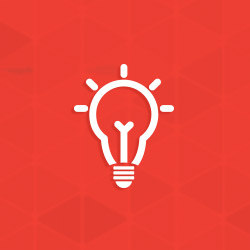
Zinc Coatings for Fasteners
How are zinc plating, mechanical galvanizing, high temperature galvanizing, or thermal diffusion galvanizing different than HDG?
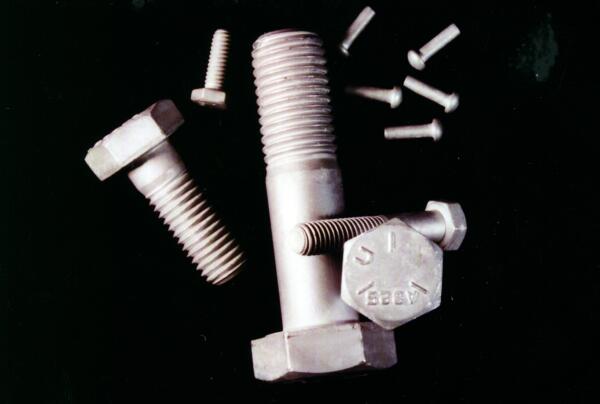
There are various methods of applying zinc coatings to fasteners and hardware items which are often marketed as equal to or better than hot-dip galvanized (HDG) fasteners. In reality, the longevity of all zinc coatings (regardless of application method) is directly related to coating thickness, and abrasion resistance is affected by a metallurgical vs. mechanical bond to the steel. However, there are pros and cons to each zinc coating application process.
Having a working knowledge of other zinc coatings is valuable when customers have specific concerns regarding paintability, precise fit-up, embrittlement, or appearance. Below is a summary of several zinc coating application methods for fasteners that compete with hot-dip galvanizing in various markets.
Zinc Plating (Electroplating)
Zinc plating (ASTM B633) is identical to electro-galvanizing (electroplating) in principle because both are applied via the electro-deposition process. However, zinc plating is the specific electro-deposition terminology for fasteners. Zinc plating provides an economical zinc coating consisting of pure zinc which is tightly adherent to the steel, very smooth, and often bright/shiny in appearance.
As typical coating thicknesses range from 0.2 - 0.5 mil, time to first maintenance is significantly less than can be achieved using hot-dip galvanizing. Zinc plated fasteners are considered appropriate for small fasteners used in interior applications or mild external environments. Zinc plated fasteners used in moderate applications are often post-treated with a chromate conversion coating to improve longevity or to affect the appearance (color). Typical conversion coatings may be clear or slightly blue (known as zinc clear or blue zinc), iridescent yellow (known as yellow zinc, zinc di-chromate, zinc-yellow chromate, or zinc plate gold), or black (known as black oxide, black chromate, or black zinc).
Mechanical Galvanizing (Mechanical Plating)
Mechanical galvanizing (ASTM B695) is accomplished by tumbling small parts (less than 8-9 inches in length) in a drum with zinc, glass beads, and proprietary chemicals. During tumbling, the glass beads peen zinc powder onto the part. Once finished, the parts can be post-treated with a passivation film.
Mechanically galvanized fasteners can have a coating thickness similar to hot-dip galvanized fasteners, but the coating is thin near edges and underneath any head surfaces due to the physical limitations of the application process. While thicker coatings up to 4 mils (100 µm) are possible, the common thickness on commercial fasteners is 2 mils (50 µm). Mechanically galvanized fasteners tend to be matte gray and rough in comparison to zinc plated fasteners.
Mechanical galvanizing is often a viable alternative for fasteners of a very high ultimate tensile strength (>170 ksi) which may be susceptible to hydrogen embrittlement during HDG due to a tight grain structure trapping hydrogen molecules readily available from the pickling step, or for fasteners which have been heat-treated using a tempering temperature which is near or below typical hot-dip galvanizing temperatures.
High Temperature Galvanizing (HTG)
High temperature galvanizing (delta galvanizing) is a hot-dip coating process where steel is dipped in a zinc bath at 1040 - 1165 °F (560 - 630 °C) to form a coating comprised of a thin gamma layer with a compact delta layer on top. As a result, a very hard, rough, and thin coating is produced with similar properties to a traditional hot-dip galvanized coating. If desired, high temperature galvanizing can be controlled to produce coating thicknesses ranging from 1.0 - 3.1 mils (25 - 80 µm).
Although high-temperature galvanizing is not a common coating process seen in North America, in Europe high temperature galvanizing is typically specified for certain hardware items where both superior corrosion protection and precise fit-up (controlled coating growth) is required. Often times, the reason a customer may wish to high-temperature galvanize is when they have concerns over precise fit-up between parts, ease of painting over HDG, and/or abrasion resistance.
Thermal Diffusion Galvanizing (Sherardizing)
Thermal diffusion galvanizing (ASTM A1059) is a specific process for performing sherardizing that involves zinc powder and proprietary chemicals. Parts are cleaned and tumbled in a heated drum at temperatures slightly less than hot-dip galvanizing (680 - 825 °F) so that matte gray HDG-like intermetallic alloy layers are produced. The coating is thinner than HDG (1 - 3 mils) with no free-zinc layer on top. ArmorGalv® and Greenkote are proprietary methods for thermal diffusion galvanizing.
Thermal diffusion galvanizing can be desired for fasteners where a galvanized coating is desired but fit-up or alignment is critical, or for high strength fasteners susceptible to hydrogen embrittlement through the batch hot-dip galvanizing process (>170 ksi ultimate tensile strength). It is also specified for fasteners to be painted or powder coated since the coatings can be applied on the rough but uniform coating with minimal surface preparation. In North America, thermal diffusion galvanizing is specified for hardware items, but in Europe it is also applied to small parts and tubing/pipes. The overall process is more expensive than HDG, batch sizes are limited, and it can take six to eight hours to complete the coating application due to specification requirements.
A Note on Accelerated Testing
Claims that any of the above zinc coating methods are superior to HDG for fasteners stem from the results of accelerated testing, specifically the published results of various salt spray tests (ASTM B117, etc.) available from a competitors website. Accelerated testing performed for any zinc coating will not provide results which are consistent with real world performance. This is because the tests attack the wrong material (zinc metal instead of the self-protecting zinc patina it develops). As a result, such tests will give an incorrect prediction of the performance of zinc coatings in the real world. In addition, zinc coating thickness is directly related to longevity. Hot-dip galvanized fasteners galvanized to ASTM A153 standard provide a thicker coating of zinc than possible through these other zinc coating methods.
© 2025 American Galvanizers Association. The material provided herein has been developed to provide accurate and authoritative information about after-fabrication hot-dip galvanized steel. This material provides general information only and is not intended as a substitute for competent professional examination and verification as to suitability and applicability. The information provided herein is not intended as a representation or warranty on the part of the AGA. Anyone making use of this information assumes all liability arising from such use.