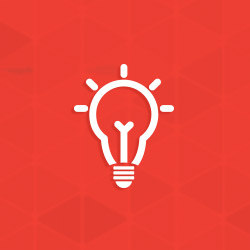
Overlapping Areas on Bridge Cross Frame Members
Can cross frame-to-gusset connections be seal welded for HDG?
When designing for hot-dip galvanizing, best practice is to avoid large overlapping surfaces welded together with narrow gaps. The resulting gap between two overlapping surfaces allows the collection of air, moisture, and pretreatment chemicals from the galvanizing process. When the resulting gap is less than 3/32 in. between the overlapping surfaces, molten zinc from the galvanizing kettle cannot enter the gap to coat the interior area. As a result, entrapped air and fluids are super-heated to the galvanizing temperature (820-850° F) with the rest of the fabrication. This causes a rapid expansion of the entrapped air and/or fluids, potentially leading to a blowout of the weld and harm to galvanizing plant personnel and equipment. Even if weld blowout is avoided, entrapped pretreatment chemicals can interact with the steel and moisture in the environment, causing oxides to seep from the joint in a condition known as a weeping weld. Weeping welds can be seen immediately after galvanizing, but can also occur after the steel are in service. Weeping welds are primarily a cosmetic concern and is addressed by cleaning any oxides or rust bleeding from the surface, but to prevent further weepage a caulking should be applied and maintained to seal the joint.
When overlapping surfaces cannot be avoided, fabrications require special considerations if hot-dip galvanizing to ensure structure integrity, galvanizing quality, and aesthetics near the overlapped area. The available methods are to:
- Ensure minimum 3/32 in. gap between plates such as when intermittent welding.
- Perform seal welding and provide sufficient vent holes or a length of unwelded area as required to prevent weld blowout based on steel thickness and size of overlap area, as detailed in ASTM A385 Tables 1 & 2 (summarized in Figure 1).
- Ensure sufficient venting when gap is less than 3/32 in. and apply caulking to seal the joint after galvanizing (may result in weeping weld as described above).
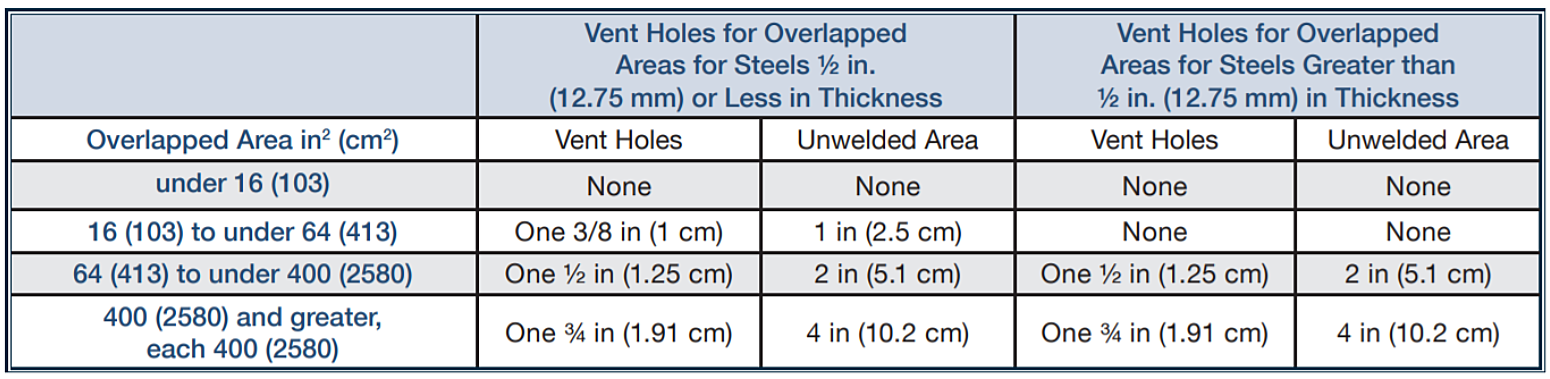
One example of a fabrication involving overlapping surfaces is the design of bridge cross frames which include an overlapping area at the connection between the angles and gusset plates (Figure 2).
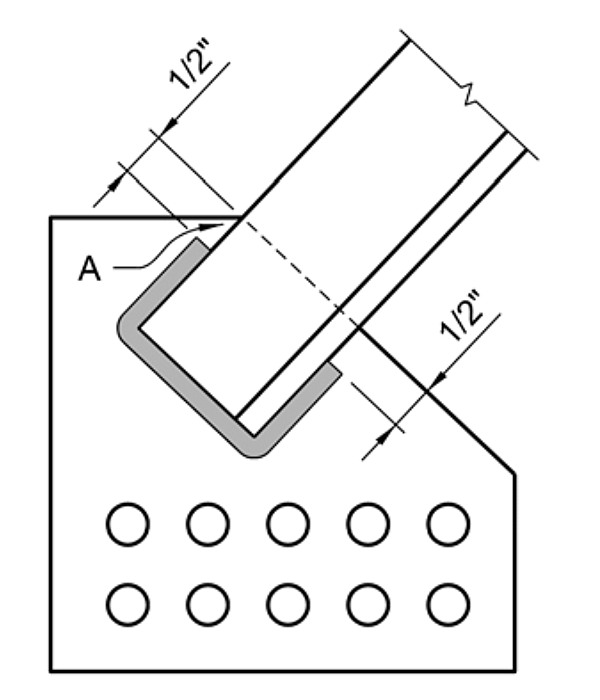
Design best practices involve starting and terminating the weld a short distance before the end of the joint (often specified as a distance equal to the weld size). Known as a weld holdback, this practice helps prevent weld quality issues related to arc blow if the weld were to be extended to the end or when wrap welding (Figure 3.)
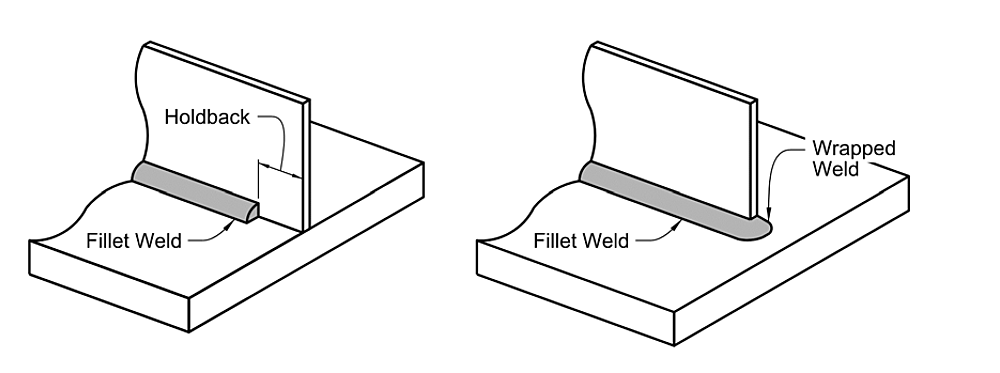
Depending on the steel thickness and size of overlap area, the specified holdback or otherwise unwelded lengths for this type of design are typically sufficient to prevent issues with weld blowout during galvanizing per ASTM A385 Tables 1 & 2. However, to avoid causing a weeping weld and rust bleeding after galvanizing, either a 3/32” gap must be provided between the overlapping surfaces to allow successful galvanizing of the interior, or seal welding can be investigated with caution.
According to Figure 1, overlapping areas less than 16 in2 (103 cm2) of steel less than ½ in. thick or overlapping areas less than 64 in2 (413 cm2) of steel greater than ½ in. thick can be seal welded without venting and galvanized without fear of weld blowout of the entrapped air/moisture upon galvanizing. However, any seal welding must be ensured or inspected to be free of pinholes or defects so that galvanizing pretreatment chemicals cannot enter the area. Performing a seal weld of suitable quality can be difficult or impossible to achieve depending on welding method, part geometry, accessibility of the welding equipment, and welder skill. Additionally, this practice conflicts with current bridge welding best practices. Therefore, any change to weld termination details should be discussed directly between the engineer, fabricator and galvanizer to discuss feasibility and known difficulties related to ensuring seal weld quality.
© 2025 American Galvanizers Association. The material provided herein has been developed to provide accurate and authoritative information about after-fabrication hot-dip galvanized steel. This material provides general information only and is not intended as a substitute for competent professional examination and verification as to suitability and applicability. The information provided herein is not intended as a representation or warranty on the part of the AGA. Anyone making use of this information assumes all liability arising from such use.