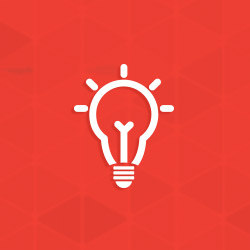
The Progressive Dip Process
What steps are involved in progressive dipping an item too large for the kettle?
Progressive dipping is oftentimes a viable option for items too large for the kettle. However, extra steps must be taken to ensure both ends of the item going into the kettle are freshly fluxed. The AGA has recently put together a series of photographs that go through the steps typically involved in the progressive dipping process.
The item progressive dipped in this example is a large, square plate in a galvanizing plant with a monorail crane. It should be noted that differing plant configurations may affect the steps involved and every galvanizer does things a little differently. As long as the item is fully coated, and meets the standards of ASTM A123, there is not necessarily a right or wrong way to progressive dip. This article covers the steps involved in a general sense.
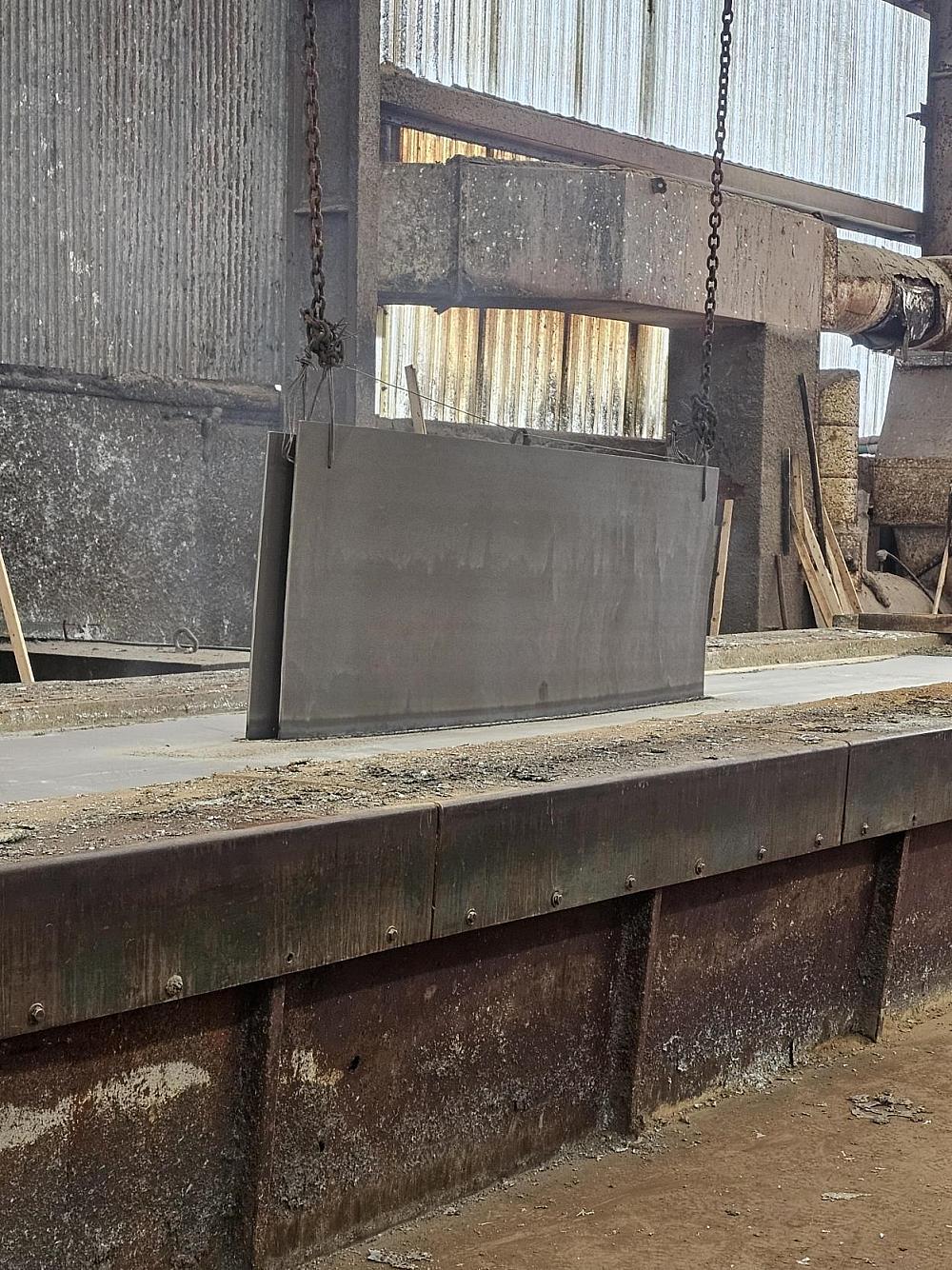
The item is submerged at least halfway in the kettle; up until this point everything regarding surface preparation has been performed according to the plant’s standard operating procedures.
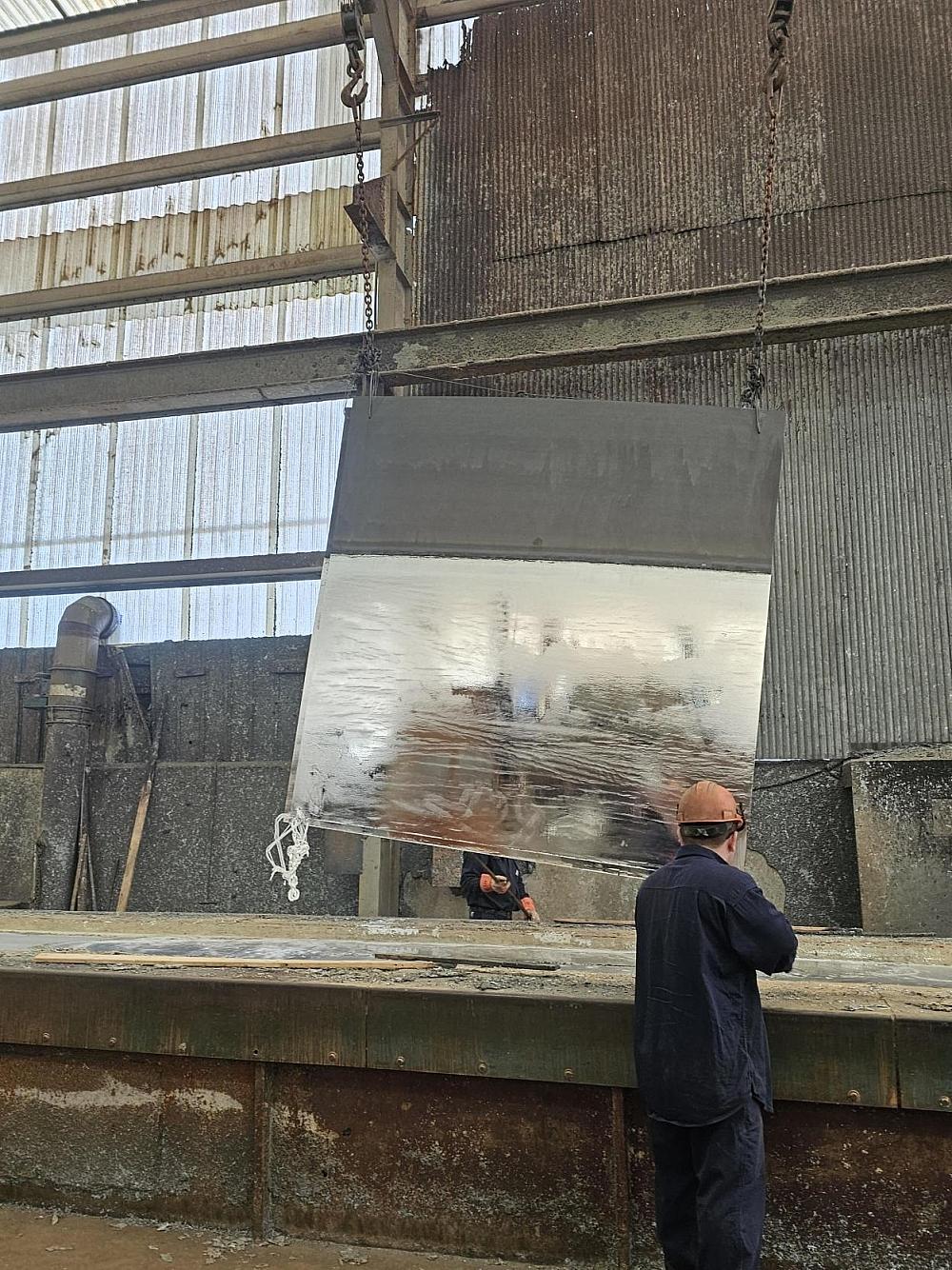
The item leaves the kettle at least halfway galvanized.
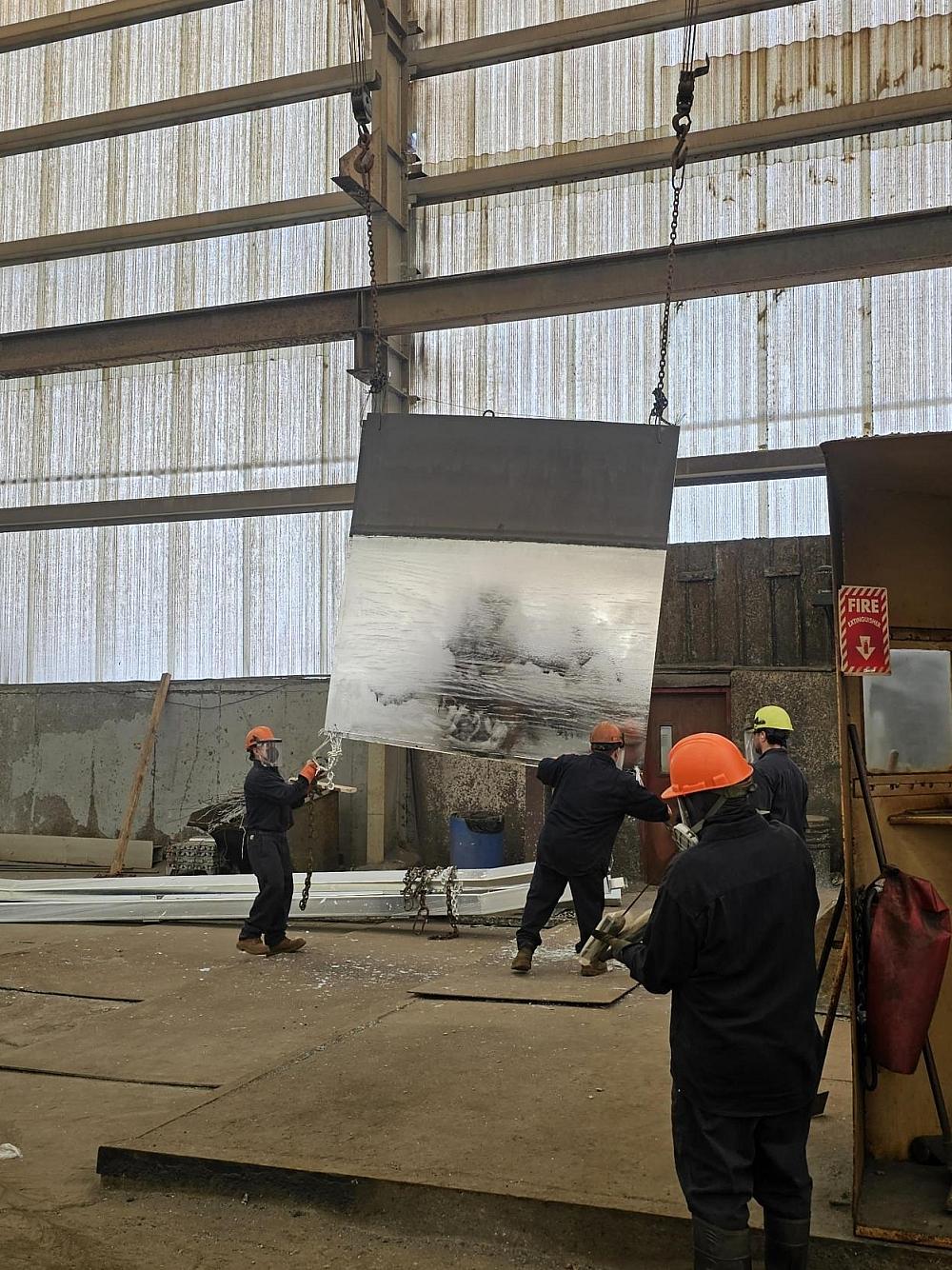
Next, the item is taken to the finishing area where the crew attaches chains to the galvanized (bottom) side.
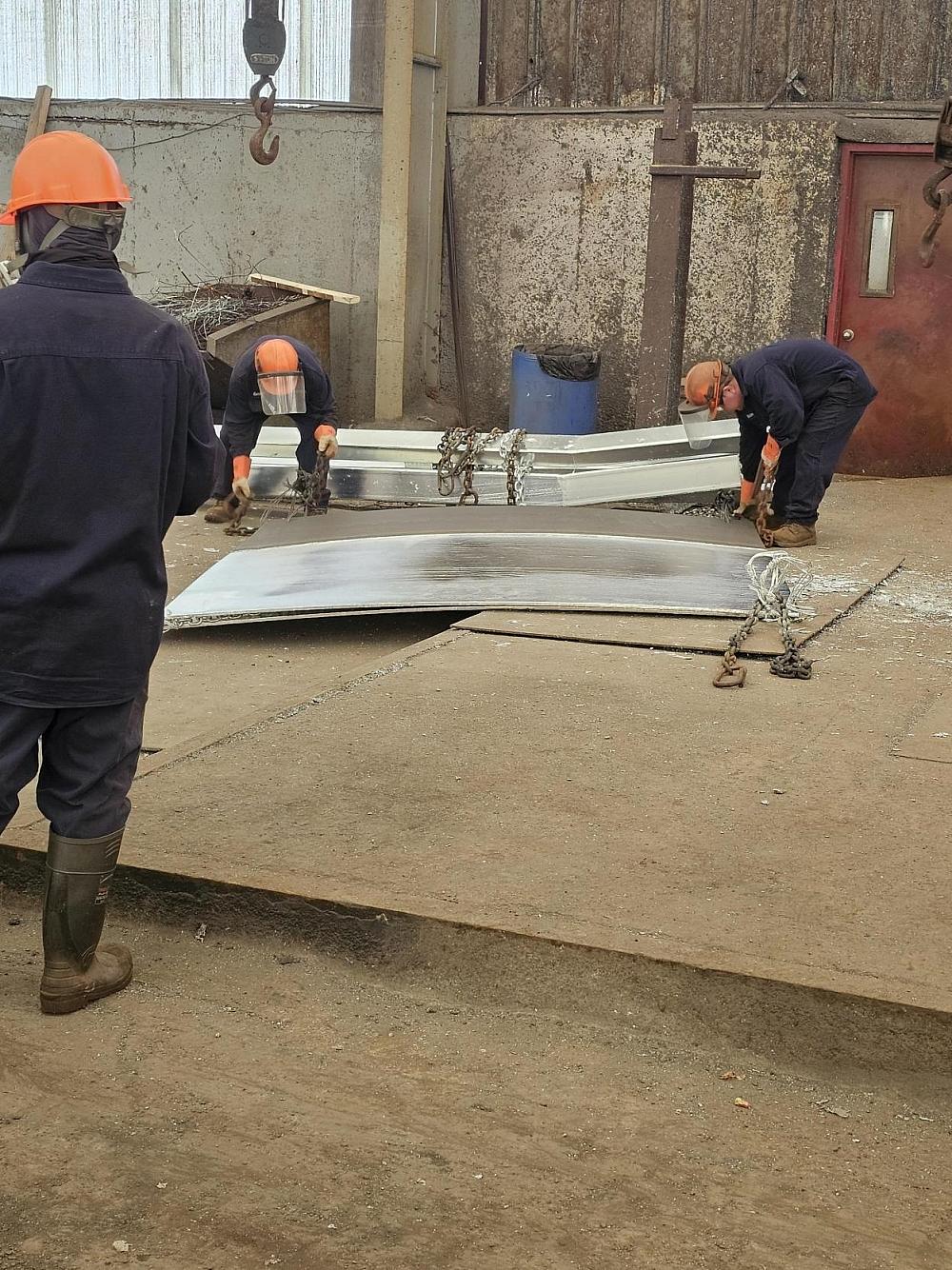
The item is then laid down and chains and other rigging materials are removed from the ungalvanized side.

The item is picked back up with the ungalvanized end downwards and is taken backward on the crane past the galvanizing kettle.
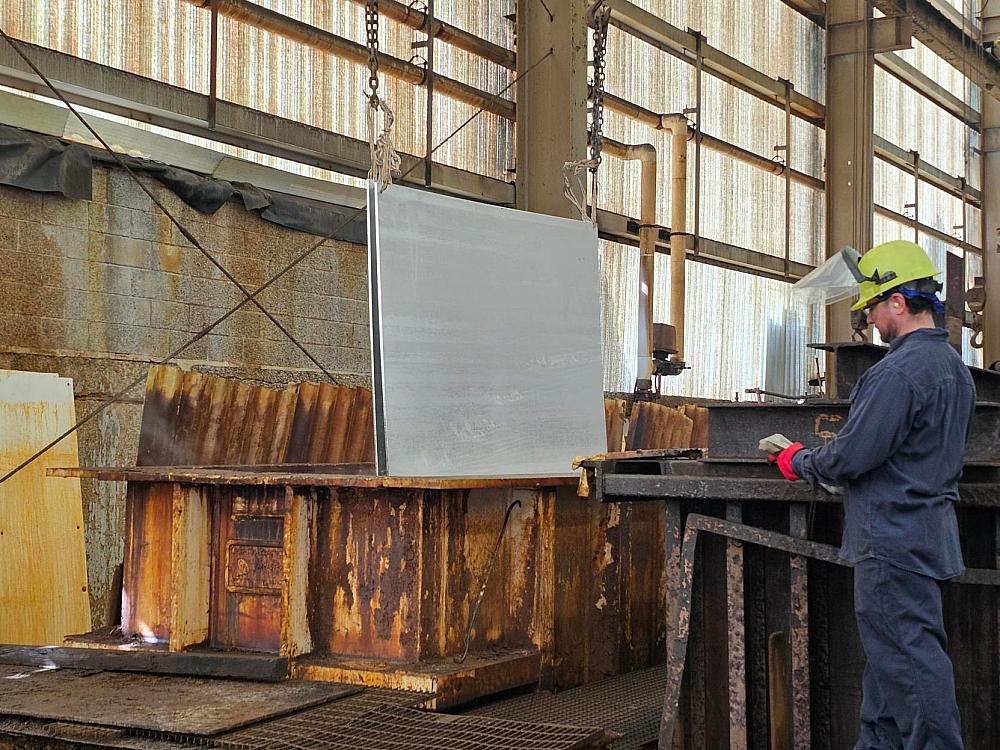
The item is taken back to the pretreatment area and the ungalvanized portion is either cleaned and fluxed, or fluxed-only (depending on variations in the galvanizer's process).
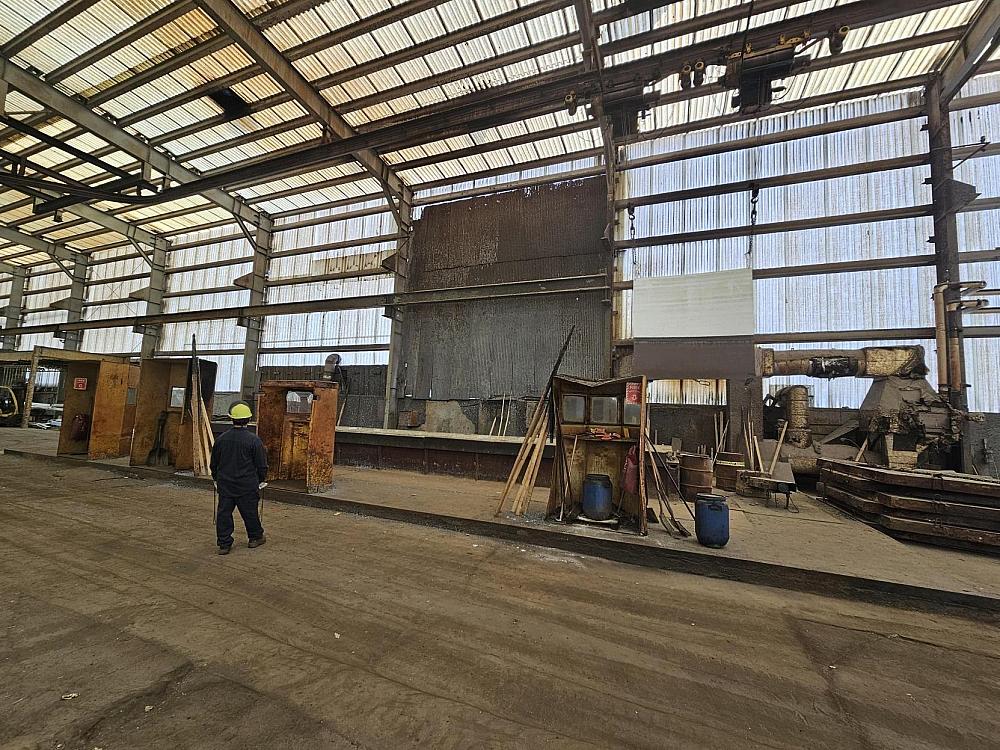
Once fluxing is complete, the item is taken back to the kettle to finish galvanizing.
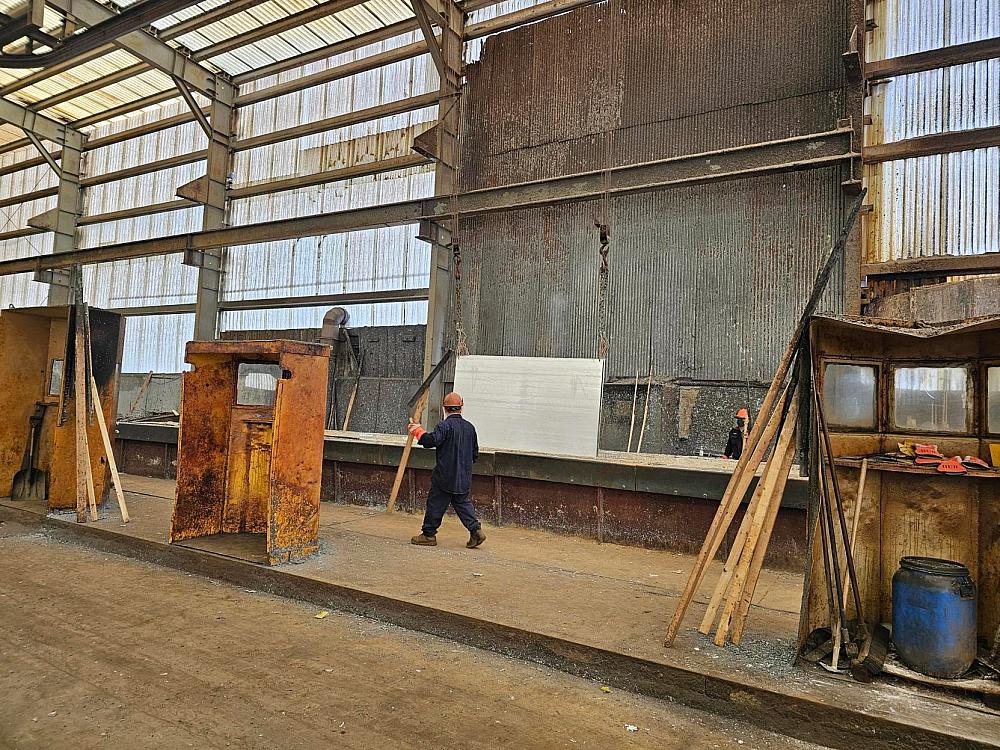
The bottom half of the item is submerged in the kettle, allowing the iron and zinc to react with one another, growing the galvanized coating.
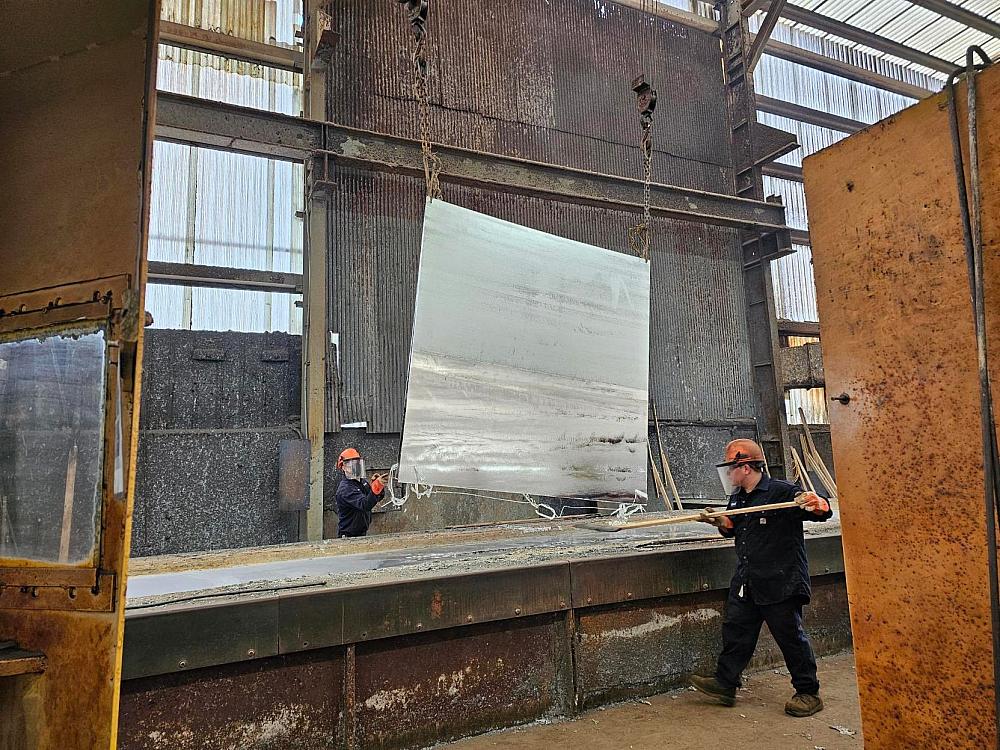
The item is now fully galvanized and continues on to the cooling and inspection area.
© 2025 American Galvanizers Association. The material provided herein has been developed to provide accurate and authoritative information about after-fabrication hot-dip galvanized steel. This material provides general information only and is not intended as a substitute for competent professional examination and verification as to suitability and applicability. The information provided herein is not intended as a representation or warranty on the part of the AGA. Anyone making use of this information assumes all liability arising from such use.