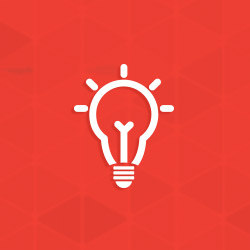
Aluminum Killed Steel and Thinner HDG Coatings
Why do aluminum-killed steels develop a thinner hot-dip galvanized coating than silicon killed-steels?
Silicon can be the primary catalyst in steel that drives the metallurgical reaction that happens during the hot-dip galvanizing process. Various studies have looked at how varying levels of silicon in steel affect the galvanized coating. These studies have shown that varying the silicon level in the steel can have a profound effect on the thickness of the galvanized coating that develops on the steel.
Different galvanized coating thicknesses will not only provide varying levels of corrosion protection (thicker coatings provide longer corrosion protection than thinner coatings), but they can also affect the brittleness of the galvanized coating. Galvanized coatings thicker than 10 mils can be more brittle and can thus have a higher likelihood of flaking off the steel if the steel is handled roughly or impacted, such as when driving piles into the ground.
Silicon is added to iron during the steel making process and acts as a deoxidizer. It prevents oxygen in the air from reacting with carbon that is added to the iron. (Carbon is added to iron to strengthen the steel.) Another deoxidizer that is commonly used in the steel-making process is aluminum. Aluminum does not act as a catalyst in the galvanizing reaction like silicon does.A recent study conducted by Corbec Inc. looked at the difference in galvanized coating thicknesses on silicon and aluminum-killed steels. The study showed it can be difficult to meet the coating thickness requirements of various galvanizing specifications when aluminum-killed steels are galvanized. This problem is exacerbated when the galvanizing kettle has nickel (nickel can reduce the coating thickness on reactive steel with silicon levels less than 0.20%), which tends to develop excessively thick galvanized coatings.
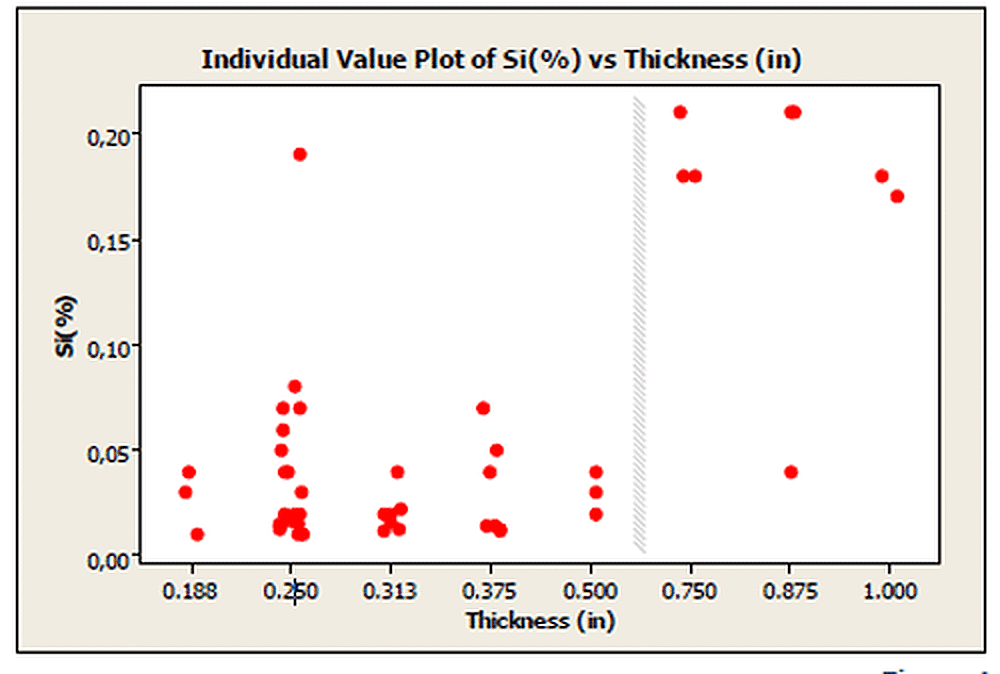
This study by Corbec was critical to recent changes made to ASTM A123/A123M for the two different material categories, Structural Shapes and Plate and Strip and Bar, for steel thicknesses ranging from >3/16 inch to <1/4 inch. The changes reduced the minimum coating thickness requirements from 85 microns (3.4 mils) to 75 microns (3.0 mils). The need for the change in coating thickness requirements is demonstrated in Figure 1. This chart shows for plain carbon steel thinner than 1/2 inch, the silicon level tends to be low (often less than 0.05%). For these types of steels, aluminum is often used as the primary oxidizer. Because aluminum is the primary oxidizer in these steels, the silicon level will be low in these steels and the galvanized coating thickness tends to be thinner as well; so low in fact it is often difficult or impossible to meet the previous coating thickness requirement of 85 microns (3.4 mils).
In summary, aluminum like silicon acts as a deoxidizer in the steel making process. In the galvanizing process, the primary difference between these deoxidizers is aluminum does not act as a catalyst for the metallurgical reaction like silicon does. This means aluminum-killed steels tend to have thinner galvanized coatings than silicon-killed steels. For more information on this topic or studies on how silicon and aluminum affect the galvanized coating thickness, please contact the AGA Technical Department at [email protected]
© 2025 American Galvanizers Association. The material provided herein has been developed to provide accurate and authoritative information about after-fabrication hot-dip galvanized steel. This material provides general information only and is not intended as a substitute for competent professional examination and verification as to suitability and applicability. The information provided herein is not intended as a representation or warranty on the part of the AGA. Anyone making use of this information assumes all liability arising from such use.