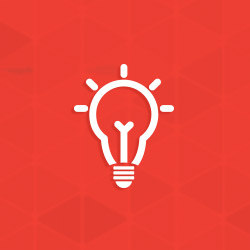
Differences Between ASTM A123 and CSA G164-18
What are the differences between ASTM A123 and CSA G164-18?
As the industry standard, ASTM A123 Standard Specification for Zinc (Hot-Dip Galvanized) Coatings on Iron and Steel Products, provides requirements for hot-dip galvanized coatings on various steel products. Most galvanizers located in North America use this specification as their standard for coating thickness, appearance, finish, and adherence. However, there are some competing specifications that get attention when an end user asks a galvanizer to use them. For example, some customers in Canada may ask for steel to be galvanized according to CSA G164 Hot Dip Galvanizing of Irregularly Shaped Articles. While this standard is similar to ASTM A123 in scope and purpose, there are many differences between the two. It is important to be aware of these differences in the event a fabricator or specifier asks about CSA G164.
Previously, CSA G164 has not been updated since 1992, and seemed to have lost relevancy in the market and was seldom used. In 2018, G164 was updated to: include references to communication and power line hardware specifications, remove coating weight values in favor of coating thickness values, revise material classifications and associated minimum coating thickness, and mention alternative galvanizing options (thermal diffusion galvanizing and mechanical galvanizing). A review of the specification updates and a summary of the differences between ASTM A123 and CSA G164 are provided below.
Scope & Reference Specifications
The scope of these two specifications continue to be nearly identical in terms of the types of products to be batch hot-dip galvanized, but some new language added to CSA G164 changes the primary industry or market:
“This Standard specifies the requirements for zinc coating (galvanizing) by the hot-dipping process on iron and stele products intended or primarily for use in electrical and communication systems made from rolled, pressed, cast iron, or forged shapes such as structural sections, plates, bars, pipes, or sheets 1mm thick and thicker.”
To supplement this changed focus on the electrical and communications industry, the new revision of G164 also includes a new reference specification CSA C83, Communication and Power Line Hardware. Newly updated in 2017 (previous revision 1996), this reference standard offers utility companies a comprehensive list of electrical system line hardware components (including hot-dip galvanized), with critical performance, dimensional, design, and inspection criteria.
Bath Composition and Zinc Purity
Though previously different, CSA G164 was updated to match the zinc bath composition requirement of ASTM A123. G164 requires, “…the galvanizing bath shall contain not less than 98.0% zinc by mass” while A123 states in section 5.5, “….the galvanizing bath shall contain not less than an average value of 98.0% zinc by weight.” Percentage by weight and percentage by mass differ only in verbiage and are describing the same quantity. Both standards cite ASTM B6 as a standard for zinc to be used in the galvanizing bath, but ASTM A123 also accepts specification B960 for recycled zinc.
Material Categories and Coating Thickness
Each specification uses a table to describe minimum coating thickness standards on galvanized steel, but the minimum requirements and materials listed are quite different. Table 1 of ASTM A123 has requirements for structural shapes, strip and bar, plate, pipe and tubing, wire, and reinforcing bar. CSA G164’s classifications are more general and include castings; rolled, drawn, pressed, or forged steel; and screws, bolts, nuts, rivets, nails, and similar fasteners. We can see G164’s first two general categories are broken down into the six specific categories found in A123. Also, A123 does not give requirements for the minimum coating thickness on fasteners and threaded articles but references ASTM A153 for these requirements. Both tables are shown below to compare the minimum coating thicknesses specified by each one.
The most notable difference here is in regard to the minimum coating thickness required by A123 for pipe and tubing as well as for strip and bar. Recent information has shown coatings much thicker than these minimum requirements are not attainable on these materials. Despite this, G164 lumps this material in with all other materials and requires unattainable thicknesses for strip, bar, pipe, and tubing.
CSA G164 Minimum Average Coating Thickness (μm) by Material Classification
Classification of Material | Size/Thickness | Minimum Coating Thickness (μm) |
1 Castings iron and steel | all | 85 |
2 Rolled, drawn, pressed, or forged steel articles (except Classifications 3 and 4) | < 1.6 mm 1.6 mm to < 3.2 mm 3.2 mm to < 4.8 mm > 4.8 mm Structural Steel >6.35 mm and plates, non centrifuged | 45 65 75 85 100 |
3 Screws, bolts, nuts, rivets, nails, and similar fasteners | < 12.7 mm diameter & Washers < 6.4 mm thick | 42 |
4 Bolts, nuts, and threaded fasteners | > 12.7 mm diameter & Washers >6.4 mm thick | 65 |
ASTM A123: Minimum Average Coating Thickness (μm) by Material Category
Material Category | All Specimens Tested- Steel Thickness Range (Measured), in. (mm) | |||||
---|---|---|---|---|---|---|
<1/16 [<1.6] | >1/16 to <1/8 [>1.6 to <3.2] | >1/8 to <3/16 [>3.2 to < .8] | >3/16 to <1/4 [>4.8 to <6.4] | >1/4 to <5/8 [>6.4 to <16.0] | >5/8 [>16.0] | |
Structural Shapes | 45 | 65 | 75 | 75 | 100 | 100 |
Strip and Bar | 45 | 65 | 75 | 75 | 75 | 100 |
Plate | 45 | 65 | 75 | 75 | 75 | 100 |
Pipe and Tubing | 45 | 45 | 75 | 75 | 75 | 75 |
Wire | 35 | 50 | 60 | 65 | 80 | 80 |
Reinforcing Bar | - | - | - | - | 100 | 100 |
Forgings and Castings | - | - | - | 100 | 100 | 100 |
Each standard lists the same tests to be used to determine the coating thickness on galvanized steel; magnetic or electronic gauge thickness, weigh galvanize weigh, weigh strip weigh, or microscopy methods. The practice behind each one of these methods varies from one specification to the next, but the most notable differences are that of the magnetic and electronic thickness gauge measurements.
G164 requires each coating thickness reading to be at least 90% of the of the required minimum thickness in the table with the average of five measurements equaling the required minimum thickness in the table. A123, on the other hand, only requires the average coating thickness measurement meet the minimum coating thickness required by A123 Table 1, with the average of one specimen being one coating grade below the requirement in Table 1 (as listed in Table 2).
Sampling
Previously, the sampling procedure laid out in G164 for testing the coating thickness had some very general and relaxed guidelines in comparison to the sampling procedure provided in A123 Paragraph 7. The G164 sampling procedure has been updated to reference the same sampling protocol outlined in Annex B of CSA C83, Communication and Power Line Hardware.
Finish & Appearance
Few requirements are given by G164 concerning the appearance of the zinc coating. The specification does require that the coating be free from “…imperfections such as blisters; gritty or uncoated areas; acid, black spots, or dross particles adhering to the coating…” ASTM has a more realistic expectation of the coating being free from “…uncoated areas, blisters, flux deposits, and gross dross inclusions.” The key difference here is the disallowance of any dross particles adhering to the coating according to G164. ASTM A123 also holds a few more requirements regarding the finish of the coating.
Adherence & Embrittlement
Both specifications ask for the use of a stout knife test to determine proper adherence of the coating. However, G164 gives its own test procedures for strain-age embrittlement (bend or impact test) while A123 references a complete guide of ASTM A143 which details a bend test.
Touch-up & Repair
Touch-up and repair of the hot-dip galvanized coating is performed in accordance with ASTM A780 for both standards. However, the two specifications contain a minor differences regarding the maximum area that can be repaired after hot-dip galvanizing. Both specifications require a bare spot must be less than one inch in its narrowest dimension and less than 0.5% of the coated area if it is to be repaired at the galvanizing plant. However, G164 3.3 refers to “surface area to be coated,” while A123 6.2.2 refers to “the accessible surface area to be coated on that article.” This may seem like a small difference in syntax, but this difference may prove to be very important when overlapping (and similar) areas are considered. ASTM A123 also declares, in addition to the 0.5% requirement, that “or 36 in2 per short ton [256 cm2per metric ton] of piece weight, whichever is less” be the smallest allowable area for renovation before the piece is rejectable.
G164 does allow exception to the maximum allowable repair size stating “any area larger than this may be renovated if mutually agreeable to the galvanizer and purchaser.” ASTM A123 does not allow an exception to maximum allowable repair size at the galvanizing plant. Another difference is related to repairs performed in the field, such as touch up after welding at the job site. ASTM A123 6.2.2 directly address the issue, stating "once the parts have left the galvanizing facility there shall be no limit on the size of the area subject to renovation." Though CSA G164 does not discuss field repairs explicitly, the same clause regarding mutually agreeable repair size could be employed.
Alternate Galvanizing Methods
CSA G164 includes a new informative Annex E on alternative galvanizing methods. The process and properties of thermal diffusion galvanizing (TDG) are described along with a reference to the associated standard ASTM A1059, Zinc Alloy Thermo-Diffusion Coatings (TDC) on Steel Fasteners, Hardware, and Other Products. Mechanical galvanizing under ASTM B695, Coatings of Zinc Mechanically Deposited on Iron and Steel, is also referenced as an alternative galvanizing method.
Summary of Differences
In order to completely understand the differences between CSA G164 and ASTM A123, one must fully read and understand each specification. However, the information presented here may adequately describe some of the major differences between the two.
Category | CSA G164 | ASTM A123 |
Galvanizing Bath | 98% by mass | 98% by weight |
Zinc Purity | ASTM B6 | ASTM B6 or B960 |
Max. Repairable Area | <25 mm [1 in] wide in smallest dimension and 0.5% of total area OR, mutually agreed size | <25 mm [1 in] wide in smallest dimension and 0.5% of accessible area or 36 in2 per short ton |
Field Repairs | Not explicitly addressed | No limit to repair size |
Minimum Coating Thickness | Very general material categories (includes fasteners) with some unattainable thicknesses | Specialized material categories with thicknesses based on real-world information |
Coating Thickness Measurements | Magnetic or electronic gauge, weigh galvanize weigh, weigh strip weigh, microscopy | Magnetic or electronic gauge, weigh galvanize weigh, weigh strip weigh, microscopy |
Coating Thickness Averages | Average of five thicknesses with all readings being at least 90% of required minimum | Total average equal to minimum coating thickness requirement in Table 1 with each specimen average more than one coating grade less. |
Sampling Procedure | CSA C83 Annex B | A123 Paragraph 7 |
Finish/Appearance | No imperfections permitted including dross inclusions | Gross dross inclusions are not permitted |
Adherence | Stout knife test | Stout knife test |
Embrittlement | Strain-age embrittlement tests provided in Paragraph 7.5 (bend and impact tests). No tests for hydrogen embrittlement. | ASTM A143 Bend Test |
Alternative Galvanizing Methods | Thermal Diffusion Galvanizing (ASTM A1095) Mechanical Galvanizing (ASTM B695) | N/A |
© 2025 American Galvanizers Association. The material provided herein has been developed to provide accurate and authoritative information about after-fabrication hot-dip galvanized steel. This material provides general information only and is not intended as a substitute for competent professional examination and verification as to suitability and applicability. The information provided herein is not intended as a representation or warranty on the part of the AGA. Anyone making use of this information assumes all liability arising from such use.