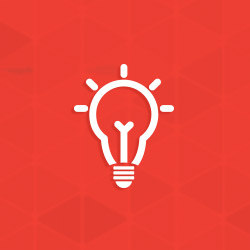
HDG Rebar and Avoiding Hydrogen Evolution
I’ve heard zinc reacts with concrete during the curing phase…does this affect the bond strength and how does it affect the corrosion resistance of the HDG rebar?
Upon initial contact, fresh zinc will try to protect itself from the wet, alkaline concrete mixture by forming calcium hydroxyzincate to protect it from further corrosion. This reaction also produces hydrogen gas at the rebar–cement paste interface which can possibly reduce the bond strength.
The good news is this reaction is easily and commonly mitigated by two methods. As long as this reaction is suppressed, bond strength is not affected and the galvanized rebar bond strength is equal or higher than black steel bond strength, and greater than epoxy rebar bond strength.
The first method is to apply a chromate passivation treatment after HDG. This controls the reaction while the concrete cures. This is the method required by rebar galvanized to ASTM A767 or ASTM A1094 standard unless waived by the specifier. According to a study conducted by the AGA, the presence of a chromate passivation coatings applied to HDG were found to last from 45 days (6 1⁄2 weeks) to 98 days (over 3 months). As a result, you should consider whether the rebar will be placed within several weeks time. If needed, you can test for the presence of a passivation coating in accordance with ASTM B201, Standard Practice for Testing Chromate Coatings on Zinc and Cadmium Surfaces.
The second method is to ensure a sufficient amount of chromates are present in the wet cement mixture to limit the reactions. Although there is some variability of naturally existing chromate levels in the final concrete mix of domestic suppliers, it is possible to test for total chromate ahead of time to confirm. Most domestic mixtures already contain at least 20-30ppm total Chromate and have demonstrated practical success in limiting zinc reactions in concrete. Chromate levels tend to only be a concern when sourcing is from international suppliers using no chromate, or domestic suppliers replicating that international practice. If it is necessary to add chromates afterward, aim for a total chromate content in the paste cement of 100ppm minimum, but values between 50-100ppm are specified with success. Chromate additions are typically performed by adding chromate salts or dilute chromic acid.
This method can be used in situations where:
- The chromate passivation weathered after sitting out a few months
- Chromate passivation coatings are not allowed due to environmental restrictions
- Chromate passivation coating is waived by the specifier (A767 and A1094), or is not specified (A123 for rebar fabrications).
Method two is widely used in the pre-casting industry. Most domestic cement mixtures already contain sufficient levels of chromate to control zinc reactions. Because of this, you may sometimes see the requirement for a chromate quench within ASTM A767 or A1094 waived. Best practice is to confirm with your supplier and/or test the cement paste for total chromate, especially if using an international supplier where the use of chromates is prohibited or unlikely.
© 2025 American Galvanizers Association. The material provided herein has been developed to provide accurate and authoritative information about after-fabrication hot-dip galvanized steel. This material provides general information only and is not intended as a substitute for competent professional examination and verification as to suitability and applicability. The information provided herein is not intended as a representation or warranty on the part of the AGA. Anyone making use of this information assumes all liability arising from such use.