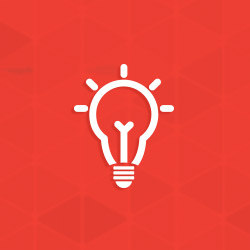
Hot-Dip Galvanizing in the Wind Power Industry
Can the wind power industry benefit from HDG?
Over the last few decades, wind energy has become a vital player in the US power industry. Keeping in spirit with efforts to move towards renewable energy and a more resilient grid, wind power production has steadily increased to over 10% of US energy and is still growing. Although there are many privately owned wind towers, the majority of wind power comes from wind farms, or wind power stations, which are commonly located both offshore and inland. The many environments in which wind towers are placed subject them to a variety of corrosive factors.
While size can be a limitation to the application of hot-dip galvanizing for blades and towers on some projects, there are many other steel components that can be successfully coated. If size permits, tower and blade components can and have been successfully galvanized in the past. However, full-size utility wind tower and blade components are often too large to galvanize. Even if parts too large for the kettle require a different coating system such as metallizing, there are still accessory components that make excellent candidates for galvanizing and they can be reused indefinitely.
Wind tower components that should be considered for galvanizing are, but not limited to, the following:
- Access platforms
- Anchor plates
- Blades (size permitting)
- Bolt platforms
- Brackets
- Fasteners
- Foundations
- Frames
- Gratings
- Hubs
- Ladders/stairs
- Nacelle components
- Offshore wind substation projects
- Railing
- Rotor components
- Support structures
- Towers (size permitting)
- Tower climbing systems
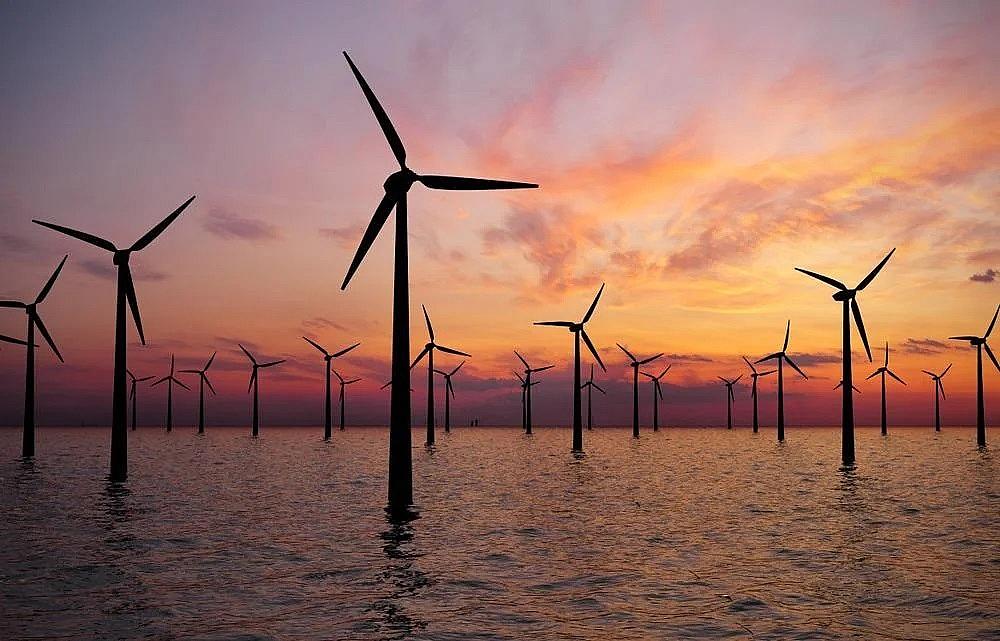
Though alternative coating systems must be used for items too large for the kettle, it is not required to use the same corrosion protection system throughout for uniformity. For example, some specifiers are turning to metallizing as their first choice for wind towers and blades which are too large for the galvanizing kettle. However, there are a few reasons why hot-dip galvanizing should be considered for the ancillary components of a wind turbine structure as opposed to an all-metallized solution. First, hot-dip galvanizing is on average 3-3.5 times less expensive than the cost of metallizing for these smaller components according to cost data published by AMPP. Second, hot-dip galvanizing is an immersion process making it better suited for coating parts with threads, nooks and crannies, or complex geometries which are notoriously difficult to metallize. Finally, hot-dip galvanized components have no potential for galvanic, or dissimilar metals corrosion when connected to metallized surfaces. Therefore, to combine and leverage the benefits of two zinc coating systems: metallize steel components too large for the galvanizing kettle and hot-dip galvanize the rest.
Areas with limited access not only have the potential to make initial coating application difficult but also corrosion monitoring and proper maintenance when required. HDG is relatively maintenance free and provides complete coverage for parts difficult to access once installed. This offers unmatched peace of mind when it comes to maintaining hard-to-reach areas like recesses and internal surfaces.
Hot-dip galvanizing demonstrates proven durability for wind power projects where maintenance and repair are inconvenient and costly. Galvanized access platforms and ladders for the first offshore wind towers in Europe (Tunø Knob Offshore Wind Farm), were in excellent condition after 25 years when the structures were decommissioned for a capacity upgrade. Meanwhile, Pinalosa Energy Corp has supplied tower access kits for 15 years with hot-dip galvanizing and Keuka Energy site in Ainsworth, Iowa started hot-dip galvanizing wind tower structures in 2013. Looking forward, the very first utility-scale offshore wind farm substation in US waters (South Fork Offshore Wind Substation) specified hot-dip galvanizing for handrail, stairs, ladders, grating, antenna mounts, and walkways based on its demonstrated longevity in similar environments for other offshore structures such as oil & gas platforms.
As utility companies and specifiers design these projects focused on clean energy production, building wind turbine components with sustainable materials goes hand in hand. Hot-dip galvanized steel is produced from natural, abundant resources (iron and zinc) and is 100% recyclable without the loss of any physical or chemical properties. Additionally, galvanized steel provides unparalleled maintenance-free durability for decades - reducing the need for more raw material or energy consumption throughout the life of the structure.
© 2025 American Galvanizers Association. The material provided herein has been developed to provide accurate and authoritative information about after-fabrication hot-dip galvanized steel. This material provides general information only and is not intended as a substitute for competent professional examination and verification as to suitability and applicability. The information provided herein is not intended as a representation or warranty on the part of the AGA. Anyone making use of this information assumes all liability arising from such use.