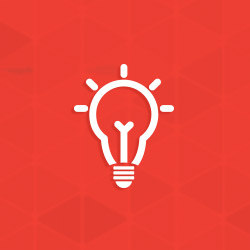
Revisions affecting HDG in the AASHTO LRFD Bridge Design Specifications (10th Edition)
What are the changes affecting HDG in the AASHTO LRFD Bridge Design Specification (10th edition)?
The American Association of State Highway and Transportation Officials (AASHTO) via the Committee on Bridges & Structures (CoBS) recently released the 10th edition of its LRFD Bridge Design Specifications for use in the design, evaluation, and rehabilitation of bridges nationwide. The AASHTO Steel & Metals Committee (formerly T14 Committee on Steel Structures) approved ballot items revising Section 6 on Steel Structures directly pertaining to hot-dip galvanized (HDG) bridge projects.
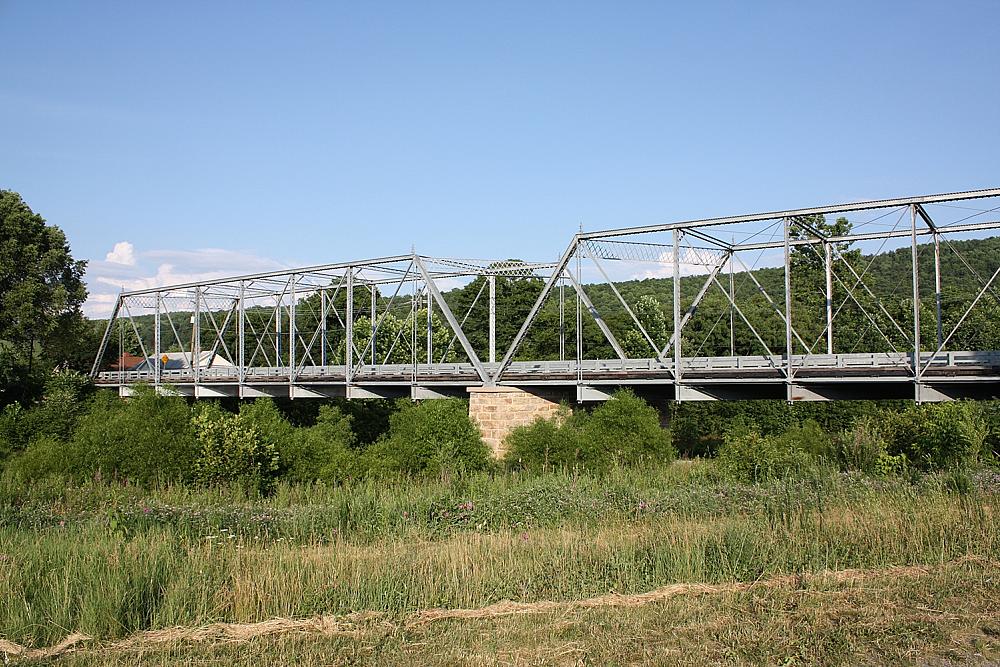
Creep Reduction Factor for HDG
In Article 6.13.2.8, A creep reduction factor Kc = 0.80 was introduced into the equation for determining the nominal slip resistance (Rn) of a galvanized faying surface (Class C, µ = 0.30) or duplex-coated faying surfaces utilizing a coating applied over hot-dip galvanizing to produce a higher slip coefficient (Class D, µ = 0.45). For all other surface conditions, Kc = 1.
Commentary language in RCSC Specification for Structural Joints Using High-Strength Bolts states coating thicknesses over 15 mils [380 μm] on each mating surface may creep under sustained bolt tension, reducing clamping force and slip resistance. RCSC and AGA continue to actively research this topic, but AASHTO moved to adopt this conservative 20% reduction to avoid the potential for concern over HDG coating thickness. Specifications for general HDG do not require a maximum coating thickness (only a minimum average coating thickness), but coating thicknesses in the range of 3-8 mils [75-200 μm] are considered typical. The revision results in a slight increase in the number of bolts used in HDG slip-critical connections.
Slip-Critical Connections & Mixed Faying Surfaces
For bridge projects containing a mixture of larger steel fabrications (plate girders too large for HDG) with smaller or more complex components suitable for HDG (cross frames, cable stay tubes, railings, and more), a tandem coating of HDG and metallizing has been successfully demonstrated for maximum cost efficiencies while leveraging the benefits of both coating systems. Examples include the I-95 overpass at Fairfield Avenue bridge over I-95 (CT), the Kosciuszko Bridge (NY), and the I-90 overpass at Commonwealth Ave. (MA).
Previously, slip-critical connections involving a galvanized faying surface and a metallized faying surface were not readily described by the AASHTO standards. However, they could be qualified to one of the surface condition classifications in accordance with Appendix A of RCSC’s Specification for Structural Joints Using High-Strength Bolts and used if approved by the Engineer. Testing can take several months and is subject to limited laboratory availability.
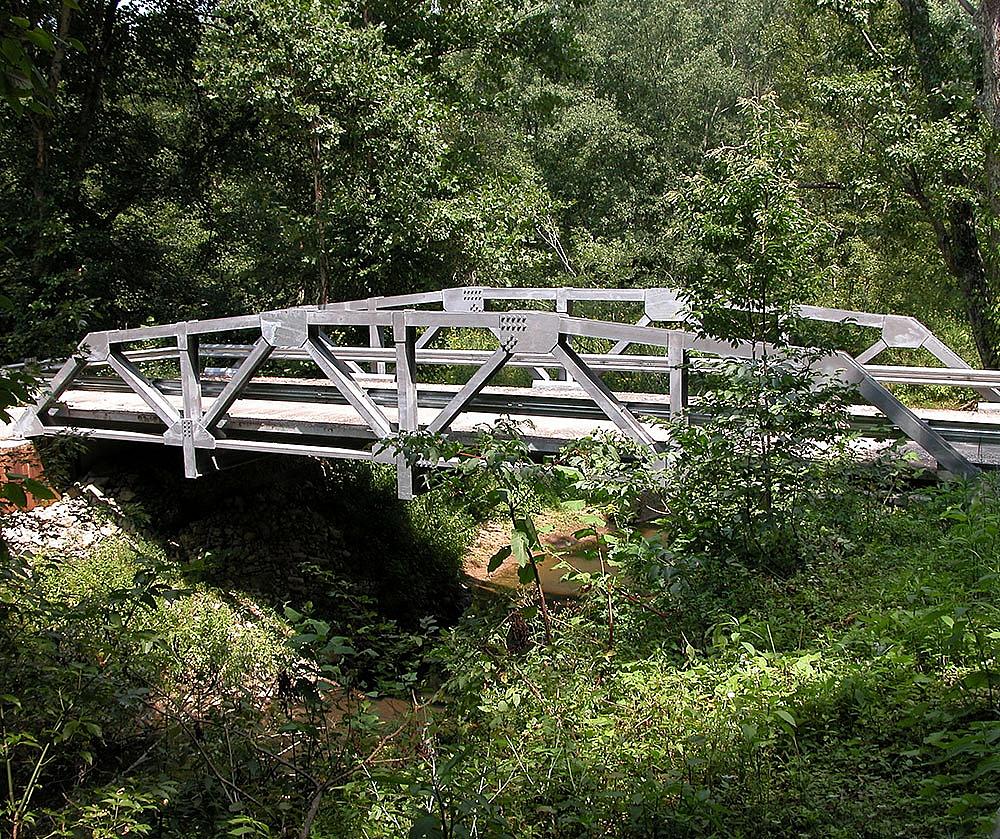
New in the 10th edition (Article 6.13.2.8), connections involving a hot-dip galvanized surface mated to a metallized faying surface are classified as a Class D surface condition for slip (µ = 0.45). Some limitations on metallizing composition and coating thickness are applicable in the new definition of Class D.
Class D Surface: blast-cleaned surfaces with Class D coatings, or a mixed faying surface utilizing an unsealed pure zinc or 85/15 zinc/aluminum thermal-sprayed coating with a thickness less than or equal to 16 mils mating with a hot-dip galvanized surface.
Although a Class D (µ = 0.45) surface condition has a slightly lower slip coefficient value than Class B (µ = 0.50), the difference between Class D and B does not cause a significant impact in the overall number of bolts required. This revision addresses a greater variety of options for the specifier/designer to optimize on cost and corrosion protection.
Note: AGA and the International Zinc Association are currently developing a new Specifiers Guide to assist projects pairing hot-dip galvanizing alongside zinc thermal spray.
© 2025 American Galvanizers Association. The material provided herein has been developed to provide accurate and authoritative information about after-fabrication hot-dip galvanized steel. This material provides general information only and is not intended as a substitute for competent professional examination and verification as to suitability and applicability. The information provided herein is not intended as a representation or warranty on the part of the AGA. Anyone making use of this information assumes all liability arising from such use.