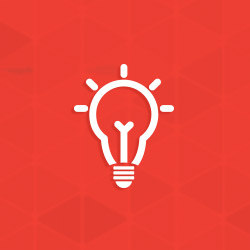
Evaluation of HDG Repair Materials
Is any HDG repair material better than the other?
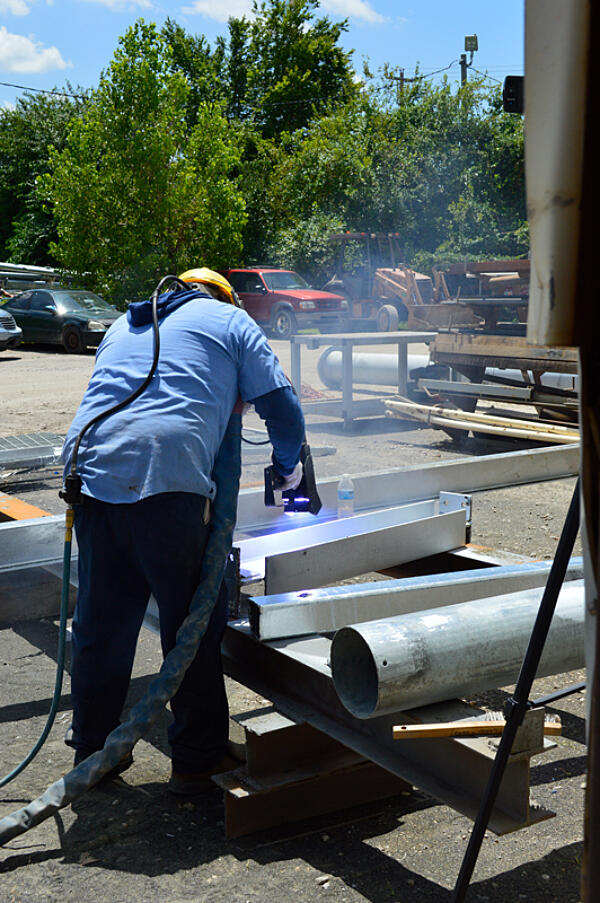
The touch-up and repair of hot-dip galvanized coatings is important to maintain uniform barrier and cathodic protection as well as ensure longevity. Although the hot-dip galvanized coating is very resistant to damage, small voids or defects in the coating can occur during the galvanizing process or due to improper handling of the steel after hot-dip galvanizing. ASTM A780, Practice for Repair of Damaged and Uncoated Areas of Hot-Dip Galvanized Coatings, details how to repair a damaged hot-dip galvanized coating regardless if performed at the galvanizing plant or in the field. Whether newly galvanized or in service for years, the practice for touch-up and repair of hot-dip galvanized steel is the same. There is a maximum allowable repair size for new products at the galvanizing plant, but no maximum repair size for products that have been delivered to the job site or have been in service.
ASTM A780 contains three acceptable methods of touch-up and repair of hot-dip galvanized steel: zinc-based solder, zinc-rich paint, or zinc-spray (metallizing). Since three options are provided, customers concerned with overall coating performance may occasionally ask which coating repair method is most suitable to provide durable corrosion protection for their project. Whether performed at the galvanizing plant or in the field, it is possible to achieve a successful and durable coating repair (regardless of repair method) as long as:
- prior to acceptance from the galvanizer, only bare areas within the maximum repair size criteria are touched-up (refer to either ASTM A123 Paragraphs 6.2.1 and 6.2.2, A153 Paragraph 4.5 or A767 Paragraph 9.1)
- the repair material meets the material requirements provided within the hot-dip galvanized coating repair specification ASTM A780 Paragraph 4 and is also applied according to the manufacturers' recommendations and/or ASTM A780 Annex A1, A2 or A3.
- the repair thickness meets the values provided within the primary galvanizing specification (A123 Paragraph 6.2.3 or A153 Paragraph 4.5)
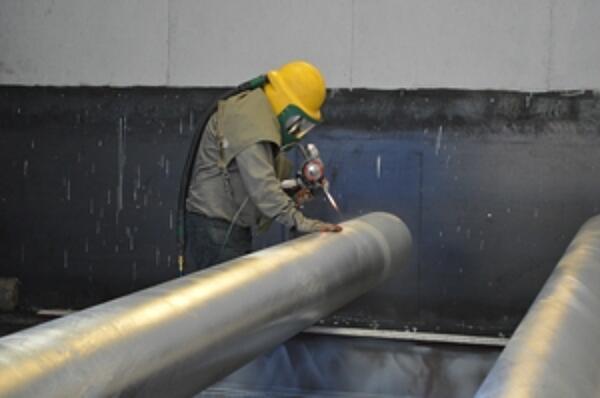
That being said, it is important to note each repair material may perform slightly different in terms of corrosion resistance, aesthetics, or abrasion resistance. After determining which of these criteria are most important for the individual project, a preferred method may be chosen depending on evaluation of the advantages and/or disadvantages for each repair material.
To assist in this evaluation, a study was conducted to evaluate thirteen repair materials and twenty application methods for the repair of hot-dip galvanized coatings. Each repair material was evaluated in terms of ease of application, aesthetics, adhesion, abrasion resistance, and corrosion resistance. The following table summarizes results from the study in addition to practical experience from the hot-dip galvanizing industry:
Repair Material | Advantages | Disadvantages |
Zinc-Based Solder | - Affordable - Easy to apply - Good barrier protection - Good cathodic protection - Very good adhesion - Best color match to HDG | - Difficult to apply on curved, vertical, and overhead surfaces - Difficult to apply over large surface areas - Thin coatings tend to be produced - Low abrasion resistance - Requires heat source |
Zinc-Rich Paint (organic & inorganic formulations) | - Easiest to apply - Lowest cost - No limit to coverage area - Brush-on application facilitates achieving minimum thickness - Various shades available to assist in appearance matching - Very good barrier protection - Very good adhesion | - Lower cathodic protection than other two methods - Low abrasion resistance - Potential for poor appearance match - Spray application results in thin coatings requiring multiple applications - Depending on weather/location, inorganic zinc rich formulations may require control of relative humidity and temperature during application |
Zinc-Spray (Metallizing) | - No limit in coverage area - Very good barrier protection - Excellent cathodic protection - Very good adhesion - Good abrasion resistance - Good appearance match | - Most expensive - Extensive equipment and qualified personnel required for blasting and application - Difficult to apply on internal surfaces or hidden corners, recesses, holes - Quality of repair highly depends on experience and qualification of applicator |
If the repair method or specific product material selected is different from the standard practice of the galvanizer, this is a topic that should be discussed and agreed to prior to galvanizing.
For more information on applying HDG repair materials in accordance with ASTM A780 to achieve durable HDG coating repairs, refer to the AGA Touch Up & Repair video series. These videos provide highly beneficial visual aids to those needing assistance with touch-up and repair, whether in the plant or the field.
References:
© 2025 American Galvanizers Association. The material provided herein has been developed to provide accurate and authoritative information about after-fabrication hot-dip galvanized steel. This material provides general information only and is not intended as a substitute for competent professional examination and verification as to suitability and applicability. The information provided herein is not intended as a representation or warranty on the part of the AGA. Anyone making use of this information assumes all liability arising from such use.