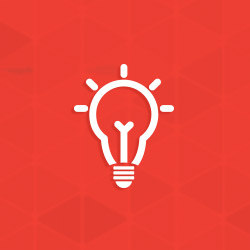
Galvanized Rebar in Marine Environments
My customer has heard rave reviews about galvanized rebars performance when embedded in concrete for marine applications . . . Why is HDG rebar outperforming black rebar in this particular application?
Its true that galvanized rebar outperforms black rebar in this application—the superior performance is a result of several factors stemming from zincs unique corrosion behavior. The extended performance of galvanized rebar can be correlated to a higher threshold for corrosion initiation, reduced corrosion kinetics, and a lowering of stresses induced in the concrete as a result of the mobility of zinc corrosion products.
Chemical corrosion of steel results when a voltaic cell is formed contacting the steel surface. The cell contains four basic parts: anode, cathode, electrolyte, and return current path. For this discussion, lets focus on the electrolyte. In marine applications, the electrolyte is seawater—most importantly, the chloride content of that seawater. With respect to embedded rebar in marine environments, a degree of saturation of electrolyte must be reached in order for corrosion to begin. This is referred to as the critical chloride threshold. Critical chloride thresholds are different for all metals, but the value most commonly used for black steel is 1.1 lbs/yd3. Field evaluations for bridges in marine applications performed by CTL—a contractor for the International Lead Zinc Research Organization (ILZRO)—report HDG rebar performing corrosion-free for decades in chloride environments far exceeding the black steel threshold value (see chart, facing page).
1995 Data Compiled from ILZRO Field Evaluation of HDG Rebar | ||||||||
---|---|---|---|---|---|---|---|---|
Bridge/Structure Name | Location | Construction Year | 1975 ZE 206 | 1977 ZE 247 | 1982 ZE 320 | 1992 ZE 389 | 1994 ZC 1 | Years to Date Above CI- Corrosion Threshold |
PCA Slabs | IL | 1963-1969 | [6] | |||||
Boca Chica | FL | 1972 | [3] | [19] | [21] | |||
Seven Mile | FL | 1972 | [3] | [19] | ||||
Longbird | Bermuda | 1952 | [23] | [42] | [42] | |||
Flatts | Bermuda | 1966 | 8 | [28] | [28] | |||
Arnes | IA | 1967 | 7 | 14 | [26] | |||
Montpelier | VT | 1971 | 3 | [10] | [21] | |||
Manicouagan | Quebec | 1966 | 8 | |||||
Penno's Wharf | Bermuda | 1964/1966/1969 | [28*] | [28*] | ||||
Hamilton Dock | Bermuda | 1966 | [28] | [28] | ||||
RBYC Pier | Bermuda | 1968 | [26] | [26] | ||||
Athers | PA | 1973 | [8] | [18] | [20] | |||
Betsy Ross | PA | 1973 | 8 | |||||
Corapolis | PA | 1972 | 9 | [19] | [21] | |||
Hershey | PA | 1975 | [6] | [16] | ||||
Orangeville | PA | 1974 | 7 | |||||
Tioga | PA | 1974 | 7 | 19 |
From this research, its reasonably deduced that the critical chloride threshold for galvanized steel is far higher than that of black steel, but that is only part of the reason for HDG rebars noteworthy success. In high pH environments (namely saturated calcium hydroxide solutions . . . for this discussion, wet concrete mix), zinc surfaces passivate to form a calcium hydroxyl-zincate layer. A study by Andrade and Macias showed that this passive zincate layer can reduce corrosion currents, a scientific way of measuring corrosion potential, by an order of magnitude. This result was obtained in a chloride-free suspension and the effect of chlorides on the formation of this passive layer is not fully understood. Andrade and Macias showed that chloride concentrations of 0.30.9 molars do not have an effect on the formation of the passive zincate layer, but Sergi, Short, and Page suggest that higher concentrations do; however, they do not report a threshold value. Regardless, galvanized coatings after passivation show much lower corrosion currents in bench-scale tests, equivocal to zinc losses of 1.5 ?m/yr, and a service life of 100 years for an ASTM A767 Class I coating.
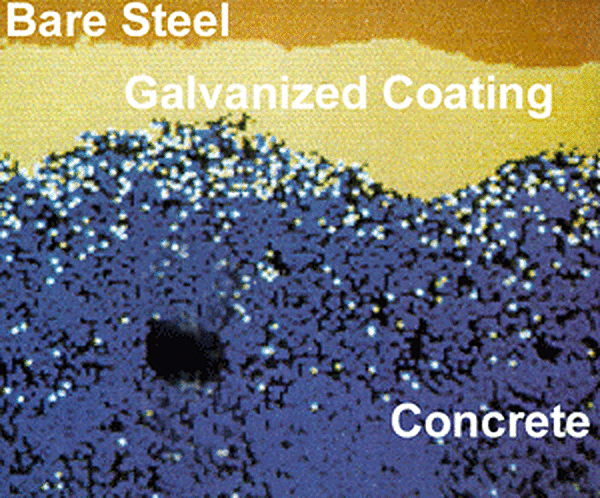
The final and, perhaps, most remarkable phenomena contributing to the superior performance of galvanized rebar deals with the actual corrosion products of the zinc coating itself. Cracking—or, in its most severe form, spalling—occurs as a result of a local increase in internal pressure due to volume increase when metal transforms into corrosion products. As steel corrodes, the voluminous products formed as part of the corrosion reaction need some place to go and pressure builds until a crack in the concrete matrix results. Continued corrosion results in the production of more corrosion products, further cracking the concrete and spalling until the article is no longer fit for service. The corrosion of zinc coated rebar occurs in a slightly different fashion. Zinc corrosion products are very small and migrate away from the surface of the rebar and into the bulk media of the concrete matrix. This can be seen in the figure, right,
This phenomenon results in a small increase in internal pressure at a much slower rate. Ultimately, this translates into a longer service life for galvanized rebar.
© 2025 American Galvanizers Association. The material provided herein has been developed to provide accurate and authoritative information about after-fabrication hot-dip galvanized steel. This material provides general information only and is not intended as a substitute for competent professional examination and verification as to suitability and applicability. The information provided herein is not intended as a representation or warranty on the part of the AGA. Anyone making use of this information assumes all liability arising from such use.