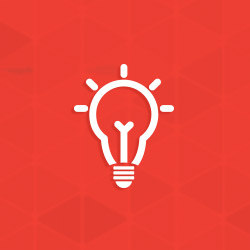
Cracking in the Heat Affected Zone
When galvanizing a frame structure, we took it out of the kettle, and I noticed some small cracks around one of the weld areas. What is causing this cracking?
The weld area and surrounding heat-affected-zone (HAZ) can change the steel properties in the local area around the weld. This area can become a highly stressed location and can attract steel imperfections during the heating of the steel assembly. So, this area is experiencing stresses from the welding operation, steel impurities, and the two steel sections trying to move during the heating of the steel assembly. The ductility of the steel is usually sufficient to prevent anything from happening when all of these stresses combine; but when the conditions are above the yield stress of the material, then the steel reacts by forming a small crack somewhere near the weld area.
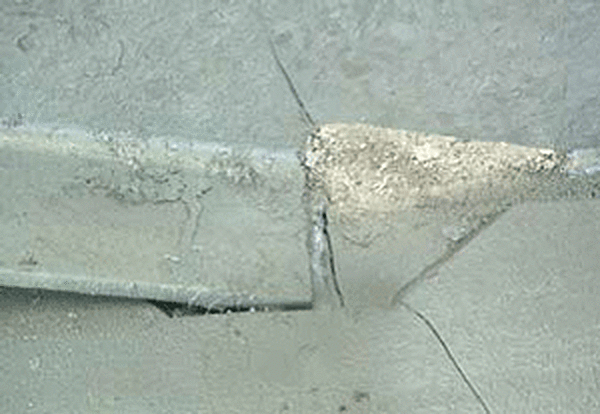
The small crack can then expand as zinc and lead wick into the crack, pushing it into the surrounding steel material. The zinc cannot penetrate openings less than 3/32 in.; but in this case, as the crack opens under the heating of the steel, the zinc is pulled into the crack by wicking action and helps the crack expand and grow. Other low melting point metals like tin and lead can also be found inside the crack as they will also penetrate the void. They will be found near the tip of the crack since they stay molten for a long time after the part is removed from the heat source of the molten zinc in the kettle.
This whole process is known as liquid metal embrittlement (LME), but it does not mean that the steel parts are embrittled. The only embrittlement that occurs is the area around the weld and the HAZ where the small cracks can form. This same process has occurred many times with cope cut beams, where the cope area becomes the highly stressed region that attracts more stresses and can experience cracking at the 90-degree bend of the cope.
What is really tough about this cracking issue is it does not happen all of the time, but only occasionally when the conditions are just right. For cope cracking the frequency of occurrence is about 10%. This makes it very difficult to predict and to prevent. During the mid 90s, ILZRO did a very thorough study of the causes behind cope cracking. The result of that work was there were a number of contributing factors that went into making a certain steel beam susceptible to this type of cracking. There are many different factors needed to exceed a threshold level before the steel would be susceptible to cracking. The most controllable factor was the residual stress in the area of the cope cut. This factor was reduced by applying a weld bead along the edge of the cope on both sides. The main benefit of this process was to reheat the area of the cope and relieve some of the residual stress in the area. This change to the fabricating procedures has lowered the occurrence frequency to less than 1.
Since we are talking about many factors necessary for a steel assembly to be susceptible to cracking, what can the galvanizer do to avoid this type of situation? One of the major controllable factors is progressive. If there are large steel pieces welded together into a frame that must be progressively dipped, then the galvanizer should notify the fabricator there is a finite chance the weld areas will crack. If the fabricator gives the go ahead, then the galvanizer has made him aware of the potential problem. If the part can be single dipped in a larger kettle, then the cracking may be avoided.
What do you do about the piece that has cracked? Experience with cope cracking has shown the piece can be repaired and put into service. The crack is gouged out to about a ½ in. beyond the tip and the area is backfilled with weld material. This repair is touched-up according to ASTM A780 to provide corrosion protection. The part is then ready to be put into service if approved by the engineer of record. Past experience and inspection of cope cracks repaired using this process show the beams experience no further issues, many in place for over 15 years.
Zinc can be pulled into a crack by wicking action, which will cause the crack to expand and grow. The heat-affected-zone is a highly stressed location. When the conditions are above the yield stress of the material, the steel reacts by forming a small crack somewhere near the weld area as delineated by the markings on the piece to the left.
© 2025 American Galvanizers Association. The material provided herein has been developed to provide accurate and authoritative information about after-fabrication hot-dip galvanized steel. This material provides general information only and is not intended as a substitute for competent professional examination and verification as to suitability and applicability. The information provided herein is not intended as a representation or warranty on the part of the AGA. Anyone making use of this information assumes all liability arising from such use.