Masking Materials for Preventing Hot-Dip Galvanizing
2010
Authored by Dr. Tom Langill
Authored by Bernardo A. Duran III
Background
Masking materials, also called stop-off materials, are products applied to steel in specific areas prior to hot-dip galvanizing to prevent zinc from reacting with and adhering to the steel. Masking is done for a myriad of reasons. For example, sometimes it is preferable to prevent galvanizing on large areas of steel that will be welded, rather than removing the zinc coating later. Masking materials are also sometimes applied to threads when precise fit is necessary and the additional width of the galvanized coating would cause fit issues. Another reason to mask steel is to give a higher slip factor on some faying surfaces. Many different types of products have been used as masking materials. Some products are specifically designed for the purpose of preventing galvanizing, and other products from other industries or for other uses have been found to work well at masking steel prior to galvanizing.
Introduction
An American Galvanizers Association (AGA) study was conducted to determine the effectiveness of masking materials at preventing adhesion of zinc to steel during galvanizing. This study is important because masking materials are commonly used, and until now, there was no definitive study that looked at the efficacy of various products used to prevent galvanizing. The information obtained in this study will give galvanizers and fabricators detailed facts on the performance of various masking materials, as well as provide data on application and removal of the masking materials after hot-dip galvanizing.
Test Procedure
In this study 15 masking materials were tested. Some of these materials are currently used to mask steel, and others have been used in the past with some success. In addition to past performance, the products were chosen based on their availablility and recommendations from AGA members.
The study consists of two phases. The goal of Phase 1 testing is to determine the effectiveness of the various masking products in masking the steel surface from zinc. The products that successfully masked steel in Phase 1 were included in Phase 2 testing. The goal of Phase 2 is to determine the performance of the successful materials from Phase 1 testing when given shorter cure times. Attempting to restore the original appearance of the steel (by chemical cleaning) is also a goal in Phase 2.
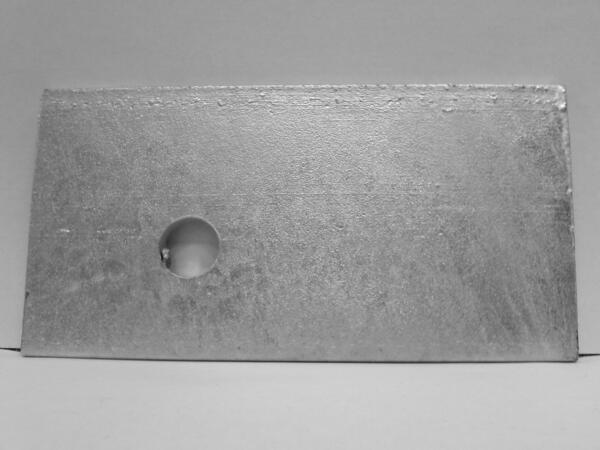
The masking materials were tested on three different types of surfaces; flat plate, buried threaded holes, and bolt threads. Two types of flat plate were used in the study. The first type of flat plate (see Figure 1) was approximately 3" x 6". The masking materials were applied to the steel away from the hole. The masking area had a width of 3" and a length of a little less than 4".
All masking materials were applied to the steel prior to the cleaning steps of the galvanizing process, meaning the masking materials were subjected to a caustic bath, pickling bath, and flux bath. It was important to determine if the masking materials could survive the cleaning chemicals, because if they could survive, the masking materials could be applied at the fabricator's facility, and thereby save the galvanizer the time and trouble of applying the materials.
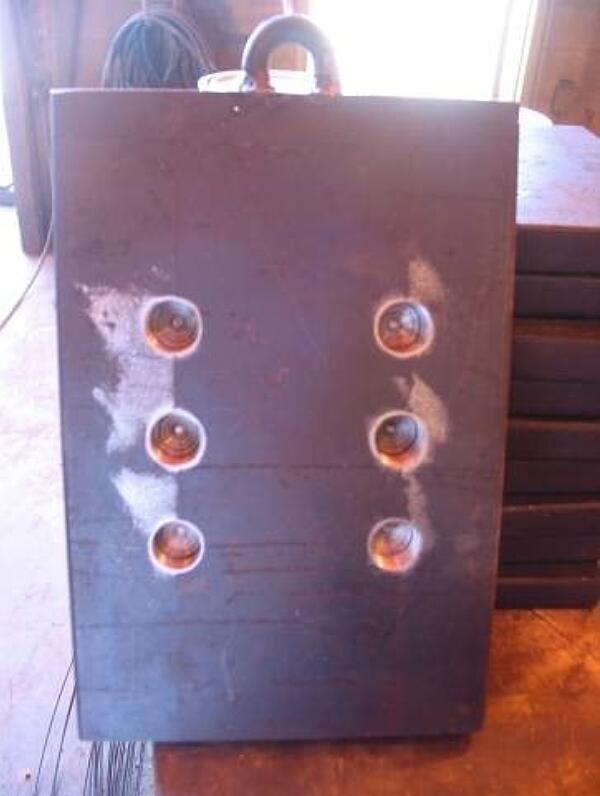
Some of the plates were drilled and tapped to provide a plate with a buried threaded hole to test the masking materials (see Figure 2). The buried threaded holes were 2½" deep holes drilled into a 3" thick plate (see Figure 2). Buried threaded holes were used only in Phase 1 testing. The bolts used in the study were ¾" in diameter and approximately 2 ½" in length (see Figure 3).
The masking materials were applied to the plates with a foam brush and then spread in the masked areas until an even consistency was achieved.
For the buried threaded holes the masking products were simply poured or squeezed into the holes.
For the bolt threads, the masking materials were applied by either dipping the bolts directly into the bottle of the material, if there was enough room, or spread onto the threads using a foam brush. The material was spread onto the threads to achieve even thickness.
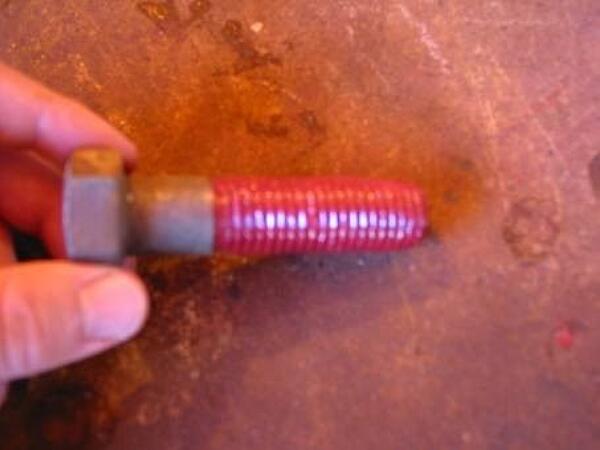
The masking materials for all surface types were applied prior to the chemical cleaning steps of the galvanizing process. This ensured the masking materials could stand up to the cleaning agents and would remain on the steel prior to galvanizing.
Masking products were removed by using a metal-bristled brush. The materials were scrubbed off the surface and then compressed air was used to blow off the debris. In Phase 2 testing, scrubbing the cleaned steel with a nylon bristled brush and Simple Green solution was also performed to determine if the original steel finish could be restored. A grinder was also tested in Phase 2 for removing the materials on flat plate.
PHASE 1 TESTING
Masking Material Testing
Fifteen different masking materials were tested in Phase 1, including:
- Duct Tape
- Kapton Tape
- VHT Header Paint (tested only on flat plate)
- Dow Corning Compound #111
- DAP Household Adhesive Sealant
- Stop Galv
- NAPA RTV Red
- GE 100% Silicone Caulk
- Galva Stop
- Valmont Masking Compound
- Macropoxy 846
- 3M High Temperature Aluminum Tape
- Maskote Zinc Stop-Off
- ZYP Boron Nitride Lubricoat
- ZYP Boron Nitride Hardcoat
Determining the effectiveness of each masking material came down to observing how much of the masked area galvanized. The smaller the area that galvanized, the more effective the masking material.
For flat plate, greater than 90% of the masked area had to remain ungalvanized to proceed to Phase 2 testing. For buried threaded holes, almost the entire threaded area needed to remain free of galvanizing. If a few small spots of zinc were observed, the masking material was still considered effective. For bolt threads, the same criteria applied as that for buried threaded holes - almost the entire threaded area must remain ungalvanized to be considered effective.
Test 1 Results
On the flat plate, nine products failed to prevent galvanizing on a minimum of 90% of the masked area. Six products successfully prevented zinc coating a minimum of 90% of the masked area on flat plates including:
- Stop Galv
- Maskote Zinc Stop-Off
- NAPA RTV Red
- Galva Stop
- GE 100% Silicone Caulk
- Valmont Masking Compound
Only 14 of the masking materials were tested on buried threaded holes and bolt threads. The VHT Header Paint was not tested because paint cannot be easily removed from threaded areas.
Eight products failed to prevent zinc coating on the buried threaded holes. Six products successfully prevented zinc coating on the buried threaded holes, including:
- DAP Household Adhesive Sealant
- GE 100% Silicone Caulk
- Valmont Masking Compound
- Maskote Zinc Stop-Off
- Macropoxy 846
- ZYP Boron Nitride Hardcoat
Six of the 14 products failed to prevent galvanizing on bolt threads. The masking materials that did prevent zinc coating on bolt threads include:
- Galva Stop
- Stop Galv
- DAP Household Adhesive Sealant
- NAPA RTV Red
- GE 100% Silicone Caulk
- Macropoxy 846
- Maskote Zinc Stop-Off
The bolts masked with Valmont Masking Compound were lost during the galvanizing process during testing.
For more detailed information on how each masking material performed on the various surface types, and application and removal data, please see the charts in Appendix 1.
PHASE 2 TESTING
Shorter Cure Time Testing And Cleaning
The first goal of Phase 2 testing was to determine how the products that performed well in Phase 1 testing performed were applied using shorter cure times. Products tested in Phase 2 included:
- Stop Galv
- Galva Stop
- Maskote Zinc Stop-Off
- NAPA RTV Red
- GE 100% Silicone Caulk
- DAP Household Adhesive Sealant
Although Valmont Masking Compound did well in Phase 1 testing, it was not included in Phase 2 testing. Also, as mentioned earlier, buried threaded holes were not tested in Phase 2.
Shorter cure times were tested in Phase 2. These tests demonstrated the limits of the masking materials. However, it is important to note these materials should be used in accordance with the manufactures curing instructions to achieve optimum performance.
The second goal of Phase 2 testing was to determine if the original steel finish could be restored after removing the masking materials from the steel.
The criteria for determining the effectiveness of these masking materials in Phase 2 testing was the same as in Phase 1 Testing. Ninety percent or more of the masked area on plates had to remain free of galvanizing to be considered successful. For bolts, only a few small areas of zinc on the masked threads were allowed for the material to be considered successful.
For the flat plate specimens, each masking material was applied to the same areas used in Phase 1 testing. The plates had been stripped of all zinc and remaining residues from Phase 1 testing. Masking products were applied to only one side of the plates to decrease application time. Cure times included 1 and 2 hours for flat plate specimens.
For bolt threads, the masking materials were applied to the same bolts as those used in Phase 1 Testing. The bolts had been stripped of all galvanizing and debris from the Phase 1 tests. Three different cure times were tested on the bolt threads; 30 minutes, 1 hour, and 2 hours.
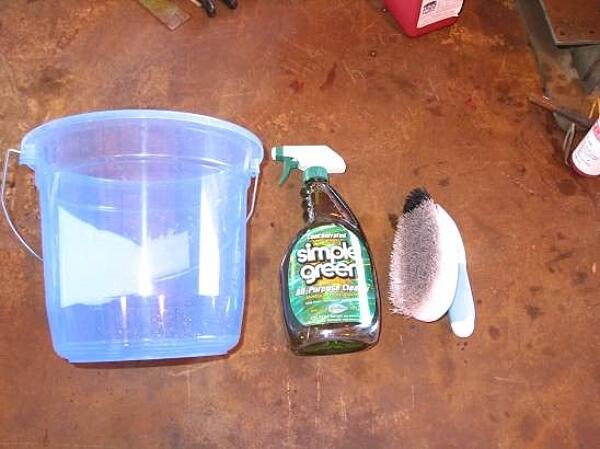
For both the flat plate specimens and the bolt thread areas, cleaning the baked on masking materials after galvanizing was attempted by scraping the steel with a metal-bristled brush and then scrubbing with a nylon brush and Simple Green solution (see Figure 4). The goal of cleaning with the Simple Green solution was to determine if the original finish of the steel could be restored after the various masking materials had baked on the surface while going through the galvanizing process. Cleaning with a grinder was attempted on the flat plate specimens only.
Test 2 Results - Flat PlateFor the 1 and 2 hour cure times only Stop Galv and Galva Stop were successful at preventing galvanizing.
Some ashy material from Stop Galv and Galva Stop remained on the plates even after scrubbing with a metal-bristled brush.
Cleaning the plates with the Simple Green solution had a negligible effect on removing the debris left from the masking materials.
Using a grinder to remove the baked-on masking materials was excessive and is not recommended. The grinder immediately went through the masking materials and attacked the steel underneath.
Test 2 Results - Bolt ThreadsThree different cure times were tested for each masking material on bolt threads, including 30 minutes, 1 hour, and 2 hours. For the 30 minute cure time Galva Stop and NAPA RTV Red were the only products that successfully prevented galvanizing.
For the 1 hour cure time, five of the six masking materials were successful at preventing galvanizing, including Galva Stop, Maskote Zinc Stop-Off, DAP Household Adhesive Sealant, NAPA RTV Red, and Stop Galv.
For the 2 hour cure time all six masking materials successfully prevented galvanizing on the bolt threads.
After galvanizing, a metal-bristled brush was used to scrape the big chunks of baked-on masking material from the threads. A Simple Green solution and nylon brush were then used to remove the remaining baked-on debris. The appearance of the bolt threads was improved for all the masking materials after cleaning with the Simple Green solution.
The cleanest bolts were those masked with Maskote Zinc Stop-Off, GE 100% Silicone Caulk, and DAP Household Adhesive Sealant. It was necessary to wash the bolts masked with NAPA RTV Red twice because of the gummy residue. Some baked on masking material remained on the bolts masked with Galva Stop and Stop Galv.
Cleaning with the Simple Green solution was done after the 1 hour curing time. If the masking materials had been given their full recommended curing time it is likely the products would have been easier to remove and would have cleaned even better.
Cleaning the masking materials from the bolt threads with a grinder was not attempted because it would damage the threads.
Conclusion
The goal of this study was to determine which commercially available masking materials work best at preventing galvanizing on masked areas. Six commercially available masking materials were identified to successfully prevent galvanizing on one or more surface types, including flat plate, bolt threads, and buried threaded holes. The successful masking materials included (in no particular order):
- Stop Galv
- GE 100% Silicone Caulk
- Maskote Zinc Stop-Off
- NAPA RTV Red
- (cont. on next page)
- Galva Stop
- DAP Household Adhesive Sealant
Additional and detailed performance data is presented in the charts in Appendix 1 and additional pictures are presented in Appendix 2.
Safety and Health Information
Material Safety Data Sheets (MSDS) should be obtained and adhered to when using these materials. Necessary personal protective equipment should be employed when appropriate. Almost all of these masking materials had nauseating smells and should be used only in well ventilated areas. It is important to note some of these products were not designed to be used in the temperature ranges of the galvanizing process.
Costs of the Masking Materials
The masking materials tested in this study have a wide range in price, which can be found in Appendix 1. In addition to the purchase price, additional costs to be considered include labor time for applying and removing the materials. Detailed application and removal times are included in the charts in Appendix 1.
Appendices
- Appendix 1: Detailed Performance Data of Masking Materials
- Appendix 2: Pictures of Masking Materials During Phase 1 Testing
© 2018 American Galvanizers Association. The material provided herein has been developed to provide accurate and authoritative information about after-fabrication hot-dip galvanized steel. This material provides general information only and is not intended as a substitute for competent professional examination and verification as to suitability and applicability. The information provided herein is not intended as a representation or warranty on the part of the AGA. Anyone making use of this information assumes all liability arising from such use.