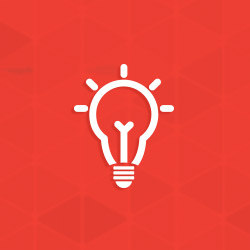
Hot-Dip Galvanizing for Bridge Decks in Chloride-Rich Environments
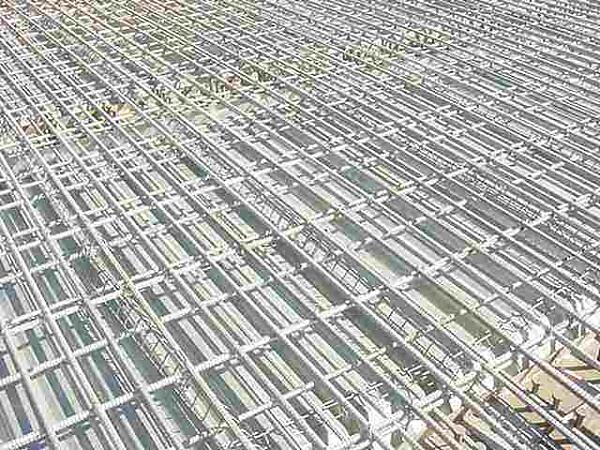
What is chloride threshold and its impact on galvanized rebar performance?
Reinforced concrete bridge decks are exposed to a wide variety of corrosive environments including the presence of salty air and seawater along the coast or the application of de-icing salts in winter months. All rebar is passivated immediately after the concrete pour and does immediately not corrode. However, concrete is porous and corrosive salts from these harsh environments work their way down to the rebar within. When a certain degree of saturation occurs, the rebar depassivates and initial corrosion of the rebar begins. As the steel rebar corrodes over time, a buildup of iron-corrosion products causes outward pressure toward the concrete, leading to eventual cracking, spalling, and failure.
To prevent spalling in high-chloride environments, specifiers of bridge decks turn to various means of rebar corrosion protection, such as hot-dip galvanizing. Hot-dip galvanized rebar provides unique benefits and long service life in high-chloride environments, making it a suitable choice for these applications. To evaluate the impact galvanized rebar has on the longevity of bridge decks, specifiers should consider the following:
- Time to reach the “chloride threshold” where zinc is depassivated in concrete
- Time to consume the galvanized coating
- Life of steel rebars after galvanizing is consumed
As a result, the maintenance-free service life of hot-dip galvanized bridges decks is:
Time to depassivation + HDG life + Black bar life
Time to Depassivation
Once the concentration of corrosive elements surpasses steel's corrosion threshold, the galvanized coating depassivates and begins to corrode. For marine environments and areas where de-icing salts are commonly used, there has been a lot of research over the years to quantify the chloride threshold associated with the onset of zinc corrosion, 1. Laboratory findings through accelerated testing indicate the threshold is somewhere between two and four times the threshold for the onset of corrosion of black reinforcing steel (0.95 kg/m3), 2. However, real-world testing where actual bridge decks were cored over decades observed the threshold to be five to ten times that of black bar, 3.
To be conservative, it is possible to use a chloride threshold for zinc which is four times the threshold for corrosion of black reinforcing steel. Therefore, the time to depassivate the galvanized coating in concrete is the time until the chloride concentration of the concrete surrounding the rebar reaches 3.8 kg/m3.
Time to Consume the Galvanized Coating
Once the chloride ion threshold is exceeded, the galvanized coating begins to corrode. However, it is important to note the zinc corrosion products migrate into the concrete matrix (Figure 1), meaning cracking and spalling do not occur during this stage.
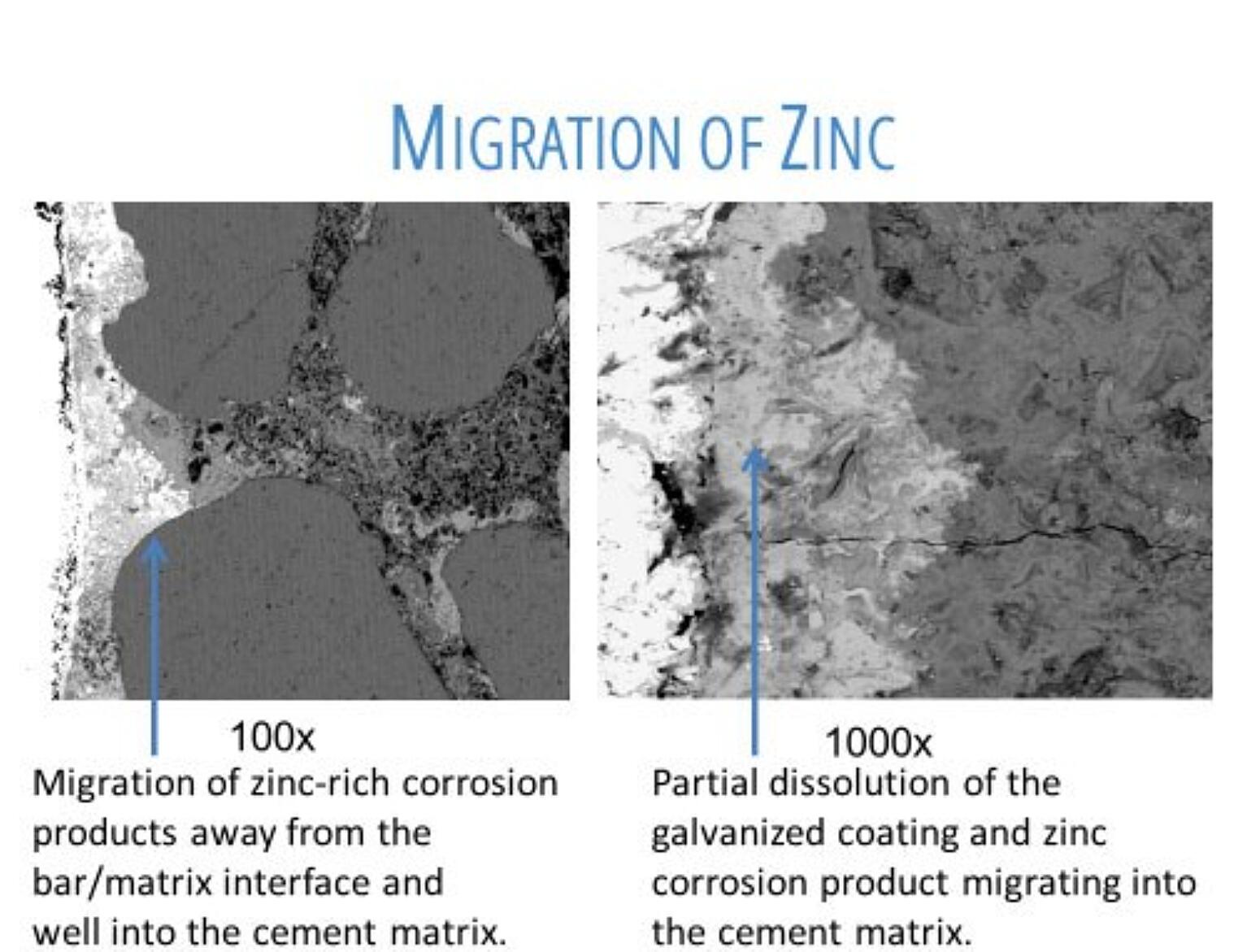
The corrosion rate of the zinc in concrete is approximately 3 µm/year (0.01 mils/year), but depends on the amount of moisture in the concrete, the wet/dry cycles, the cracks in the concrete, the concrete cover thickness, and use of concrete additives.
The time to initial carbon rebar corrosion after the threshold is reached is also a function of the amount of initial coating weight on the bar. Initial coating weight varies depending on the minimum requirements outlined in the specified standards for hot-dip galvanized rebar:
- ASTM A767 Class I (3.0 or 3.5 oz/ft2)*
- ASTM A767 Class II (2.0 oz/ft2)
- ASTM A1094 (1.2 oz/ft2)
*minimum required coating weight dependent on bar designation size
To estimate the performance of a ASTM A767 Class I coated bar (bar size ≥ No. 4), we can assume the minimum specified coating weight: 3.5 oz/ft2 (equivalent to 150 µm or 5.9 mils coating thickness). At a corrosion rate of 3 µm/year, the time to consume the galvanized coating is 50 years.
Life of Steel Rebars After HDG consumed
Once the galvanized coating is consumed, the steel is exposed and the final cycle of corrosion begins. The time from initiation of black rebar corrosion to initial cracking of the concrete may be approximately 3-5 years or 3-7 years depending on the concrete properties 4. For a conservative estimate, the time to full degradation or deck replacement may be 10-15 years.
Two Real-World Examples
To demonstrate the impact of hot-dip galvanizing for rebar placed in chloride-rich environments, let us review real-world data obtained from two bridge decks. The Tioga bridge (Tioga, PA) is located in a northern climate where road salts are the primary source of chloride ions. Meanwhile, the Boca Chica bridge (Key West, FL) is from a southern coastal climate where the ocean water and salty air result in high chloride ion exposure. These bridge decks were cored over a period of 27 years to determine the chloride concentration and condition of the galvanized rebar.
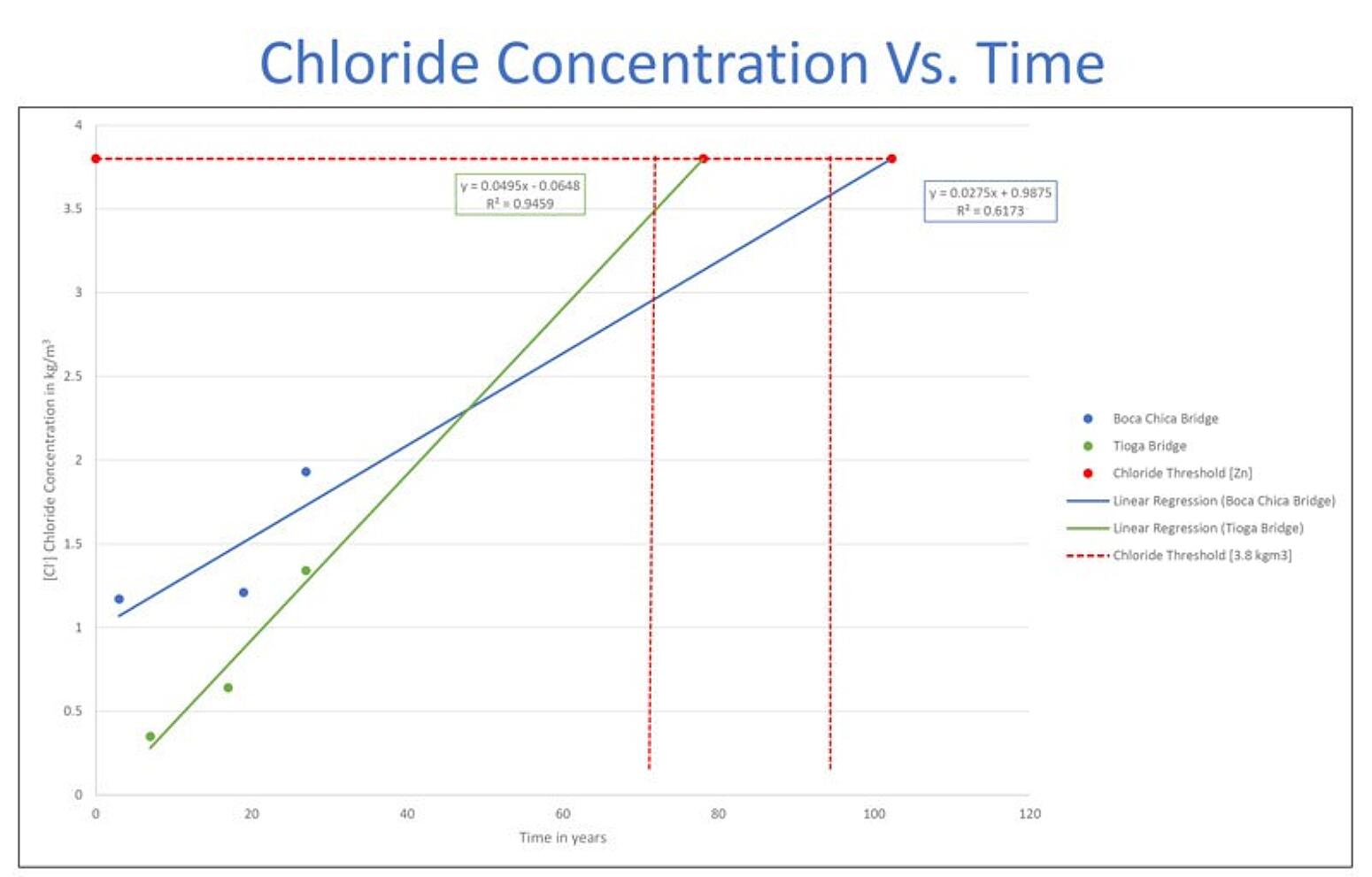
At 27 years, both bridge decks experienced chloride thresholds that were above the chloride threshold for black rebar, but well below the chloride threshold to begin corrosion of the galvanized rebar. From the chart in Figure 2, you can see the chloride concentration for both bridges rises over time, but neither the Tioga Bridge and Boca Chica bridges are predicted to experience the chloride threshold for zinc (3.8 kg/m3) until approximately 78 and 102 years, respectively. With this information, we can graph the anticipated performance of the galvanized rebar over the life of a bridge where no maintenance is performed (Figure 3).
Once corrosion of the galvanized coating begins, a coating weight of 3.5 oz/ft2 provides a galvanizing service life of 50 years. After consumption of the galvanized coating, the bare rebar begins to corrode at a more accelerated rate than the galvanizing until cracking and spalling initiate.
Maintenance-free Service Life = time to chloride threshold + HDG life + black bar life
Tioga Bridge (~143 years) = 78 + 50 + 15 years
Boca Chica Bridge (~167 years) = 102 + 50 + 15 years
Achieving 100-year Maintenance-Free Service Life
Future bridges constructed in coastal areas or in climates where road de-icing salts are commonly used throughout winter can achieve significant longevity as demonstrated by the Tioga and Boca Chica bridge. The higher chloride threshold is capable of preventing initial corrosion of the galvanizing by 78 or 102 years into the service life. Even after the chloride threshold for zinc is reached, the hot-dip galvanized coating protects the black bar for decades so that a 100-year service life can be achieved well before the initial corrosion of the underlying black bar.
Footnotes:
- Yeomans, S. R. “Corrosion of the Zinc Alloy Coating in Galvanized Reinforced Concrete”; Research Report No. R103, The University of New South Wales, The Department of Civil and Maritime Engineering, 1991
- Tonini, D. E. and Dean, S. W. “Chloride Corrosion of Steel in Concrete”; ASTM-STP 629, 1976
- Cornet, I. and Bresler, B. “Corrosion of Steel and Galvanized Steel in Concrete”’ Materials Protection, Vol. 5, No. 4, 1966, p. 69-72
- Brown, M. C. and Weyers, R. E. “Corrosion Protection Service Life of Epoxy-Coated Reinforcing Steel in Virginia Bridge Decks”; Virginia Transportation Research Council, Commonwealth of Virginia, 2003
© 2025 American Galvanizers Association. The material provided herein has been developed to provide accurate and authoritative information about after-fabrication hot-dip galvanized steel. This material provides general information only and is not intended as a substitute for competent professional examination and verification as to suitability and applicability. The information provided herein is not intended as a representation or warranty on the part of the AGA. Anyone making use of this information assumes all liability arising from such use.