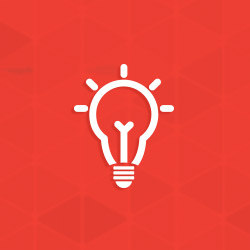
Volume of Zinc vs. Iron Corrosion Products
Reinforcing steel (rebar) and concrete is one of the most widely utilized building material combinations in modern construction. From bridges to skyscrapers, some of humankind’s greatest architectural accomplishments were only made possible because of the low cost and high dependability of reinforced concrete. The high load-bearing properties and endless structural design capabilities provided by reinforced concrete uphold modern infrastructure around the world. Extending the life of each project in a society lowers maintenance costs and reduces a structure’s overall carbon footprint. One way to prolong the life of these structures is to protect the steel reinforcement from corrosion with hot-dip galvanizing.
Although it is encased in concrete, rebar is still at risk of corrosion over time. The porous nature of concrete eventually allows corrosive elements such as water, chloride ions, oxygen, carbon dioxide, and other gases to seep through the concrete matrix and contact the rebar. As the concentration of these corrosive elements increases within concrete, particularly the chloride concentration, steel’s corrosion threshold is eventually exceeded and the rebar starts to corrode.
The byproducts of iron corrosion are several times larger than iron in its previous, uncorroded state (Figure 1).1, 2 Therefore, as the voluminous products resulting from the corrosion reaction build, so does internal pressure on the concrete. Since concrete does not flex, bend, or yield, the expansion of the corroding rebar causes the concrete to crack from the inside out. As fissures open, steel exposure to corrosive elements is increased, accelerating the overall failure of the structure. It is also difficult to detect corrosion build-up inside the concrete until it is too late, and spalling is already visible.
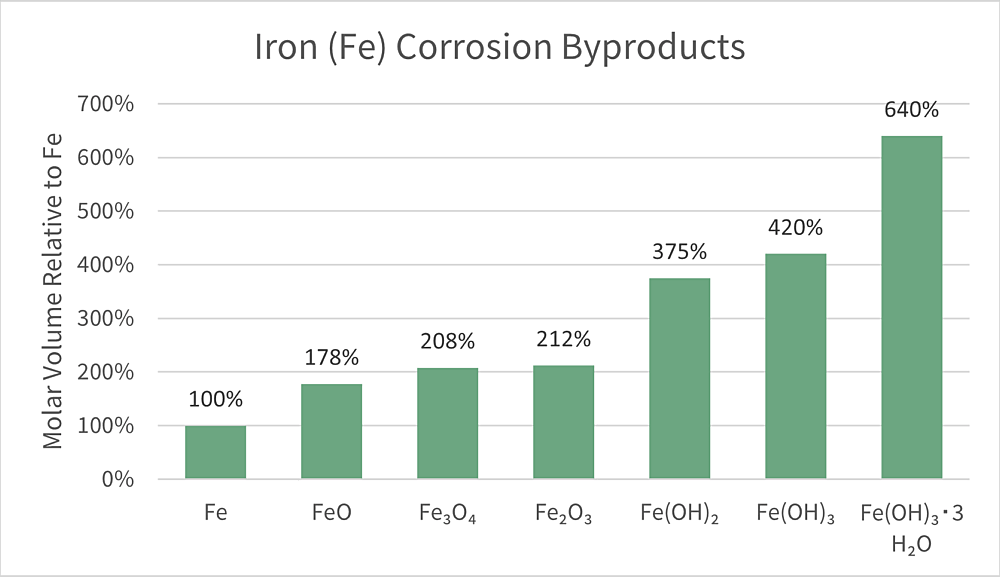
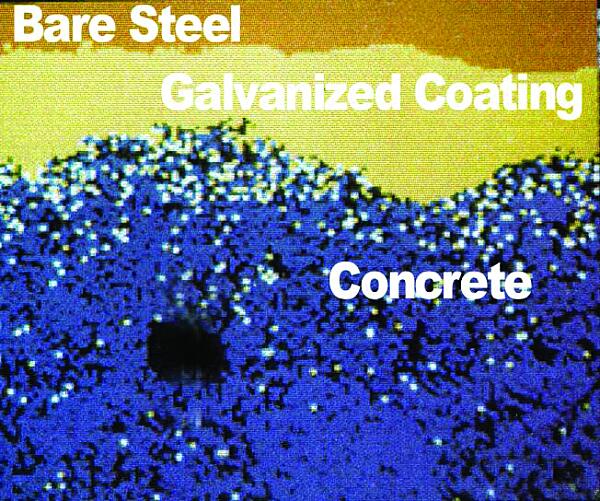
The zinc coating also corrodes differently when encased in concrete than it would if exposed to the outdoor environment. Over time in atmospheric exposure, hot-dip galvanized coatings experience natural wet and dry cycles which promote the development of a passive and stable film of zinc carbonate called the zinc patina. However, when immersed in concrete the corrosion behavior is different. After reaching the critical chloride threshold which often takes many decades, the zinc depassivates and begins to corrode in concrete, where studies observe the primary corrosion product to be zinc oxide. Regardless of the presence of concrete, black steel produces iron corrosion products which are considerably more voluminous than zinc oxide (see figure 3).
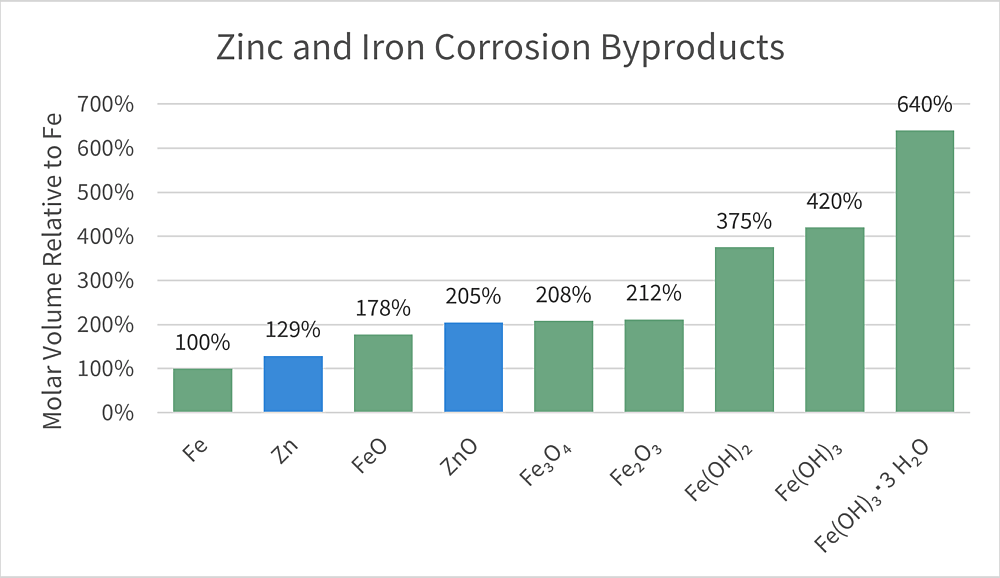
In addition to being less voluminous, zinc’s corrosion products are loose and powdery, allowing them to migrate into the cement pores, plug the pore spaces at the concrete/rebar interface, and prevent the pressure build-up and eventual concrete spalling (Figure 2). This makes it more difficult for corrosive elements to penetrate the concrete, slowing the rate of corrosion. Adversely, the spalling caused by iron corrosion opens a direct route in the concrete, allowing increased exposure to corrosive elements and accelerating damage to the steel rebar.
Fortunately, hot-dip galvanizing can provide protection to steel rebar inside the concrete. Preserving the steel and the surrounding concrete increases the lifespan of a project considerably. One important benefit of hot-dip galvanizing is the zinc coating can handle chloride concentrations at least four to five times higher than black steel, delaying the onset of corrosion.
Footnotes:
- R. Balasubramaniam, A. V. R. Kumar, P. Dillmann, Characterization of Rust on Ancient Indian Iron, Curr. Sci. 2003, 85 (11), 1546 ,
- S. Car_, Q. T. Nguyen, V. L'Hostis, Y. Berthaud, Mechanical Properties of the Rust Layer Induced by Impressed Current Method in Reinforced Mortar, Cement Concr. Res. 2008, 38 (8 – 9), 1079.
© 2025 American Galvanizers Association. The material provided herein has been developed to provide accurate and authoritative information about after-fabrication hot-dip galvanized steel. This material provides general information only and is not intended as a substitute for competent professional examination and verification as to suitability and applicability. The information provided herein is not intended as a representation or warranty on the part of the AGA. Anyone making use of this information assumes all liability arising from such use.