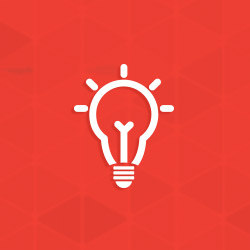
Methods Used to Coat Nails with Zinc
I've heard some types of galvanized nails specified for building/roofing projects can rust after only a few years in service. Which zinc-coated nails will provide the longest corrosion protection?
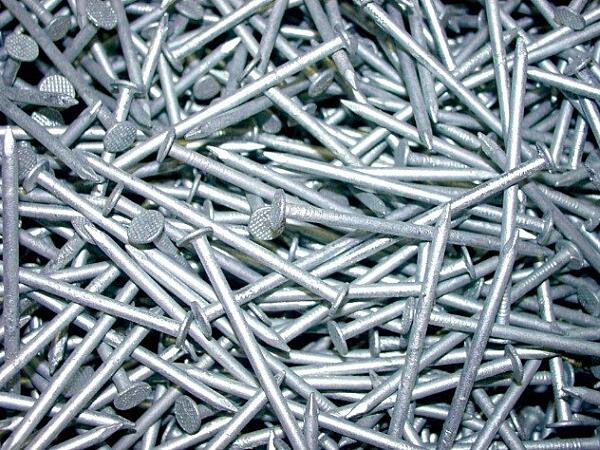
Often when purchasing zinc-coated nails, there is a misunderstanding about the difference between the methods that can produce a zinc coating on steel. There are four common methods used to coat nails with zinc: hot-dip galvanizing, tumbler hot-galvanizing, electroplating (electro-galvanizing), and mechanical zinc plating (peen-plating). Knowing the differences between these methods is valuable when assessing the corrosion protection required for a project. A summary of the properties of different methods for coating nails with zinc is presented in Table 1.
Table: Types of Zinc-Coated Nails | |||
Hot-Dip Galvanized | Electroplated/Electro-Galvanized/Zinc Plated | Mechanically Zinc Plated (Peen-Plating) | |
---|---|---|---|
Procedure | Clean steel with series of chemicals, dip in molten zinc bath, then spin to remove excess zinc | Clean steel, immerse in a zinc acid bath, and drive current through bath | Clean steel, flash coat with copper, then tumble in barrel with glass beads and zinc powder |
Zinc Coating Thickness | 1.7 mils minimum | 0.36 mils maximum | 1.5 mils effective zinc thickness (typical) 0.2 to 4.3 mils depending on tumbling time |
Coverage Consistency | 100% coverage | 100% coverage | Inconsistent thin coverage at edges and under nailhead |
Suitability | Outdoor and Indoor applications | Indoor applications | Indoor applications (outdoor sparingly) |
*Time to First Maintenance | 35-55+ years | 5-10+ years | 10-15+ years with inconsistent coating |
* Note: Minimum and maximum values derived from the Time to First Maintenance Chart for industrial and rural environments, respectively.
- Hot-dip galvanized nails have a coating which is uniform on all surfaces, providing excellent protection at the corners and edges. The hot-dip galvanizing process creates a metallurgical reaction between the zinc and the steel resulting in a series of zinc-iron alloy layers providing excellent abrasion resistance in the event the coating is scratched or damaged. Hot-dip galvanized nails are appropriate for any kind of mild-to-corrosive environment and provide long-term corrosion protection.
- Electroplated (electro-galvanized) nails have a very thin zinc coating and are therefore appropriate for interior applications. Electroplated nails are most commonly found at the local hardware store. When electroplated nails are used in exterior applications such as roofing projects, a 5-10 year coating lifetime can be typical as a result of the thin coating. After that, rust will be visible on the nail head.
- Mechanically plated nails can have a coating thickness similar to hot-dip galvanized nails, but the coating is thin near edges and underneath the nail head due to limitations of the mechanical plating process. Additionally, the coating is 25% less dense than a hot-dip galvanized coating and without the same abrasion resistance. Because the corrosion protection is related to the thinnest section of the coating, a 10-15 year coating lifetime can be typical for exterior applications.
Many times, electroplated and mechanically zinc-plated nails are sold as "galvanized, leading to the assumption that the nails are hot-dip galvanized. When purchasing nails for a housing/roofing project, ensure the labeling on the packaging says hot-dipped. If the label simply says galvanized, the package is not likely to contain hot-dip galvanized nails. Hot-dip galvanized nails are now readily available for use with pneumatic coil nail guns and can be purchased from suppliers such as Maze Nails and almost any housing/roofing nail distributor.
© 2025 American Galvanizers Association. The material provided herein has been developed to provide accurate and authoritative information about after-fabrication hot-dip galvanized steel. This material provides general information only and is not intended as a substitute for competent professional examination and verification as to suitability and applicability. The information provided herein is not intended as a representation or warranty on the part of the AGA. Anyone making use of this information assumes all liability arising from such use.