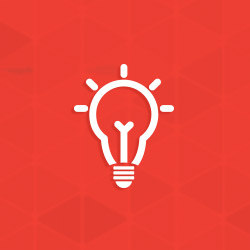
Transportation, Handling & Storage of Hot-Dip Galvanized Articles
How can I avoid damage to HDG articles during transportation, handling, and storage?
A unique characteristic of the hot-dip galvanized (HDG) coating is the development of tightly-bonded (~3,600 psi), abrasion resistant intermetallic layers. The hardness of these inner layers provides exceptional abrasion resistance while the outer and more ductile Eta layer provides some impact resistance. The combined benefits of these layers make damaging the HDG coating very difficult during rough handling, transportation, installation, as well as in service. Typically, no special handling techniques, nor specific rigging/tie-downs are required to handle HDG steel (HDG coatings can withstand chains used during transport).
In cases where special handling is required for aesthetics, galvanizers will work with customers to meet those needs.
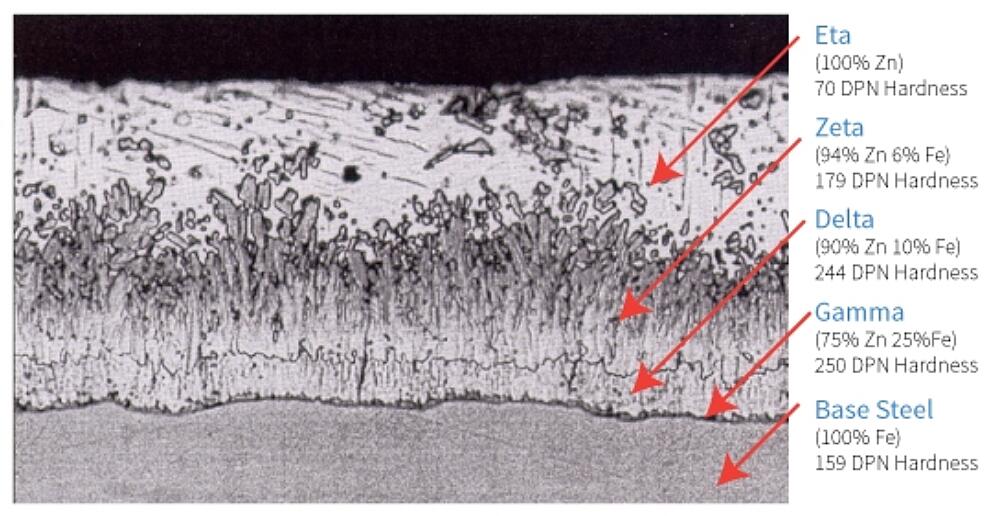
Despite hot-dip galvanizings superior durability over other industrial coating systems, it is possible to damage the coating during handling or affect coating performance by storage in a poor environment. Where it is practical, certain practices can be utilized to minimize or eliminate the potential for coating damage. The following practices should be shared with galvanizing operations personnel, the customer, and any logistics personnel to ensure expectations are met with regard to coating quality:
- Avoid stacking or contact of hot articles during cooling
- Minimize punching, drilling, or other fabrication techniques after hot-dip galvanizing
- Transport should be under dry, well-ventilated conditions.
- During transport, ensure loads are placed on the truck so the articles can be easily unloaded by forklift (i.e. on suitably sized/rated pallets, in forklift-compatible containers), and are tied down securely with restraints of the proper load rating.
- For reinforcing bar, follow recommended HDG rebar field handling techniques
- When bending articles after the hot-dip galvanizing process, perform bending at slower speeds -- some cracking or flaking of the galvanized coating at the bend may occur
- Avoid storage in contact with corrosive substances or chemicals
- Ensure proper storage and airflow to prevent the development of wet storage stain. Detailed information on best storage practices can be found within the AGA publication Wet Storage Stain.
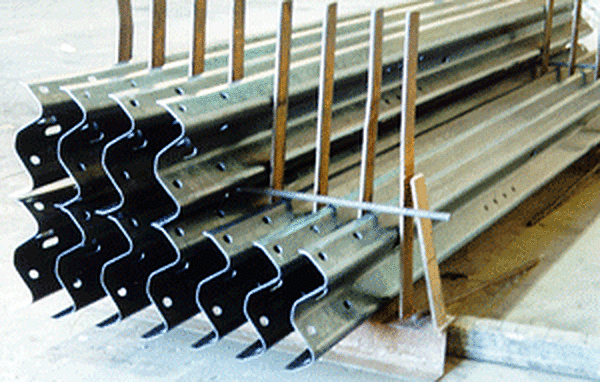
Additional handling recommendations may be required when hot-dip galvanizing reactive or thick steels susceptible to developing excessive coating thicknesses. As the galvanized coating grows to and exceeds 8-10 mils in thickness, it becomes more brittle than thinner coatings. The brittle coating can then flake off the steel when the part is struck, such as during transport or assembly in the field. In order to minimize or eliminate the occurrence of flaking on articles with excessive coating thickness, utilize the following practices where practical:
- Minimize the movement of articles directly with a forklift or use lift rigging
- Avoid dropping, hitting, or other impact forces during loading, handling, or installation
- Avoid the use of impact tools, especially for bolt installation
- Lift long or thin articles with lifting points of sufficient quantity and location to avoid bending or bowing during suspension
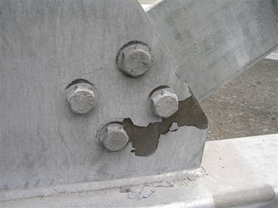
Should handling or storage damage occur during galvanizer ownership, then it must be repaired or re-galvanized based on maximum allowable repair size criteria. However, once the item is delivered or under customer ownership, then any damage resulting from trucking, handling, storage or installation techniques is not grounds for rejection nor is the galvanizer responsible for repairs. Instead, these areas can be repaired in the field without any restriction to maximum allowable repair size. Keep in mind that small scratches (< 1/8") in mildly corrosive climates do not necessarily need to be repaired as the cathodic protection of the zinc will prevent extensive corrosion of the steel. In highly corrosive environments, where corrosion protection is of paramount concern, repairs should be made to ensure the longest possible service life for the steel. Large scratches should always be repaired, regardless of environment.
Location Where Damage/Flaking Occurred: | At Galvanizing Plant or Under Galvanizer Ownership | Trucking or Transportation by Customer | After Acceptance by Customer or Delivery to Jobsite |
Responsible Party for Touch-up & Repair: | Galvanizer | Customer | Customer |
Reference to Maximum Allowable Repair Size: | ASTM A123, 6.2.1-6.2.2 ; ASTM A153, 4.5; ASTM A767, 9.1 | None | None |
Touch-up & Repair Requirements: | ASTM A780 | ASTM A780 | ASTM A780 |
Prior to galvanizing, the terms and conditions should address and clearly define when the change from galvanizer to customer ownership occurs. It might also be prudent to have clauses in your purchase orders limiting responsibility when galvanizing reactive steel that does not meet the recommended chemistry of ASTM A385. For guidance on developing a terms and conditions and identifying responsibilities before and after galvanizing, contact the AGA or refer to the Green Value Proposition available in the Members area of the website.
© 2025 American Galvanizers Association. The material provided herein has been developed to provide accurate and authoritative information about after-fabrication hot-dip galvanized steel. This material provides general information only and is not intended as a substitute for competent professional examination and verification as to suitability and applicability. The information provided herein is not intended as a representation or warranty on the part of the AGA. Anyone making use of this information assumes all liability arising from such use.