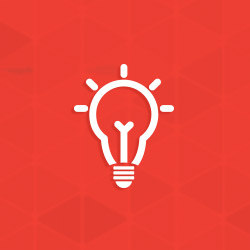
Meeting Minimum Thickness Requirements
What must galvanizers do when they cannot meet the minimum thickness requirements per ASTM specifications?
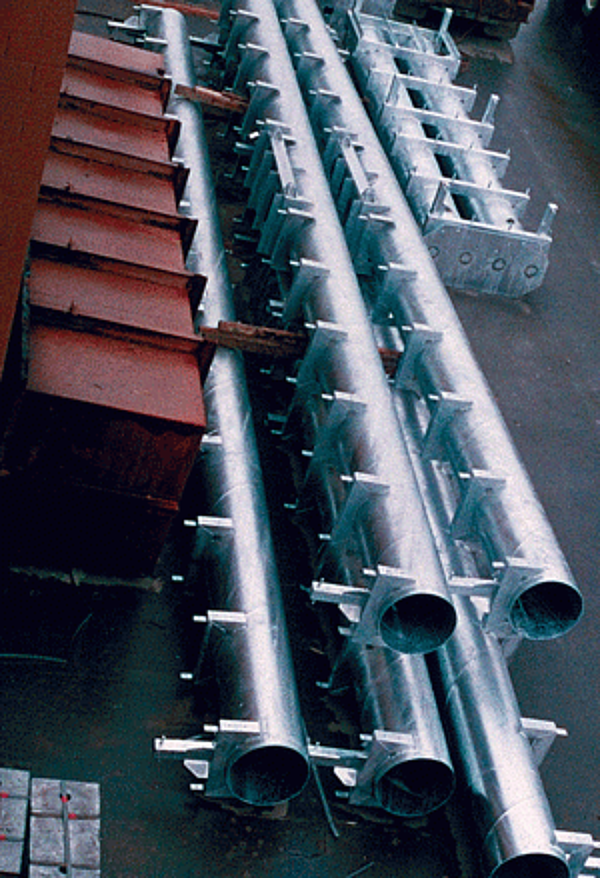
The requirements for coating thickness minimums in the specifications ASTM A123/A123M and ASTM A153/A153M have been developed over time to balance the needs for corrosion protection with how thick a galvanized coating is likely to grow given varying steel thickness and steel chemistry. In most instances, galvanizers can meet these requirements for coating thickness minimums; however, there are times when it is difficult or even impossible to meet these requirements.
Pipe, tube, and steels that have been aluminum-killed (rather than silicon-killed) or that have very low silicon levels are the types of steel most likely to present difficulties in meeting the necessary coating thickness minimums, even though they tend to fall in the recommended steel chemistry ranges of ASTM A385. In most cases, it is still possible to meet the minimum thickness requirements, but there are times when even after leaving the steel in the galvanizing kettle for excessively long times, meeting the minimum thickness requirements is not possible. This puts the galvanizer in a difficult situation since they are required to meet these requirements per the applicable ASTM specifications.
The most important thing galvanizers can do is educate their customers on the hot-dip galvanizing process. This is true not only for coating thickness minimums, but for all facets of the galvanizing process. The AGA has a number of free resources available for educating your customers. Another great place to educate your customers is in the purchase order confirmation and quotation form. In cases where it is very difficult to meet coating thickness minimums, discussing steel chemistry and coating thickness minimums in these two documents goes a long way to convincing your customer you are not trying to short change them on the zinc coating they are paying for. Both are also the perfect place to discuss alternative options (and who is to pay for these additional services) when normal galvanizing practices do not produce a galvanized coating thick enough to meet the minimum ASTM requirements.
Although not guaranteed, there are several techniques galvanizers can employ to achieve thicker galvanized coatings. Sweep blasting the steel prior to galvanizing roughens the steel surface, which thereby increases the total surface area on the steel. This increase in surface area allows for more locations for zinc crystals to grow from during the galvanizing process and increases the chances for a thicker coating to develop. An alternative method to sweep blasting that has sometimes been employed is to overpickle the steel in sulfuric acid (this method does not work in hydrochloric pickling baths). Overpickling the steel allows the acid to attack the steel surface and roughen it to some extent, which increases the surface area. Overpickling can have negative consequences, such as making the steel rougher or creating galvanized coatings that are rougher or that have uneven appearances. If overpickled too long, sulfuric acid can destroy the steel by excessive chemical attack.
In the end, it is the galvanizers responsibility to meet the coating thickness requirements of ASTM specifications, even in cases where the steel chemistry is a problem over which the galvanizer has no control. This is why it is important to educate your customer beforehand, or at least include provisions in your purchase order confirmation/quotation form to address who is responsible for paying for extra services, such as sweep blasting the steel, if necessary.
© 2025 American Galvanizers Association. The material provided herein has been developed to provide accurate and authoritative information about after-fabrication hot-dip galvanized steel. This material provides general information only and is not intended as a substitute for competent professional examination and verification as to suitability and applicability. The information provided herein is not intended as a representation or warranty on the part of the AGA. Anyone making use of this information assumes all liability arising from such use.