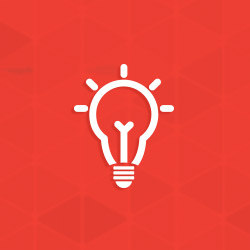
Entrapped Flux on Progressively Dipped Tubes
I have a customer who would like to galvanize some tubular products for use in transmission line applications. He likes HDGs maintenance-free service life, but has heard some horror stories about galvanizing long tubular productstransmission line poles in particular. Is there any truth to such stories?
Your customer does have some validity to his claims but provided good galvanizing and design practices are followed, a quality product can be achieved. There was an isolated incident of premature HDG failure in Arizona in 1988 . . . Transmission tower poles located near and running through Phoenix, ranging from 46 to 120+ feet in length, were galvanized for the Arizona Public Service (APS). In 1988, APS discovered that a significant number of poles had developed severe through-wall corrosion. The poles in question were only in service for 11 years before signs of severe corrosion were noticed and some poles were structurally failing. Arizona is typically considered a low corrosion environment, as its limited rainfall and low amounts of pollution lend to long service lives for galvanized material. What could be the cause of this unusual corrosion behavior?
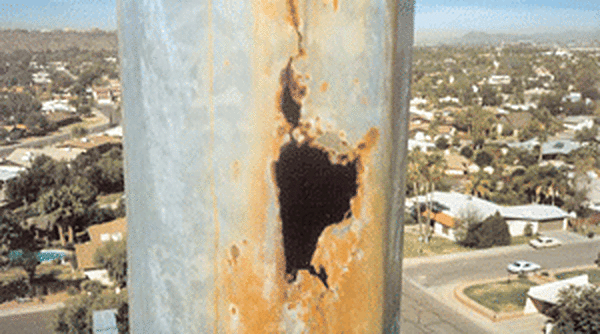
An AGA task force assembled (at this time the ADHGA). At a meeting with the APS, local galvanizers, and ADHGA, a foot section of a failed pole was presented to initiate discussion about the possible reasons for the premature failure. The tubes interior was completely corroded away in layers from the inside outward, leaving only a thin outer shell in places. The piece in question had a top plate seal-welded to the pole section, and two venting holes were positioned near the baseopposing each other3/4" in diameter which were sealed after galvanizing with HDG plugs. APS had a chemical analysis performed on the corroded materials found on the interior of the poles, and they were determined to be rich in the chemical constituents of flux. The evidence prompted a field trip to the transmission line site. An on-site inspection revealed the poles had been progressively dipped, as a visible dip line was observed. Pole tappingan inspection where the inspector hits the pole with a hammer and listens carefully for the sounds of dropping corrosion productsdiscovered corrosion throughout the line. The poles were basically sealed, preventing airflow from the exterior to the interior of the poles.
The accelerated corrosion initiating from the interior of the poles was a result of flux entrapment. The following three steps contributed to the corrosion and flux entrapment:
- Poor venting The structure had only small vent holes and, in many cases, more severe corrosion was found on sections where end plates had been welded to the tubes, further limiting the flow of fluxing solutions and zinc. Additionally, since the vent holes were sealed, moisture resulting from condensation wetted the flux residues, causing corrosive chemical solutions to run the length of the interior.
- Wet galvanizing In this process, a molten flux blanket floats on the molten zinc in the kettle. A part is passed through the blanket upon submerging into the kettle, and the blanket is then paddled back upon removal from the kettle. Any floating flux that may become attached to the part must be removed.
- Progressive dip This operation involves the dipping of articles that are too large to be galvanized fully in one dip. In this process, half of the article is lowered into the kettle first, removed, and then the other half is dipped, completing the galvanized coating.
These three factors added up to a case of extreme corrosion in an environment not typically characterized as corrosive. When a tubular product is progressively dipped in a wet kettle process, the chance for flux entrapment is high. As these long tubes were lowered into the bath on the first dip, the small vent holes allowed for minimal draining of the included flux. The second dip compounded the problem as flux was entrapped at the dip line. With no interior clean-up following galvanizing, these corrosive elements were left on the surface of the poles, and the vent holes were then sealed following the progressive dip. With the changing temperatures, condensation and moisture became trapped on the interior of the poles, wetting the flux, and creating acid-like corrosive liquids that rapidly consumed the galvanized coating and the steel itself.
APSs visual inspection of the poles in service resulted in the replacement of questionable poles used in the transmission line. The ADHGA accompanied APS officials for the inspection of 184 pole sections that were scheduled to be installed; 60 poleseach showing progressive dip lineshad severe flux contamination, the corrosion on which was concentrated around the dip lines. Both the galvanizer and the APS agreed upon the treatment of the affected poles, which required the cleaning and removal of foreign materials, followed by repair of the galvanized coating.
© 2025 American Galvanizers Association. The material provided herein has been developed to provide accurate and authoritative information about after-fabrication hot-dip galvanized steel. This material provides general information only and is not intended as a substitute for competent professional examination and verification as to suitability and applicability. The information provided herein is not intended as a representation or warranty on the part of the AGA. Anyone making use of this information assumes all liability arising from such use.