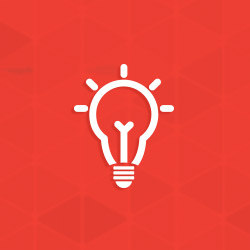
Overview of ASTM A123/A123M
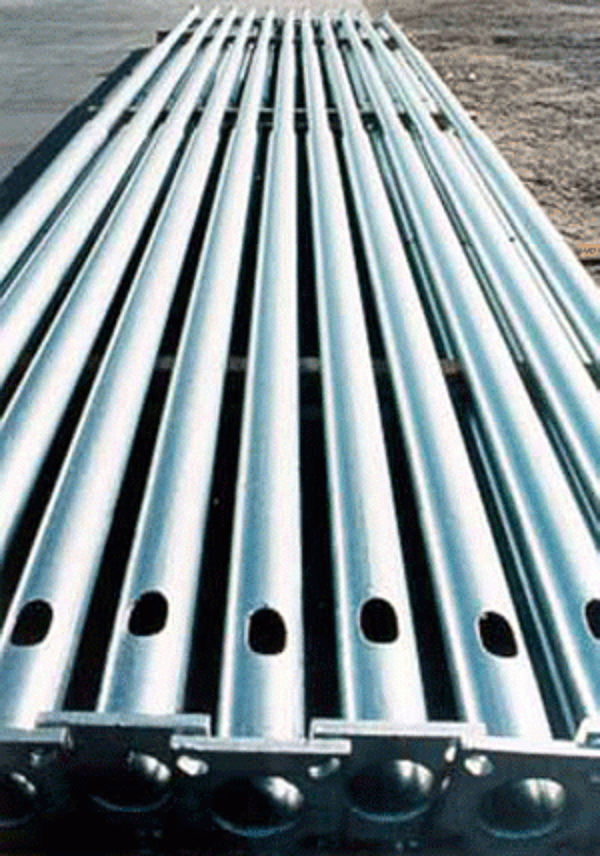
The specification ASTM A123/A123M Specification for Zinc (Hot-Dip Galvanized) Coatings on Iron and Steel Products, covers individual steel pieces as well as assemblies of various classes of material. The six material categories covered in ASTM A123/A123M include structural shapes, strip and bar, plate, pipe and tubing, wire, and reinforcing bar. A fabrication can have more than one material category such as a frame assembly. Any combination of these products can be assembled into a single fabrication and then hot-dip galvanized.
It is the responsibility of the designer and fabricator to ensure the product has been properly designed and built before hot-dip galvanizing. The galvanizer should be informed of any necessary special instructions or requests, preferably in writing on the purchase order, before the materials are shipped to the galvanizing plant.
It is the responsibility of the galvanizer to ensure compliance with the specifications, as long as the product has been designed and fabricated in accordance with the supporting specifications. However, if the galvanizer has to perform additional work in order to prepare the product for hot-dip galvanizing, such as drilling holes to facilitate drainage or venting, it should be approved by the customer. Once the material has been hot-dip galvanized, it can be fully inspected at the galvanizing plant prior to shipment.
Any materials rejected by an inspector for any reason except embrittlement may be stripped, re-galvanized, and resubmitted for inspection. The ASTM specifications A143/A143M, ASTM A384/A384M, and ASTM A385 provide guidelines for preparing products for hot-dip galvanizing. The requirements listed in ASTM A123/A123M include coating thickness, finish, appearance, and adherence. These are each defined below and discussed in more detail later in this course.
ASTM A123/A123M Requirements
- Coating Thickness / Weight dependent upon material category and steel thickness
- Finish continuous, smooth, uniform
- Appearance free from uncoated areas, blisters, flux deposits and gross dross inclusions as well as having no heavy zinc deposits that interfere with intended use
- Adherence the entire coating should have a strong adherence throughout the service life of galvanized steel
The hot-dip galvanized coating is intended for products fabricated into their final shape that will be exposed to corrosive environmental conditions. Once a product has been hot-dip galvanized, any further fabrication, which rarely occurs, may have negative effects on the corrosion protection of the coating. The coating grade is defined as the required thickness of the coating and is given in microns. All coating thickness requirements in specification ASTM A123/A123M, (Tables 1 and 2), are minimums; there are no maximum coating thickness requirements in the specification.
In atmospheric environments, the time to first maintenance of hot-dip galvanized steel is directly proportional to the thickness of the hot-dip galvanized coating. With all other variables held constant, the thicker the zinc coating, the longer the life of the coating. The aim of the finish and appearance requirements is to ensure no coatings have problem areas that are deficient of zinc or have surface defects that would interfere with the intended use of the product. In addition, the coating should have a strong adherence throughout the service of the hot-dip galvanized steel.
Table 1: Minimum Average Coating Thickness Grade by Material Category | ||||||
---|---|---|---|---|---|---|
All Specimens Tested, Steel Thickness Range (Measured) in. [mm] | ||||||
Material Category | <1/16 [<1.6] | >1/16 to <1/8 [>1.6 to <3.2] | >1/8 to 3/16 [>3.2 to < 4.8] | >3/16 to <1/4 [>4.8 to <6.4] | >1/4 to <5/8 [>6.4 to <16.0] | >5/8 [>16.0] |
Structural Shapes | 45 | 65 | 75 | 75 | 100 | 100 |
Strip and Bar | 45 | 65 | 75 | 75 | 75 | 100 |
Plate | 45 | 65 | 75 | 75 | 75 | 100 |
Pipe & Tubing | 45 | 45 | 75 | 75 | 75 | 75 |
Wire | 35 | 50 | 60 | 65 | 80 | 80 |
Reinforcing Bar | -- | -- | -- | -- | 100 | 100 |
Forgings and Castings | -- | -- | -- | 100 | 100 | 100 |
Table 2: Coating Thickness GradeA | ||||
---|---|---|---|---|
Coating Grade | mils | oz/ft2 | µm | g/m2 |
35 | 1.4 | .8 | 35 | 245 |
45 | 1.8 | 1.0 | 45 | 320 |
50 | 2.0 | 1.2 | 50 | 355 |
55 | 2.2 | 1.3 | 55 | 390 |
60 | 2.4 | 1.4 | 60 | 425 |
65 | 2.6 | 1.5 | 65 | 460 |
75 | 3.0 | 1.7 | 75 | 530 |
80 | 3.1 | 1.9 | 80 | 565 |
85 | 3.3 | 2.0 | 85 | 600 |
100 | 3.9 | 2.3 | 100 | 705 |
A: The values in micrometers µm are based on Coating Grade. The other values are based on conversions using the following formulas: mils=µm x 0.0.937; oz/ft2= µm x 0.02316; g/m2 = µm x 7.067 |
© 2025 American Galvanizers Association. The material provided herein has been developed to provide accurate and authoritative information about after-fabrication hot-dip galvanized steel. This material provides general information only and is not intended as a substitute for competent professional examination and verification as to suitability and applicability. The information provided herein is not intended as a representation or warranty on the part of the AGA. Anyone making use of this information assumes all liability arising from such use.