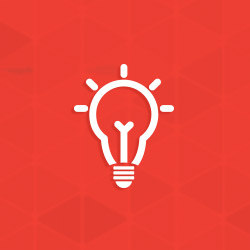
AGA Studies Impact of Abrasive Blasting Before HDG on Coating Thickness
Is abrasive blasting before HDG worth the added cost to control thick coatings?
Blast cleaning before galvanizing is often specified to roughen the steel surface and promote thicker galvanized coatings for low-silicon or Aluminum-killed steels, whereas blast cleaning before galvanizing is also a method used to limit coating thickness for reactive steel chemistries. The difference in outcome is due to the initial steel chemistry. Galvanizers and specifiers use this information to identify projects where a strategic use of abrasive blasting before galvanizing may be a worthwhile additional cost for certain projects.
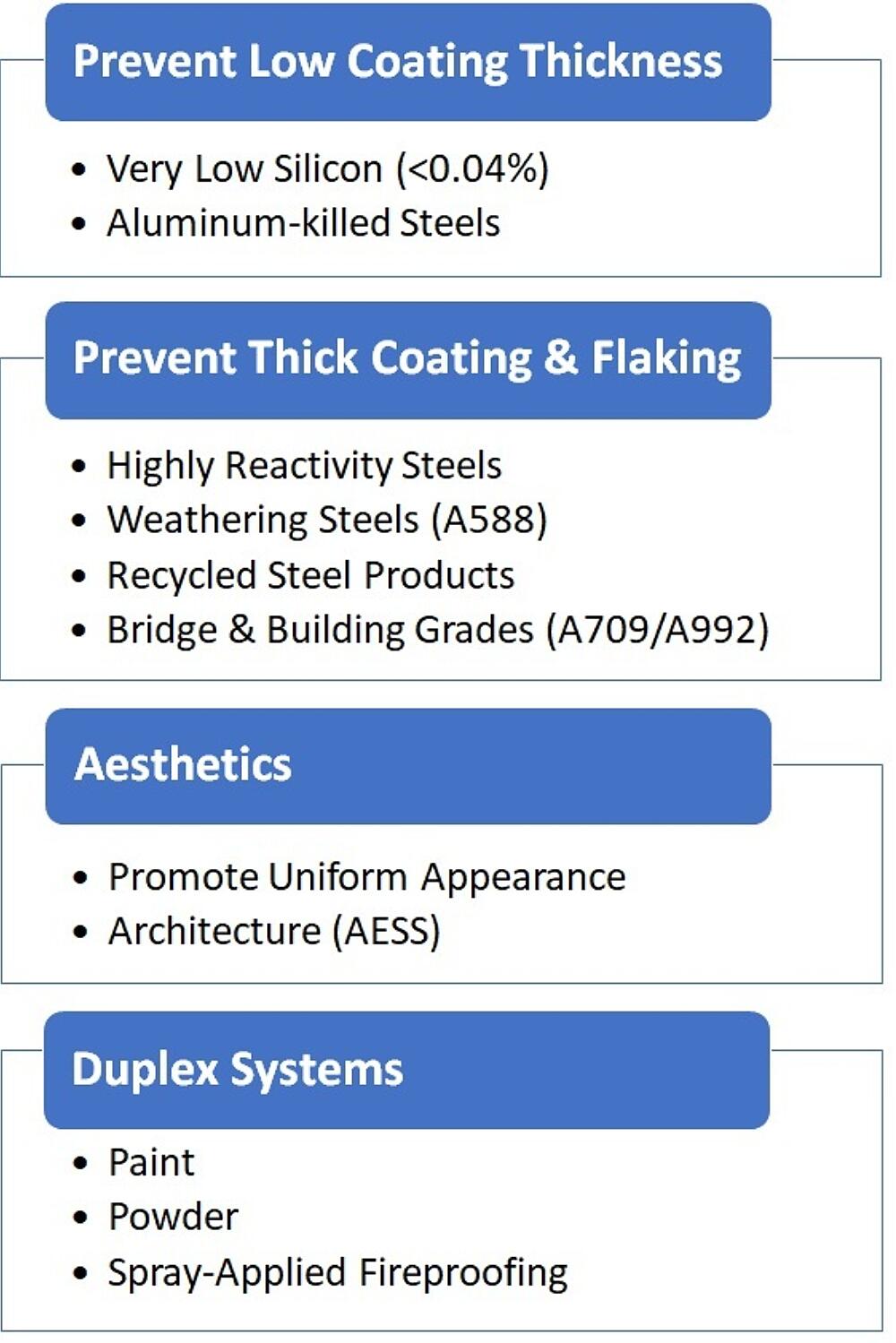
However, the reason for this contradiction and the amount of reduction/increase possible is not fully determined. As a result, the AGA began a test program in September 2021 to quantify these benefits for steels grades known to exhibit either low coating thickness or exhibit thick, brittle coatings which are susceptible to flaking concerns. Thick, brittle coatings are more prevalent when reactive steels form excessive HDG coating thickness above 8-10 mils. The goals of the AGA study are to:
- Perform a literature review: gather all existing research on this topic
- Demonstrate and quantify the outcome of abrasive blasting before HDG based on steel chemistry
- Define practical examples where abrasive blasting before HDG may be more cost effective up-front than remedying potential quality issues due to thick, brittle HDG coatings
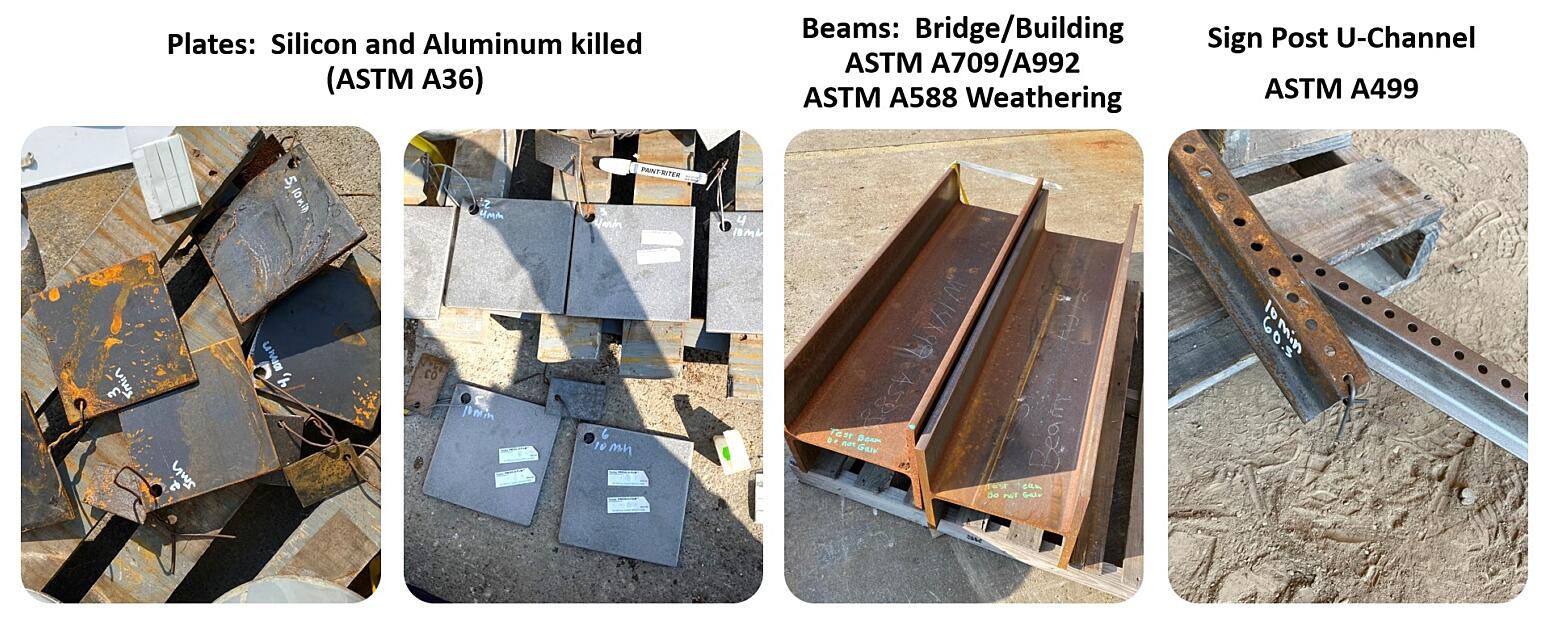
Steel samples were gathered to represent different material types and steel chemistries for testing (Figure 2). These samples also represent steel from markets where abrasive blasting before galvanizing is more commonly considered to control coating thickness. Half of each test material surface was blasted with steel grit (G25) before galvanizing to compare coating thickness variations present on blasted vs. unblasted areas of the same part. Abrasive blast cleaning before galvanizing does not require the specification of a degree of cleanliness nor specific profile parameters, however, Commercial Blast Cleaning in accordance with SSPC-SP 6/NACE No. 3 was used as a guide. A profile height of 3 mils was achieved on all plates and beams while a profile height of 2 mils was achieved on the signpost structures. Multiple replicates of each were run together using a normal dip time, while an identical second batch was galvanized for an extended time (doubled immersion times) to observe the potential impact of immersion time.
A summary of the study results is provided in Table 1 which defines where blasting has an effect on coating thickness development based on the initial steel chemistry.
Table 1: Preliminary Results of AGA Blasting Before Galvanizing Study (2021)
Reactivity |
Impact of Blasting Before HDG on Coating Thickness |
Low-Reactivity Steels Silicon < 0.04 % |
Increases coating thickness Significant increases possible Dip time has little effect |
Sandelin-Range Steels Silicon 0.04% – 0.15% |
Increases coating thickness Negligible or minor increase possible (short dip time) Greater increase possible (longer dip time) |
Slightly Reactive Steels Silicon 0.22% – 0.25% |
Negligible effect on coating thickness possible Minor decreases (5-10%) possible |
Highly Reactive Steels Silicon > 0.25% Or Recycled Steels |
Minor decreases possible (short dip time) Significant decreases (>35%) possible (longer dip time) *Investigation of more steels in this range needed |
Generally speaking, abrasive blasting before hot-dip galvanizing was found to significantly affect the coating thickness when galvanizing either very low-silicon or Aluminum-killed steels to increase coating thickness; or when used to reduce coating thickness on highly reactive steel and reactive steels that are susceptible to longer immersion times. Longer immersion times can occur for thick steels, reactive steels that are combined within a welded assembly, hollow items with poor venting/drainage hole placement and sizing, and more.
On the other hand, steels of recommended chemistry, steels that are only slightly reactive, or thin materials that will not be in the kettle for extended immersion times (regardless of steel chemistry) may not benefit significantly from abrasive blasting before galvanizing to limit the HDG coating thickness. In fact, sometimes the coating thickness may be increased slightly. This practice may drive up the cost unnecessarily in these cases unless primarily specified to achieve elevated aesthetics where the additional cost is otherwise justified.
Blasting before galvanizing is just one method in the tool kit that may bring benefits for certain steels or projects. Additional methods to reduce immersion times and limit coating thickness are also available:
© 2025 American Galvanizers Association. The material provided herein has been developed to provide accurate and authoritative information about after-fabrication hot-dip galvanized steel. This material provides general information only and is not intended as a substitute for competent professional examination and verification as to suitability and applicability. The information provided herein is not intended as a representation or warranty on the part of the AGA. Anyone making use of this information assumes all liability arising from such use.