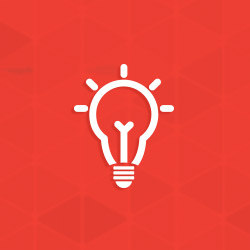
Performance and Inspection of HDG Exposed to Extreme Temperatures
Can HDG Withstand Heat Straightening, Arctic Temps, or Fires?
From time to time, the American Galvanizers Association (AGA) is asked how galvanized steel performs in a variety of applications, including exposure to extremely hot and cold temperatures. The galvanized coating is incredibly durable for wide temperature ranges, but care should be taken in some applications. Below are a few examples to demonstrate when precautions may be necessary if exposing hot-dip galvanizing to extreme temperatures and how to handle coating inspection of such items.
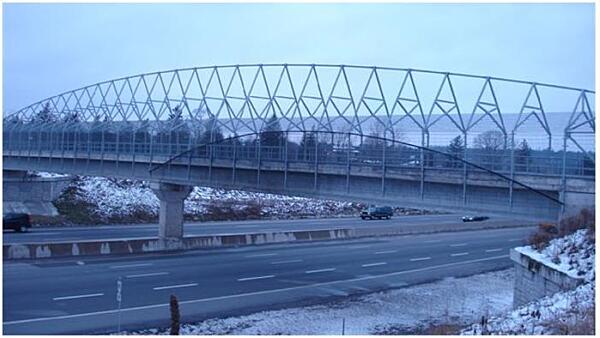
Low Temperatures
Studies of hot-dip galvanized steel in low-temperature environments (below -40 F) reveal minimal or no difference in atmospheric corrosion rate. Hot-dip galvanized steel is even utilized in some polar installations for corrosion protection and has been in service for many years. As with any steel at very low temperatures, the material may become brittle with extended use. Regardless, hot-dip galvanizing provides suitable protection against corrosion in low-temperature applications.
High Operating Temperatures
Depending on the operating temperature, there can be concerns with using hot-dip galvanized steel at elevated operating temperatures for long exposures. The reason is long-term, continuous exposure to temperatures above 392 F (200 C) can cause the outer free zinc layer to peel from the underlying intermetallic alloy layers, resulting in changes to mechanical properties, and may cause reduction in corrosion protection. However, the remaining intermetallic alloy layers provide good corrosion resistance and continue to protect the steel for many years, depending upon the remaining thickness. At temperatures ranging from 390 F (200 C) to 480 F (250 C), the remaining zinc-iron alloy layers will continue to protect the steel from corrosion. However, high operating temperatures above 480 F (250 C) will accelerate peeling and continued exposure above this temperature can result in the zinc-iron alloy layers cracking and separating from the steel. As a result, the recommended maximum temperature for hot-dip galvanized steel in long-term, continuous exposure is 392 F (200 C) to ensure maximum corrosion protection, while temperature applications above 480 F (250 C) are not recommended.
Temporary High-Temperature Exposures
In short-term use (a one-time temperature exposure for less than 24-48 hours or multiple periods of exposure less than two hours at a time), the recommended maximum service temperature for galvanized steel is approximately 660-700 F (350-370 C) to ensure coating integrity.
This also applies for articles that require heat straightening after galvanizing to remedy a part that has experienced distortion, or for articles to be bent hot after galvanizing. For example, parts that have been hot-dip galvanized and are distorted can be straightened at a temperature around 650 F without fear of coating damage.
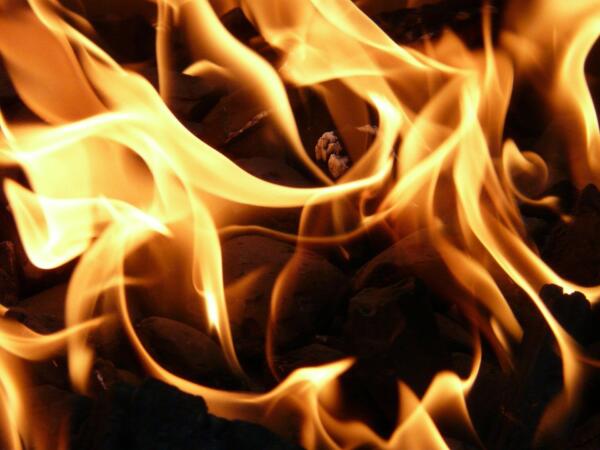
Fires
Temperatures in fires can easily exceed 1,000 F, but fires do not often last for durations which would compromise the integrity of a hot-dip galvanized structure. Even though the melting temperature of the outer eta layer (100% zinc layer) is 787 F (419 C), the melting point of the intermetallic alloy layers ranges from 986-1436 F (530-780 C). Therefore, there is a potential for coating damage but experience has found fire damage to be minimal on galvanized steel parts exposed to fires. Upon exposure to fire it is common to experience some staining (orange and/or rust color) and a layer of black carbon dust while the base galvanizing is intact.
In a study, conducted by the Galvanizers Association of Australia (GAA), the performance of hot dip galvanized utility poles exposed to brushfires was assessed using small-scale burn testing to simulate bushfire flame characteristics. Even though surface temperatures of 968 F (520 C) were reached, the overall coating remained intact but did experience some staining.
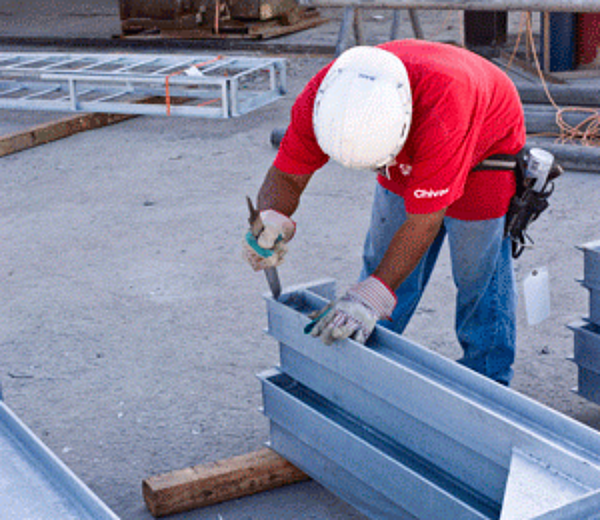
Inspection of Hot-Dip Galvanized Steel Exposed to High Temperatures
Coatings exposed to high temperatures may experience peeling or staining, but can be cleaned or otherwise prepared for coating thickness inspection. The time to first maintenance of a galvanized coating is directly related to average coating thickness, and can be re-evaluated based on the remaining coating thickness determined after high-temperature exposure. Therefore, if the inspection reveals a continuous hot-dip galvanized coating with enough average coating thickness to achieve the anticipated design life, the parts can be immediately placed back into service. For projects where peeling and/or staining are also an aesthetic concern, these areas can be remedied by smoothing and/or application of a zinc-rich paint.
If the coating inspection reveals damage, bare spots, or low average coating thickness with respect to the project requirements, the hot-dip galvanized coating can either be repaired in the field in accordance with ASTM A780, regalvanized, or (in the case of low-coating thickness) accepted/returned to service with a reduced time-to-first maintenance.
© 2025 American Galvanizers Association. The material provided herein has been developed to provide accurate and authoritative information about after-fabrication hot-dip galvanized steel. This material provides general information only and is not intended as a substitute for competent professional examination and verification as to suitability and applicability. The information provided herein is not intended as a representation or warranty on the part of the AGA. Anyone making use of this information assumes all liability arising from such use.