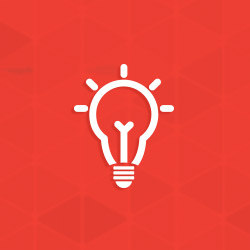
Hot-Dip Galvanizing in the Hydropower Industry
How can HDG benefit the Hydroelectric power industry?
Hydroelectric power has been a source of renewable energy for more than a hundred years, providing clean, sustainable electricity by harnessing the power of moving water. This method of power generation has seen significant growth in the United States over the past 5 to 10 years, while to the north, Canada currently generates 58% of its energy from hydropower. Hydropower plants not only help reduce reliance on fossil fuels but also require durable, long-lasting infrastructure to maintain consistent, renewable energy production.
One of the most significant challenges for hydropower infrastructure is exposure to water and high humidity levels. Corrosion of steel components in these environments can lead to inefficiencies, costly repairs, and safety concerns. The pipes and penstocks that channel water through a hydropower facility are at the heart of the operation. Given their exposure and the difficulty of repairing or replacing these components once installed, it is vital to protect them from corrosion.
Hot-dip galvanized steel has become a preferred corrosion solution in many hydropower plants across North America. HDG coatings are composed of zinc-iron alloy layers that are harder than the substrate steel, making it an ideal choice for harsh environments, including marine or water-dominated areas such as hydropower plants.
Many essential components within hydropower facilities benefit from HDG protection, as they are often exposed to constant moisture or submerged in water. Common galvanized components include:
- Aerators
- Aspiration & Evacuation Tube Covers
- Bearings
- Catwalks
- Debris Gates
- Elevator Shaft Components
- Fencing
- Fish Ladders
- Flow Restrictions
- Flood Control Gates
- Frameworks
- Penstocks
- Pipe Supports
- Platforms
- Railings
- Reinforcing Steel
- Runners
- Shafts
- Supporting Structures (including substations)
- Transmission Towers
- Turbine Components
- Valve
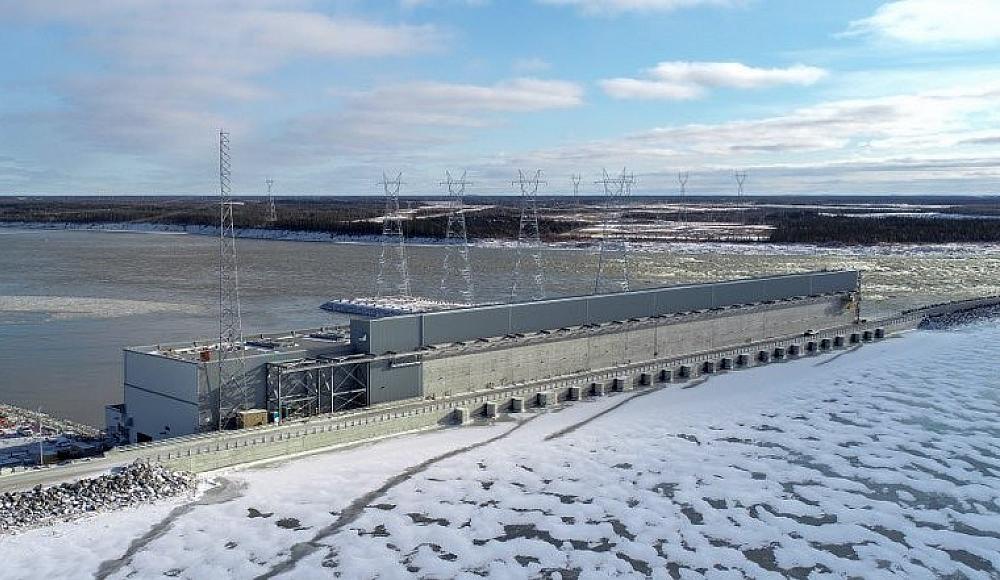
Galvanized steel components can resist corrosion for decades, minimizing the need for frequent maintenance and ensuring continuous operation. These benefits are not limited to the dam facility, but can also ensure long-lasting support of transmission systems to get the power where it needs to go. Robust and corrosion-resistant infrastructures make it easier for facilities to expand or upgrade without worrying about premature deterioration.
For instance, the Norris Dam substation in Tennessee is an impressive example of the long-term performance of galvanized steel. After nearly 90 years of service, this substation remains largely maintenance-free. Its durability provides an excellent example for future projects, demonstrating how HDG steel can significantly extend the service life of critical infrastructure.
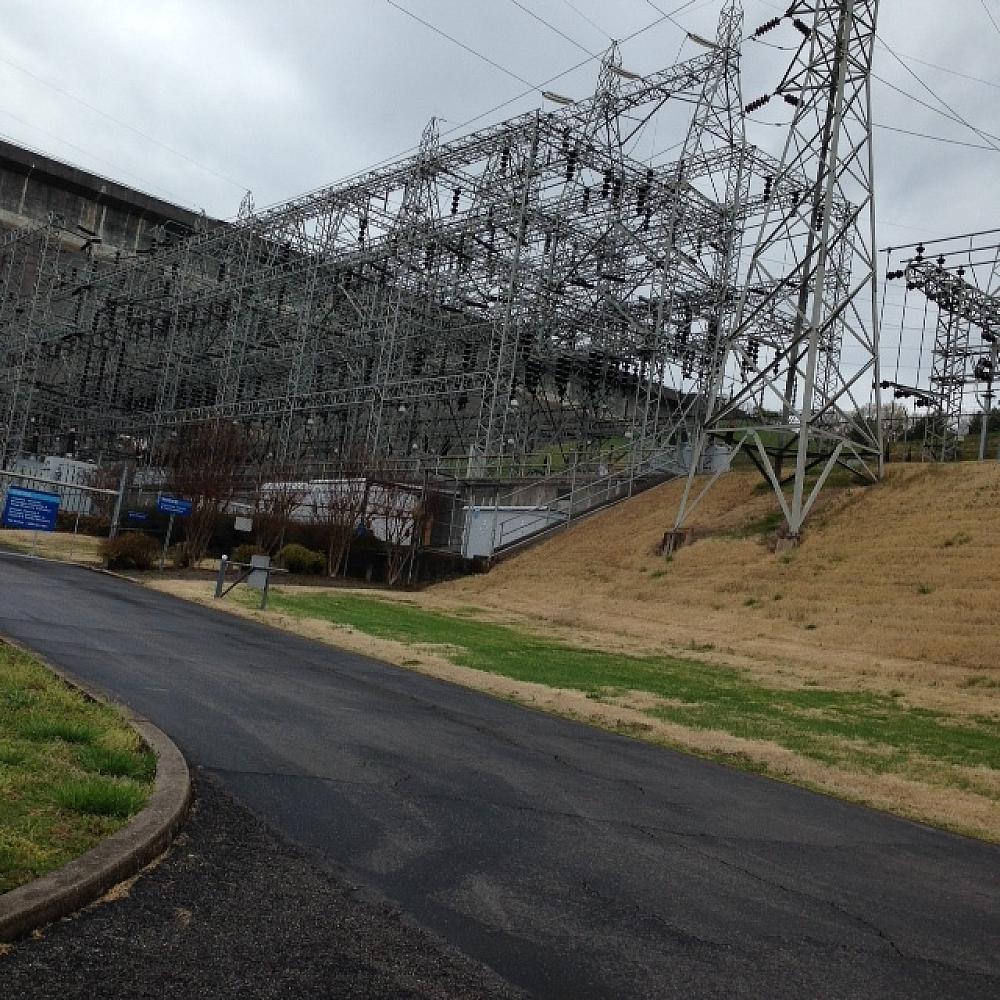
As utility companies design clean energy projects, choosing sustainable materials is crucial. Hot-dip galvanized steel aligns with these goals, as it is made from natural, abundant iron and zinc. Galvanized steel is 100% recyclable without loss of any physical or chemical properties, making it a great choice for sustainable infrastructure projects.
Hydropower plays a vital role in clean energy production, and protecting its infrastructure is essential. Hot-dip galvanizing offers a proven solution for safeguarding steel components, ensuring decades of maintenance-free service. With its unmatched durability and sustainability, hot-dip galvanized steel will be crucial in supporting the long-term growth and efficiency of renewable energy infrastructure and production.
© 2025 American Galvanizers Association. The material provided herein has been developed to provide accurate and authoritative information about after-fabrication hot-dip galvanized steel. This material provides general information only and is not intended as a substitute for competent professional examination and verification as to suitability and applicability. The information provided herein is not intended as a representation or warranty on the part of the AGA. Anyone making use of this information assumes all liability arising from such use.