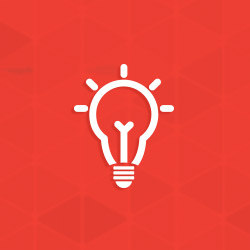
Galvanized Rebar and Reactions in Concrete
One of my customers is specifying hot-dip galvanized rebar for a new bridge. However, he is concerned about possible reactions between the zinc coating and the concrete. Are there any problems that can arise from such reactions, and is there anything special we can do to limit the reaction?
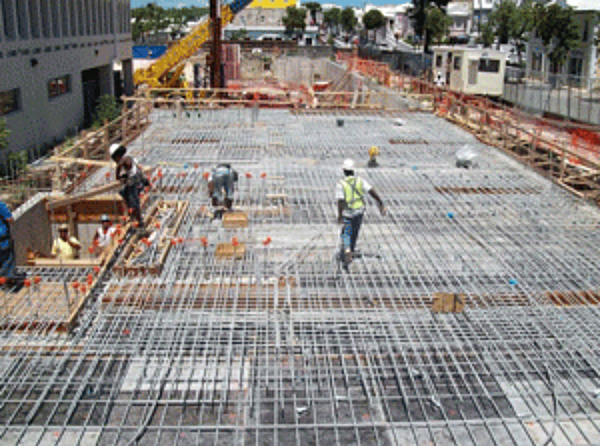
Tube reactions between galvanized reinforcement bars and concrete are only of concern during the initial curing stages of the concrete. The initial stages of curing include the time when the concrete mix is still wet. During this time the pH of the concrete is very alkaline with a pH of approximately 12.5. The wet concrete reacts with the zinc to form hydroxyzincates (Ca[Zn(OI-OH x 2 H20), which protect the zinc from further corrosion but can evolve hydrogen gas. Excessive hydrogen evolution during curing results in a more tenuous interface between the galvanized steel and the concrete, thus reducing the bond strength. Using concrete mixes with extremely high pH's may increase these reactions to unacceptable levels. Wet concrete mixes with a pH of over 13.3 have shown to significantly increase the reactions between concrete and galvanized rebar and should be avoided if possible without chromates.
The reactions that occur during the initial curing phases of the concrete can be limited by the use of chromate. Chromating the galvanized steel has shown to limit the reaction between the concrete and the zinc, thus reducing the amount of hydrogen evolved. Chromate can either be applied to the rebar directly after galvanizing, or small chromate additions can be made to the concrete mix. The amount of chromate that is added to the concrete remains in question. One study suggests that as little as 20 ppm of chromate will limit the reactions. However, it may prove beneficial to provide excess chromate (100 ppm) to ensure the reactions between the galvanized rebar and concrete are limited.
After the initial curing stages of the concrete, the reactions between the concrete and the galvanized steel cease. Once the concrete has hardened, the only access that corrosive compounds have to the galvanized rebar is through the pores of the concrete matrix. This allows the galvanized rebar to provide protection for many years.
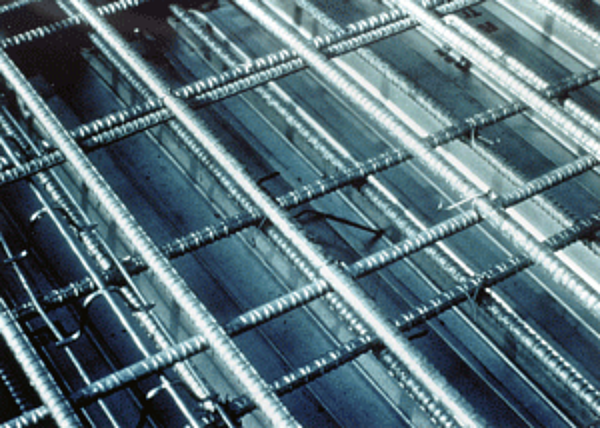
Beyond providing long-term corrosion protection, galvanized rebar poses many other chemical advantages over black rebar. The corrosion products of steel occupy a much larger volume than the metal from which they originate and the voluminous corrosion products of black steel exert a tensile stress on the surrounding concrete. Over time, these corrosion products build up pressure on the surrounding concrete. When the pressure exceeds the tensile strength of the concrete, cracking and spalling of the concrete occurs. The cracking of the concrete creates passageways that allow further corrosive media, such as chloride salt, to enter and cause further corrosion of the rebar. While the corrosion products of zinc also occupy a larger volume than its parent metal, they have been shown to disperse into the surrounding concrete matrix, unlike corrosion products of black rebar. Increased pressure due to these corrosion products is not as substantial as with black rebar and is less likely to cause cracking of the concrete.
The passivation of the zinc surface is often done by chromating the galvanized steel. The high corrosion resistance offered by the use of chromate films is attributed to the presence of hexavalent and trivalent chromium in the coating. The trivalent chromium is believed to be present as an insoluble hydrated oxide (chromium hydroxide or zinc chromate), whereas the soluble portion of hexavalent chromium imparts a "self-healing" character to the film during the oxidative (corrosive) attack by species, such as chloride ions.
The chromate film on the galvanized reinforcing steel is formed by the chemical reactions of hexavalent chromium with a metal surface in the presence of other components, or "activators" in acid solution. Hexavalent chromium is partially reduced to trivalent chromium during the reaction, with a concurrent rise in pH, forming a complex mixture consisting largely of hydrated basic chromium chromate (Cr203 Cr03 x H20) and hydrous oxides of both chromium and the basis metal (zinc). As the acid is consumed, the combining power of chromium in the solution changes and precipitates chromium hydroxide. A film builds until the face next to the zinc becomes nonacid and this stops the reaction. The resulting gel-like film is allowed to harden. Chromate coatings on galvanized steel are usually yellow and consist of a mixture of trivalent and hexavalent chrome solution. The chemical reaction of the chromate to the galvanized steel is shown below:
- Reduction of hexavalent chromium to trivalent chromium 3Zn + 2Cr+6 ------> 3Zn+ 2Cr+3
- Dissolution of metal by acid (hydrogen loss) accompanied by a local rise in pH at the metal interface Zn + 2H------->Zn + H2 (gas)
A redox reaction occurs at acidic pH where hexavalent chromium is reduced to trivalent chromium while zinc is oxidized.
- Zn ------>Zn2+2e
- HCrO4+14H+6e ------> 2Cr2+7H2O
The primary reason for the use of chromate treatments on the galvanized steel parts is to prevent the formation of wet storage stain during the first six weeks after galvanizing. The zinc coating is most vulnerable to the formation of excessive amounts of zinc oxide and zinc hydroxide during this period. The thin layer of chromate passivation layer inhibits the formation of these zinc oxides. The coating generally lasts about six weeks before it is consumed. Galvanized steel will then weather naturally after the chromate is gone.
Chromate passivation treatments are used to control reactions between the zinc and the concrete. The main reaction that chromate treatment prevents is the hydrogen evolution that may affect the bonding properties between the zinc and concrete. Zinc is amphoteric (reactive in acidic and alkaline environments) so the maximum rate of attack on zinc occurs in alkaline conditions over a pH of 12.5. The passivation of zinc is effected in the pH range of 8 to 12.5, due to the initial formation of a layer of zinc hydroxide and subsequently of a complex calcium zinc compound, calcium hydroxy-zincate (Ca[Zn(OHbl 2H20)]. The reaction of zinc with the concrete effectively ceases in a few days and gives just sufficient corrosion products to ensure a strong and reliable bond to the concrete when fully hardened. The bonding between galvanized rebar and concrete is essential for the reliable performance of concrete structures. Many factors, such as concrete mix and additives, curing conditions, and age, may affect the bonding between the galvanized steel and concrete. The chemical reaction that is of concern is the reaction of zinc with calcium hydroxide.
This reaction occurs during the curing of the concrete. During the curing process, hydrogen gas evolution occurs between the galvanized rebar and the concrete. The use of a passivation treatment, such as the use of chromates, can help to reduce the hydrogen gas from forming. In solutions with such a high pH, the zinc is attacked by the alkalis (calcium hydroxide) in the fresh concrete, leading to the formation of calcium hydrozincite and hydrogen. This reaction could give rise to poor adhesion. Once the concrete sets, the hydrogen evolution ceases; the coating of calcium zincate formed apparently provides a protection to the reinforcement and no further attack takes places after initial setting. Tests of the bond strength on galvanized rebars showed equal to or slightly better bond performance when compared to black rebars.
Laboratory studies have shown other concrete design factors affect the corrosion rate of zinc. Slightly higher corrosion rates are seen as the water-to-cement ratio of the concrete increases. Also, a thicker concrete-cover above the galvanized rebar has shown to reduce its potential of reacting with carbonation reaction products, such as calcium carbonate, that may permeate into the concrete matrix. If damaged, galvanized rebar should not be repaired using compounds that contain aluminum. Aluminum is not stable in concrete and may cause other reactions with concrete. I hope this answer provides "concrete" evidence that galvanized rebar, when used correctly, will protect your customers' bridge for generations.
Learn more about galvanized rebar and earn continuing education credits by requesting an in-person seminar or taking our online rebar seminar.
© 2025 American Galvanizers Association. The material provided herein has been developed to provide accurate and authoritative information about after-fabrication hot-dip galvanized steel. This material provides general information only and is not intended as a substitute for competent professional examination and verification as to suitability and applicability. The information provided herein is not intended as a representation or warranty on the part of the AGA. Anyone making use of this information assumes all liability arising from such use.