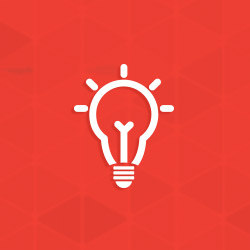
Yes, A 100-Year Bridge Is Real
As bridge designers and owners of public bridges have become more sensitive to sustainability issues and shrinking budgets, the concept of a bridge performing 100 years or more with minimal to no maintenance is a very real goal for them. This goes for all the structural components such as girders, beams, cables, but especially the decks. It is commonly understood hot-dip galvanizing can deliver 100-year corrosion protection for the structural steel in most atmospheric exposure conditions, but it is not well known hot-dip galvanized reinforcing steel in concrete exposure can do the same for decks.
The corrosion mechanics of zinc in concrete are very different from those of zinc in atmospheric exposure. Simply put, zinc on reinforcing steel in concrete forms a calcium hydroxyzincate film that passivates the underlying zinc immediately after the concrete pour. This reaction consumes only a few microns of zinc and ceases once the concrete cures. So, in addition to the barrier coating of zinc metal, there is a second barrier, namely the calcium hydroxyzincate. More significant than this passivation layer and the fact it is a second barrier coating is it will not begin corroding until the chloride concentration in the concrete reaches a threshold. Chlorides are introduced to the concrete via the application of road salts or salt-laden ocean air and eventually make their way to the rebar through cracks and/or concrete porosity.
There has been a lot of research over the years to quantify the chloride threshold for the onset of zinc corrosion. Laboratory findings using accelerated testing (chloride bath) indicate the threshold is somewhere between 2 and 4 times the threshold for the onset of corrosion of black reinforcing steel, which is 0.95 kg/m3. Galvanizing industry experts (Porter and Yeomens) cored actual bridge decks to obtain rebar samples in place for decades and observed the threshold to be 5 to 10 times that of black bar. AGA has cored bridges in Northern climates where road salts are regularly used and observed no corrosion of the zinc after 35 years, indicating the chloride threshold has yet to be reached.

Figure 1 shows the buildup of chloride ions over time for two bridges; one from a northern climate where road salts are the main source of chloride ions and one from a southern climate where natural salts from the ocean are the source of chloride ions. The high threshold for zinc coatings (conservatively 3.8 kg/m3 for these two cases) and the slow buildup of chloride ions means the corrosion of the zinc coating doesnt even begin for many decades and of course the substrate carbon rebar remains structurally intact.
Once the chloride ion threshold is exceeded, the zinc coating begins to corrode. The corrosion rate of the zinc in concrete has been studied and is approximately 3 microns/year. This corrosion rate depends on many factors; the amount of moisture in the concrete, the wet/dry cycles, the cracks in the concrete, the concrete cover thickness, and additives to the concrete mix are the most important factors. The total time for the zinc to corrode is also very dependent on the initial zinc coating on the reinforcing bar. Once the zinc has completely corroded, the steel becomes exposed to the chloride ions and begins the final cycle of corrosion where the steel turns into rust (iron oxide) and, eventually causes the concrete to spall.
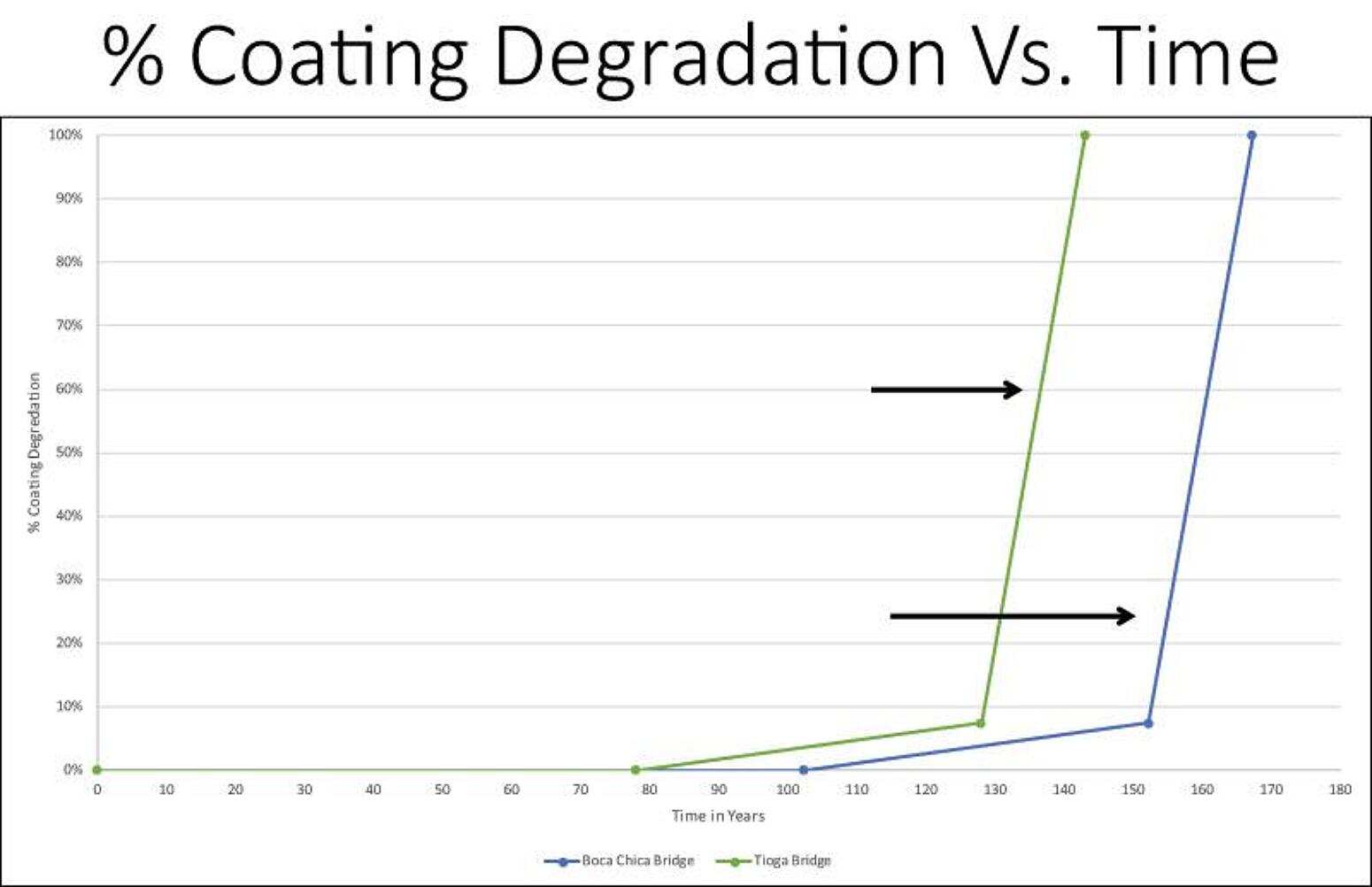
For the two bridges cited in Figure 2, (one located in a northern U.S. climate where substantial road salts are used, and the other in a marine environment where the chloride source is the ocean air and wind initiated spray) the coring samples taken over the past 25 years indicate the chloride ion threshold will not be reached until year 78 and 102, respectively (see the intersection of the lines with the X-axis). Then, the zinc corrodes at about 3 microns per year until it is completely consumed, roughly at year 128 and 153, respectively. Then, the steep slope of the curve begins, which indicates carbon steel corrosion.
But what about the zinc corrosion products when the chloride threshold is finally reached? Do they cause outward pressure on concrete resulting in cracks and spalling? The answer is no as determined by the 100x and 1000x microscopic views of actual zinc corrosion in concrete as seen in Figure 3. Zinc corrosion products are much less voluminous than iron-oxide and simply fill the voids in the concrete adjacent to the surface of the rebar. This delivers an additional benefit in that the concrete is now more dense, allowing less chloride ions to make their way to the bar surface.
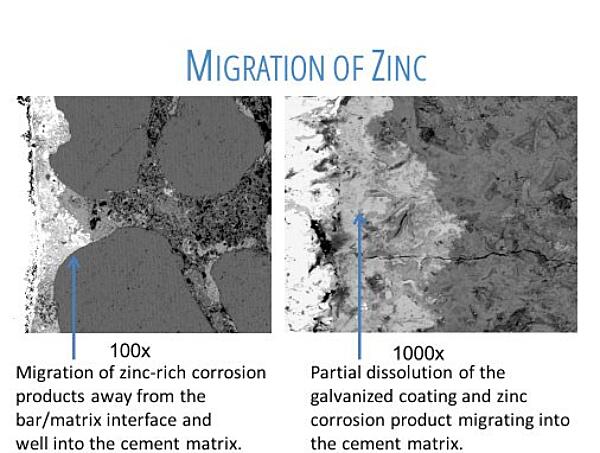
So, it is important to emphasize the galvanized rebar IS NOT the cause of concrete cracking and spalling of the concrete. Only after about 100 years and the complete corrosion of the zinc does the carbon rebar itself corrode and then lead to concrete failure.
In Summary:
- Zinc on the rebar will not begin to corrode until the chloride threshold of approximately 3.8 kg/m3 is reached, typically 70 80 years after installation.
- The time to initial carbon rebar corrosion after the threshold is reached is a function of the amount of zinc on the bar.
- Hot-dip galvanizing will protect carbon rebar far longer than the typical service life of the concrete cover applied.
© 2025 American Galvanizers Association. The material provided herein has been developed to provide accurate and authoritative information about after-fabrication hot-dip galvanized steel. This material provides general information only and is not intended as a substitute for competent professional examination and verification as to suitability and applicability. The information provided herein is not intended as a representation or warranty on the part of the AGA. Anyone making use of this information assumes all liability arising from such use.