Hydro-Electricity
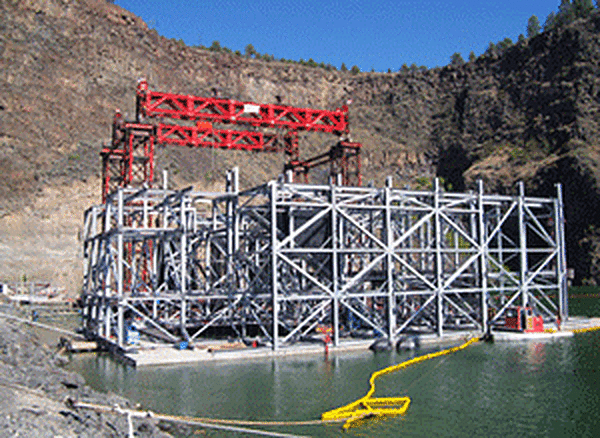
Large scale hydro-electric plants have long been a reliable means of generating renewable energy still accounting for 88% of renewable energy sources worldwide. Hydro-electric power accounts for roughly 7% of the United States' power needs and over 20% of the world's energy needs.
Hydro-electric dams and projects are often large undertakings that take years to complete; however, once in service, such structures can often be used for 50-100 years. Hydro-electric projects often outlast the economic life of a fuel-fired plant, so when designing and constructing the plant it is critical to protect the investment to ensure it has the longest service-life possible.
Moisture protection is of utmost importance in this type of project, where corrosion is a major consideration in the design and production of a dam. Pipes and penstocks are perhaps the most essential elements of a hydroelectric facility, channeling water through the process to create clean energy. These pieces are often large and unwieldy, in addition to being difficult to access; because of these challenges, a low-maintenance corrosion protection system is a necessity to keep the water flowing and plant operations uninterrupted.
Unlike many corrosion protection systems that only protect the outer layer of a pipe, hot-dip galvanizing protects piping from the inside out. As a hollow pipe is lowered into the molten zinc during the galvanizing process, the zinc flows inside the hollow structure, completely covering the inside of the pipe as well as the exterior. This zinc coating, which is metallurgically bonded to the steel, grows perpendicular to all surfaces creating a consistent barrier across the entire piece that will stand strong against moisture-related corrosion. Whether a pipe is exposed to the sitting water of a lake or reservoir or water flowing through on its way to become energy, galvanizing protects from corrosion both inside and out.
Often, a dam can recoup the costs of initial construction after just 5-8 years of full generation. To capitalize on the early return on investment, it is important to utilize low maintenance materials in the plant to avoid costly shutdowns and new installation costs in the future. Because hot-dip galvanizing (HDG) performs well in moisture-rich environments, it is an obvious choice for corrosion protection in the construction of hydro-electric facilities and equipment.
Hydro-Electricity Case Study
Clackamas Hydro Project- Estacada, OR; 2014
This portion of the Clackamas Hydro Project is a two phase project who's ultimate goal is to safely insure a 97% survival rate for wild fish attempting to complete their life-cycle journey with minimal human disturbance.
This first phase of the project includes human access ways, supporting structures for human access and fish diverter lines, fish diverter flow control station, debris filtration, and overflow control into the existing historical flues built for transport of wild fish.