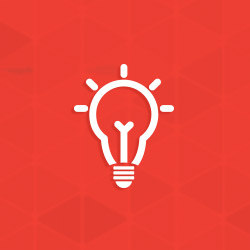
Progressive Dipping of Large Poles
Is there any concern with internal corrosion of tubular products galvanized using the progressive dip method?
Hot-dip galvanizing is a complete immersion process, which means the parts must fit in the zinc bath to be coated. In North America, the average kettle length is 40 feet, but there are many 50-60 foot long kettles with depths ranging from 6-12 feet, and widths ranging from 5-8 feet. Progressive dipping is one method considered for galvanizing oversized articles, but at least half the article must fit within the dimensions of the kettle. Then, progressive dipping is accomplished by sequentially running each end of the article through the galvanizing process, to coat the entire item.
Progressively dipped pieces often have an overlap area that is visible on the piece. After bringing the first end through the galvanizing process, the second end is also chemically cleaned and galvanized, where additional immersion of an overlapping area ensures full cleaning and coating coverage despite the rough coating edge produced from the first immersion. Owners should be made aware the overlap area often appears darker, develops a thicker coating, and may not weather consistently with the rest of the product. However, the presence of this line does not affect the overall coating performance. The overlap line can be buffed or ground down even with the surrounding coating to improve aesthetics or if the raised overlap area will be an important connection point with other pieces.
Concerns have risen in the past regarding corrosion at overlap lines which were not sufficiently cleaned when the second end is processed through the galvanizing line. For example, there was an isolated incident of premature HDG failure in Arizona where transmission tower poles (46 to 120+ feet in length) were galvanized for the Arizona Public Service (APS). In 1988, APS discovered a significant number of poles developed severe through-wall corrosion (Figure 1). The poles in question were only in service for 11 years before signs of severe corrosion were noticed in a normally low-corrosivity environment.
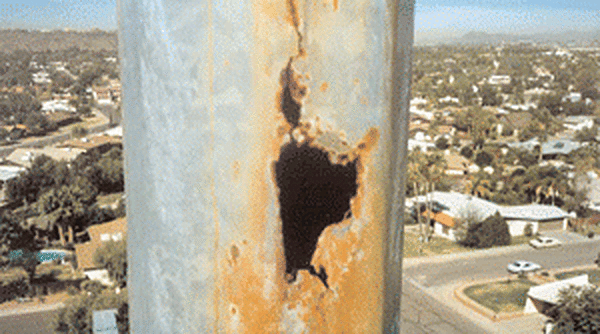
The accelerated corrosion initiating from the interior of the poles was a result of flux entrapment caused by the combination of progressive dipping with:
- Poor venting/drainage hole design The structure had only small vent holes and, in many cases, more severe corrosion was found on sections where end plates had been welded to the tubes, further limiting the flow of fluxing solutions and zinc. Additionally, since the vent holes were sealed, moisture resulting from condensation wetted the flux residues, causing corrosive chemical solutions to run the length of the interior.
- Wet galvanizing In this process, a molten flux blanket floats on the molten zinc in the kettle. A part is passed through the blanket upon submerging into the kettle, and the blanket is then paddled back upon removal from the kettle. Any floating flux that may become attached to the part must be removed.
When a tubular product is progressively dipped using a wet kettle process, the chance for flux entrapment is high. However, over time the galvanizers in North America have moved away from wet kettles and toward the “dry galvanizing” process where fluxing is performed separately before immersion in the kettle (Figure 2).
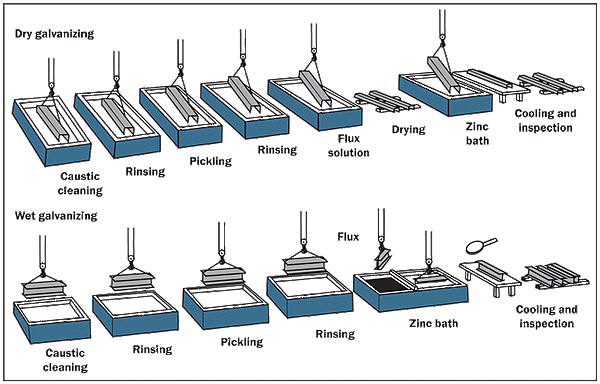
Currently, very few wet kettles remain in service. When a tubular product with proper venting/drainage holes is progressively dipped using a dry kettle, the progressive dip process does not result in concerns over internal corrosion of tubular products due to flux entrapment. As a result, progressive dipping of tubular products is now commonly and successfully performed in the industry today.
For the galvanizing of utility poles and H-frames greater than 40-50 feet long where progressive dipping is required to fully coat the structure, best design practices for venting and drainage to mitigate against flux entrapment can be obtained from the specification ASTM A385 Practice for Providing High-Quality Zinc Coatings (Hot-Dip), or through the AGA publication Design of Products to be Hot-dip Galvanized After Fabrication.
© 2025 American Galvanizers Association. The material provided herein has been developed to provide accurate and authoritative information about after-fabrication hot-dip galvanized steel. This material provides general information only and is not intended as a substitute for competent professional examination and verification as to suitability and applicability. The information provided herein is not intended as a representation or warranty on the part of the AGA. Anyone making use of this information assumes all liability arising from such use.