Solar
Solar energy, radiant light and heat from the sun, has been harnessed by humans since ancient times using a range of ever-evolving technologies. Solar radiation accounts for most of the available renewable energy on earth, but only a minuscule fraction of the available solar energy is used. In order to protect solar investments and ensure they are a reliable power source, proper corrosion protection methods should be in place for the racking structures. Because of the remote location or limited accessibility of many solar projects specifying a system that can withstand the constant exposure to the unforgiving sun's heat and UV rays without maintenance is an important consideration.
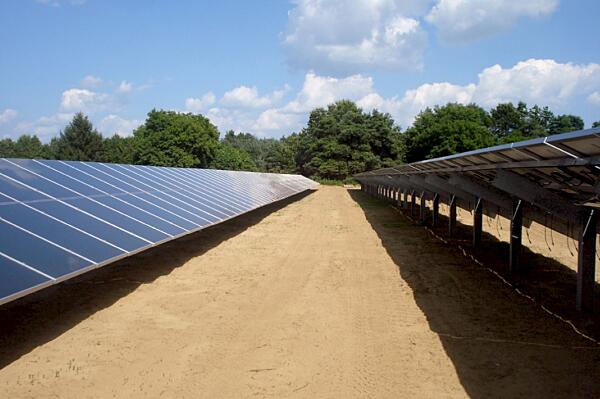
As they lie stretched out soaking and baking in the sun's rays, solar panels' racking systems and support structures are constantly exposed to damaging UV rays. Many materials, such as paint or even concrete, require special care to maintain the integrity of the coating or structure under such circumstances. Many paints are sensitive to UV light and begin degrading as soon as exposed. Blistering and peeling paint causes underfilm corrosion of the steel, leaving it inadequately protected and open to corrosion. The zinc in the hot-dip galvanized coating is unaffected by UV light. Zinc oxide, one of the corrosion products created by the coating's zinc patina, effectively blocks UVA and UVB rays and is found in every sunblock product on the market.
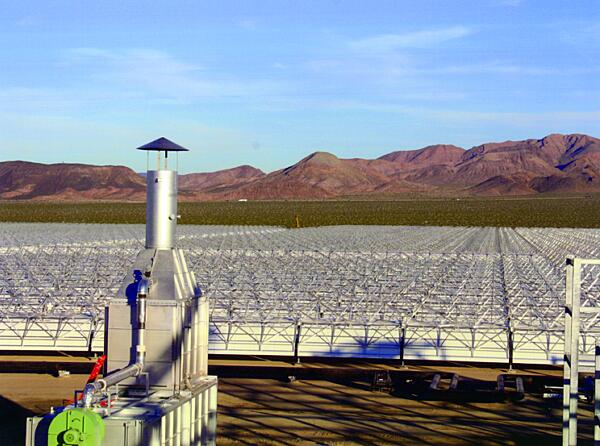
Solar projects are exposed not only to UV rays, but also to extreme temperatures in the remote locations they are installed to ensure they are left undisturbed and retain the most sun exposure possible to generate power. The small community of Boulder City, NV, boasts a very large solar farm. With temperatures reaching 114 degrees in the hot, dry Nevada summer, the racking systems, frames, and support structures must be able to withstand these extreme temperatures. Hot-dip galvanizing's protective coating is unaffected by continuous exposure to temperatures between -40 F and 392 F, meaning it will perform in virtually any environment without degradation.
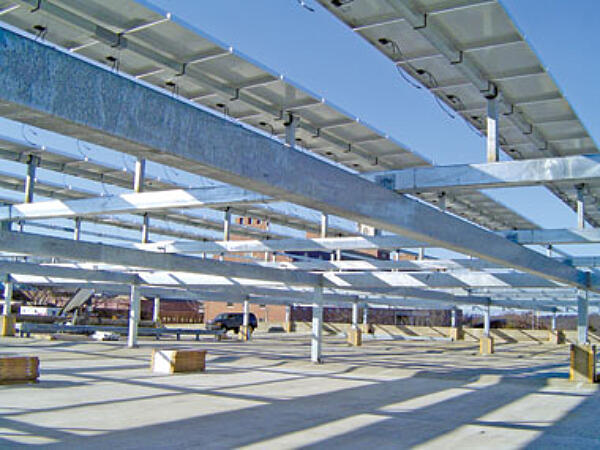
Because solar farms need vast tracts of wide open, sun-exposed land to spread out their photo electric cell structures, they are often located in remote locations where space is available and affordable. Because traveling to and from these locations for routine maintenance wastes time, money, and fuel, it is advisable to specify a corrosion protection system for the racking systems and support structures that require the least amount of maintenance. Many smaller solar arrays are now being placed on rooftops, canopies, light poles, and parking structures to power nearby buildings and/or infrastructure.
As large-scale renewable energy projects are becoming common-place in multiple locations across North America, the need for sustainable, durable, maintenance-free solar structures grows. Hot-dip galvanizing's maintenance-free durability perfectly complements the clean, renewable energy source it is protecting.
Solar Case Study
Metropolitan Tea- 702 kW Solar PV Installation-Toronto, ON; 2012
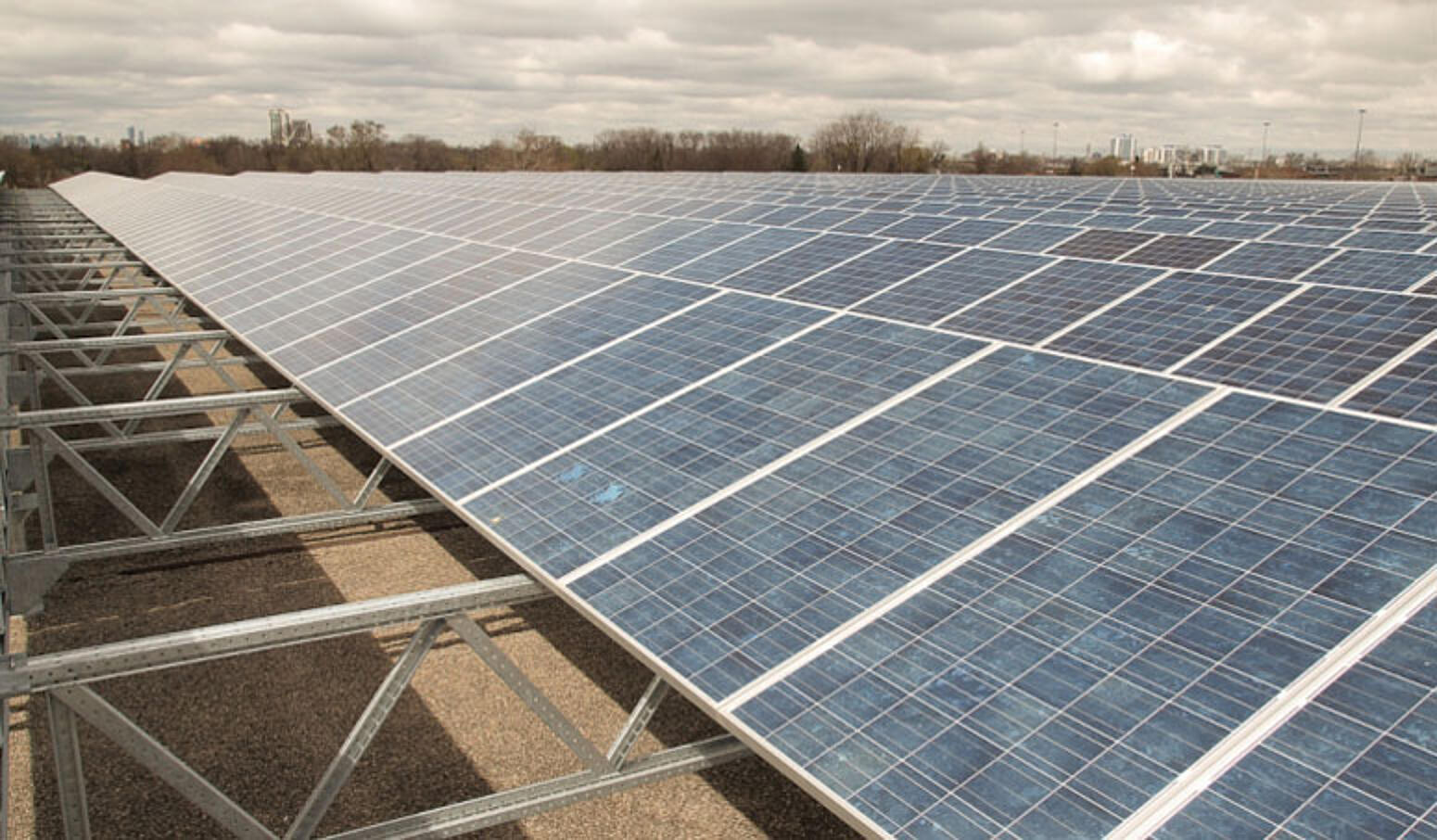
Typical rooftop solar structures are constructed of extruded aluminum materials. NorthGrid Solar has been developing a unique, elevated solar structure for rooftop applications. In designing a structure for the Metropolitan Tea Company project that was required to elevate and support solar panels over 30-40' spans, steel was determined to be a stronger and more cost effective solution. NorthGrid Solar opted for post-fabrication hot-dip galvanized finish instead of using pre-galvanized materials. Long-term exposure to the highly-variable urban Ontario climate mandated superior corrosion protection not only due to aesthetic reasons because of the high visibility above the roof, but also for structural reasons due to the use of thin 12 and 14 gauge roll-formed materials. Hundreds of feet of steel cable tray for electrical runs were supplied as hot-dip galvanized finish, as were the strut channel members used for mounting electrical enclosures. The finish remains durable through sometimes rough handling during shipping and construction, and is cost effective versus other corrosion-resistant materials such as aluminum or stainless steels.