Original Equipment Manufacturing
A variety of original equipment manufacturing (OEM) products have utilized hot-dip galvanized steel for more than a century because of its outstanding durability and maintenance-free qualities. Furthermore, there are continually new manufactured products looking to hot-dip galvanizing as an opportunity to enhance and improve the existing product.
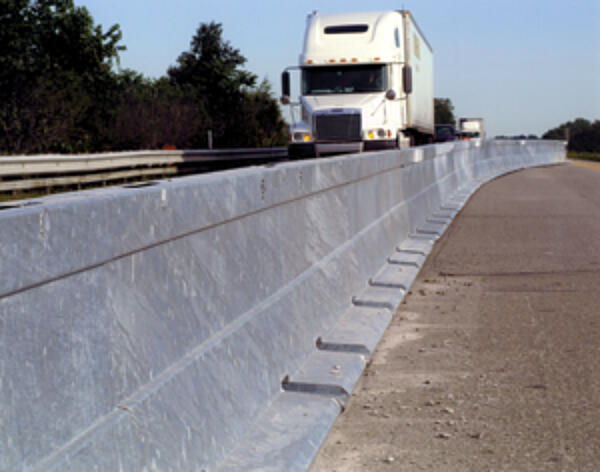
Some products that have recently seen an increase in hot-dip galvanized steel usage are commercial and residential construction products, such as brick lentils and scaffolding, material handling equipment (conveyors, racks, WIP containers, etc.), and truck and trailer bodies. However, the possibilities are virtually endless when it comes to steel products in need of superior corrosion protection.
In the US, more than $121 billion is spent annually on corrosion protection systems, regardless of their suitability and effectiveness; which arguably is not effective in many cases as the annual cost of metallic corrosion exceeds $496 billion. This shows manufacturers can benefit from forward thinking and corrosion mitigation planning to ensure their products can withstand the conditions in which they are used.
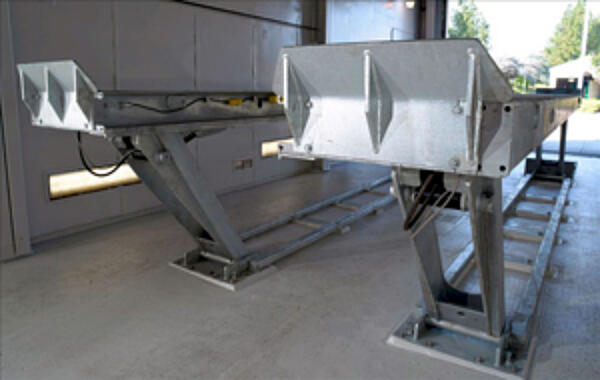
The truck and trailer industry has a long history with hot-dip galvanized steel, such as in U-haul trailers, which have utilized the coating since the early 90s. However, this market continues to grow and evolve with many different truck and trailer companies and products realizing the benefits of hot-dip galvanized steel. From fire engines, to tow trucks, to salt spreaders, hot-dip galvanized steel is quickly becoming the material of choice in this OEM market.
In addition to its corrosion resistance, hot-dip galvanized steel is used in countless OEM products because of its cost savings, durability, sustainability, safety, maintenance-free performance, and even aesthetics. The modern, industrial appearance of hot-dip galvanized steel is often the standard for equipment and rugged products.
Original Equipment Manufacturing Case Study
Water Wheels, Baltimore, MD- Galvanized starting in 2014
The water wheel will be a highly visible piece of Baltimore's Downtown Inner Harbor. Its task is to clean up the trash that gets dumped into the water on a daily basis. The wheel, capable of removing 50,000 pounds of trash per day, will bring the city's goal of making the harbor clean enough for recreational use by 2020. It is estimated the wheel will stay in use for at least 15 years as it is both solar and water powered. Galvanizing was the preferred coating because of the sustainability factor and to protect the wheel from weather elements as well as constant contact with water. With Baltimore's Inner Harbor being such a big tourist attraction, the designer wanted to ensure visitors didn't have a rusted eye sore to look at for the next 15 years. Hot-dip galvanizing will protect the water wheels of the Baltimore's Inner Harbor for years to come.