of Natural Weathering on HDG Appearance
Natural weathering and the formation of the zinc patina will minimize many discrepancies with HDG appearance, but how much change can be expected?
Shortly after hot-dip galvanizing, coatings can take on a variety of initial appearances. The AGA produced several resources to help navigate the reasons why different appearances occur and ways to minimize or mitigate issues with appearance. For more information, please see the AGA’s Appearance webpage. It’s important to remember aesthetics alone are usually not grounds for rejection and with time, nearly all aesthetic discrepancies disappear with the natural weathering process. To demonstrate the effect on various initial coating appearances and products the AGA has gathered a handful of before-and-after examples.
The Jesup bridge in Iowa was galvanized in 2014 and required progressive dipping for the large beams. In practice, progressively dipped articles result in a notably dark and rough overlap area visible on the part. The resulting progressive dip lines were photographed both during installation (Figure 1) and shortly after the bridge was opened to the public (Figure 2). One decade later, an AGA member returned to photograph the progressive dip lines to document and compare the difference in appearance resulting from 10 years of natural weathering (see Figures 1, 2, 3 & 4). Initially, the progressive dip lines had a dark appearance and rough texture compared to the surrounding coating appearance, but after 10 years of weathering, the progressive dip line softened greatly as the zinc patina developed and provided a matte-gray color.
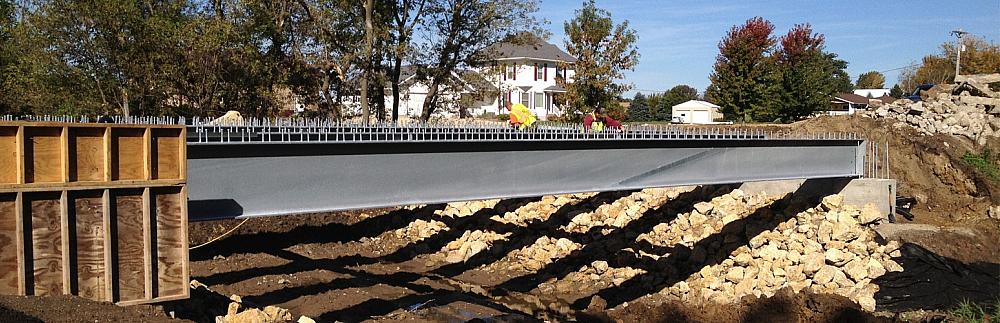
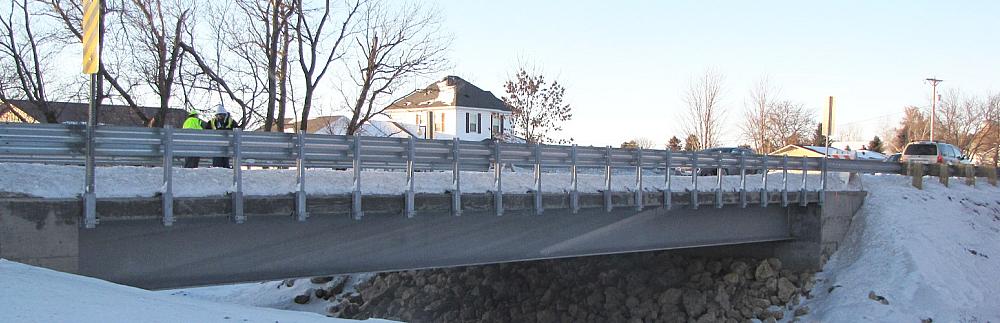
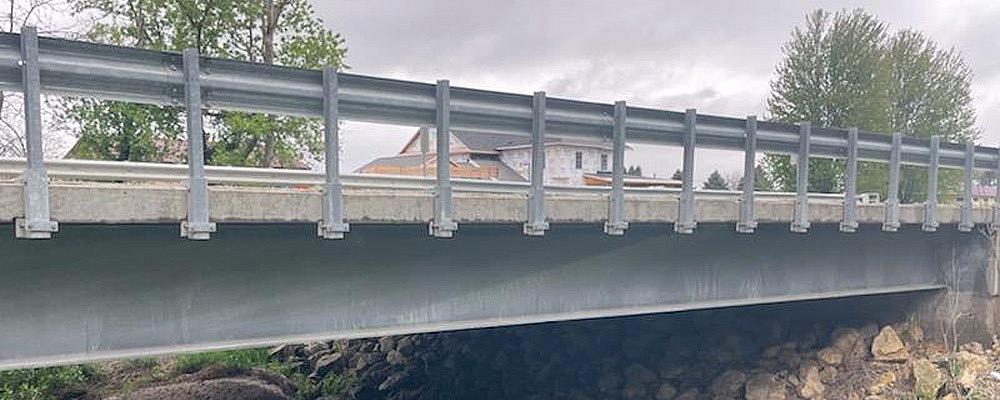
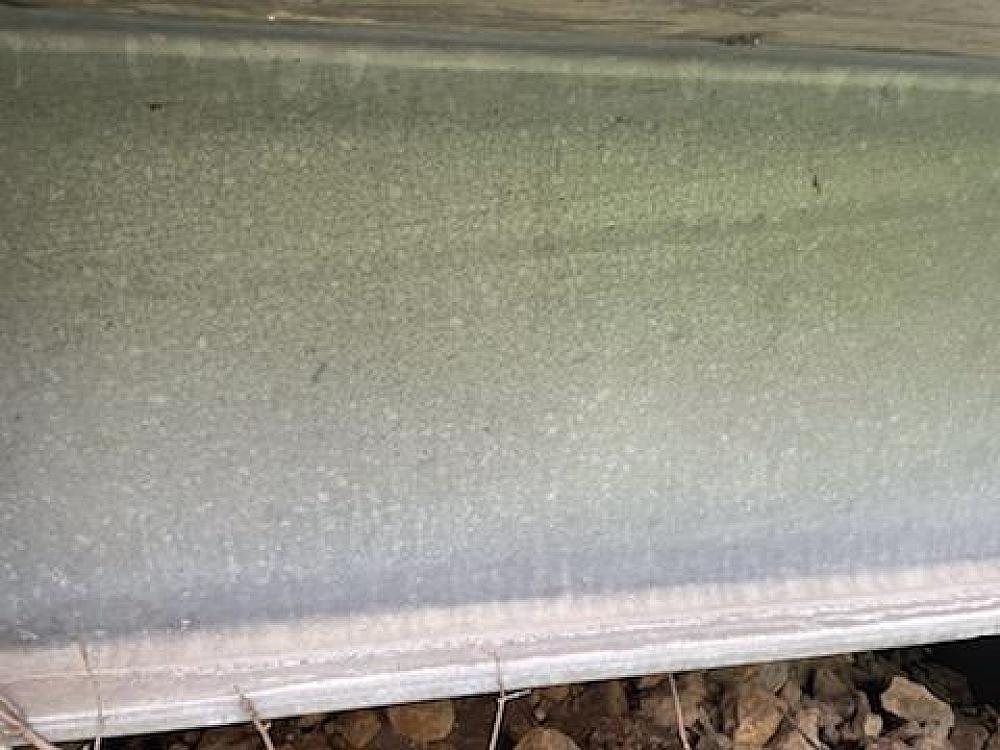
One great example of HDG weathering came from an AGA member in Coteau-du-lac, Canada. A newly galvanized transmission tower was installed next to another, fully weathered, galvanized transmission tower in December 2019 (Figure 5 left). This provided the opportunity to observe the changing appearance over the years, resulting in nearly identical coatings on both transmission towers 4 ½ years later in 2024 (Figure 5 right).
Figure 6 shows two pieces of guardrail, one shiny and one matte-gray on the left. These two pieces were galvanized in the same batch on the same day. The guardrail section on the right was stored under cover and exposed to free-flowing air, while the section on the left was exposed to moisture (humidity or rain) but no free-flowing air and developed wet storage stain. After installation, the two pieces were allowed to weather naturally. On the right, figure 6 shows the same two guardrail sections after a little more than three months exposure. Once the pieces were allowed to weather naturally, not only the appearance but also corrosion protection of both sections is identical.
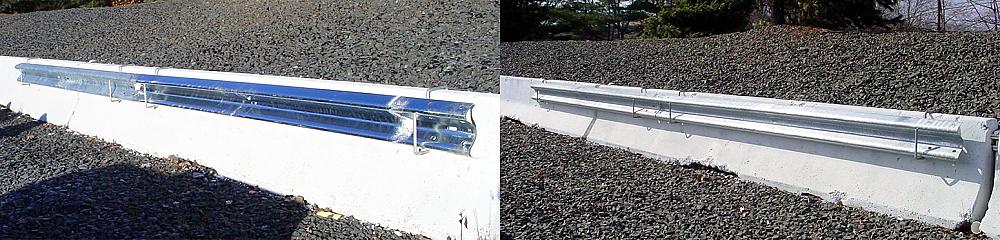
Another example of natural weathering is the canopied walkway at Mark Twain Elementary in Riverside, CA. The original canopies installed had coating variances - matte and shiny on the same beam. After a few years, the structure was revisited to check the performance, and the difference in appearance had evened out to a uniform matte gray.

One final example shows how repair materials can weather differently than the surrounding hot-dip galvanized coating. The pedestrian hand railing on the George Washington Bridge, in Fort Lee New Jersey, was initially touched up with a shiny zinc-rich paint matching the qualities of the unweathered zinc coating. However, as you can see in Figure 8, the surrounding galvanized coating lost its luster over time, causing the still-shiny repaired areas to stand out against the fully weathered patina. Generally, shiny zinc-rich paints don’t weather out or change in appearance while matte gray zinc-rich paints will. Repairs and touch-ups made by metallizing or zinc solder will weather fully and develop a zinc patina.
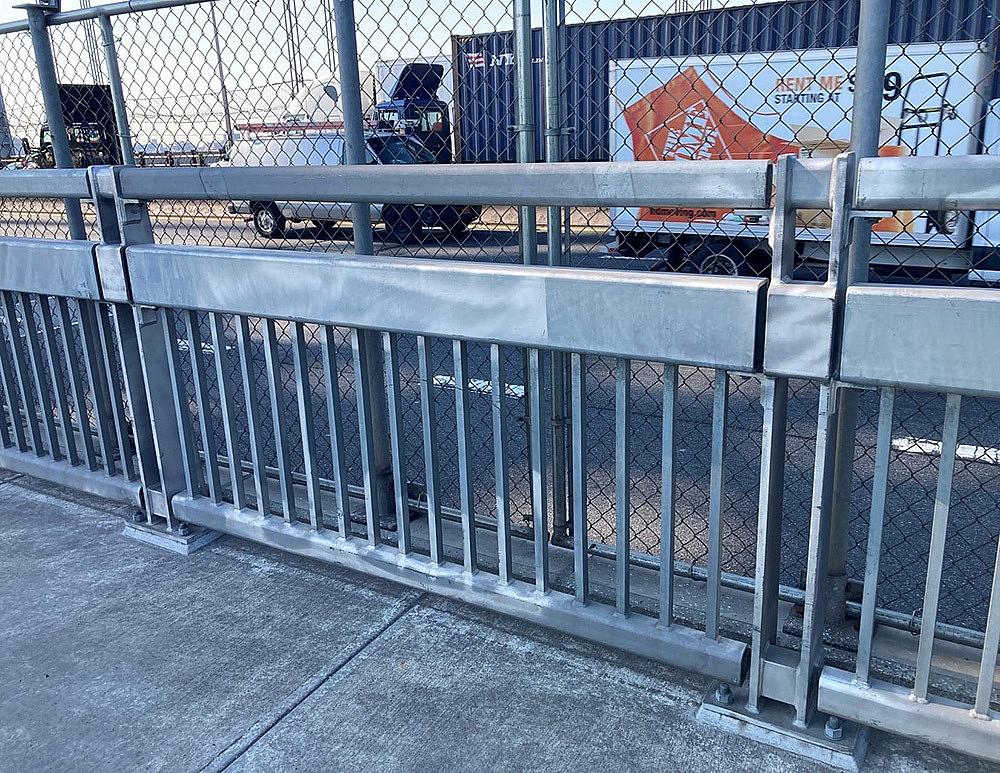
See these resources for additional information on HDG Appearance and natural weathering.
© 2025 American Galvanizers Association. The material provided herein has been developed to provide accurate and authoritative information about after-fabrication hot-dip galvanized steel. This material provides general information only and is not intended as a substitute for competent professional examination and verification as to suitability and applicability. The information provided herein is not intended as a representation or warranty on the part of the AGA. Anyone making use of this information assumes all liability arising from such use.