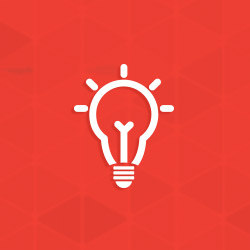
High Temperature Galvanizing
What do I tell a customer who wants High Temperature Galvanizing?
High temperature galvanizing (also called delta galvanizing) is a hot-dip coating process where steel is dipped in a zinc bath at 1040-1165°F (560-630°C) to form a coating comprised of a thin gamma layer with a compact delta layer on top. As a result, a very hard, rough, and thin coating is produced with similar properties to a traditional hot-dip galvanized coating. Depending on the customers specification, high temperature galvanizing can also be controlled to produce coating thicknesses ranging from 1-3.1mils (25-80?m) in accordance with ISO 1461, but not meeting ASTM A123 or A153 requirements.
Although high-temperature galvanizing is not a common coating process seen in North America, in Europe high temperature galvanizing is typically specified for sheet products in the automotive industry or for certain hardware items where both superior corrosion protection and precise fit-up (controlled coating growth) is required. Often times, the reason a customer may wish to utilize high temperature galvanizing for their project is that they have concerns over fit-up between parts, ease of painting over HDG, and/or abrasion resistance. So what can you tell your customer that has heard high-temperature galvanizing can provide these benefits, and requests you provide this service? First of all, it is not possible to simply raise the zinc bath temperature. Due to the high reactivity between molten zinc and steel at these temperatures, a ceramic-lined steel kettle is used. Additionally, bath alloying additions which are helpful at certain concentrations at standard galvanizing temperatures may become detrimental or at best ineffective at higher bath temperatures.
Instead, it may be possible the customer is unaware of how traditional hot-dip galvanizing can be used to achieve the same benefits. You can educate the customer regarding each of their concerns:
Fit-up of Parts
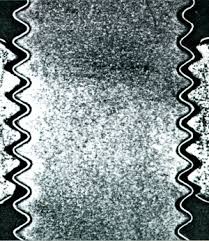
The increased thickness of the coating, although minimal, can affect final match-up of parts, along with zinc drips or runs. It is a team effort between the specifier, fabricator, and galvanizer to ensure parts fit correctly after galvanizing. The designer and fabricator must follow recommended design and fabrication practices, while the galvanizer can improve zinc drainage and potentially control coating overgrowth. If the customer has concerns over the fit up of fasteners/hardware, size of clearance holes, or clogging of holes, then it is important to inform your customer of the practices employed to mitigate such issues:
- Overtap nuts and interior threads per the recommendations within Table 5 of ASTM A563, Specification for Carbon and Alloy Steel Nuts except for nuts/interior threads utilized for bearing-type connections
- Oversize clearance holes for slip-critical connections by 1/16 inch
- Oversize clearance holes for connections that require greater clearance for alignment per Section J3.1, Table J3.3 of AISCs LRFD manual (excludes bearing-type connections)
- Maintain a radial clearance of at last 1/16 inch for all moving parts such as hinges
- Avoid specifying drilled holes or mesh sizes under ½ inch in diameter
- Increase zinc drainage with lead/bismuth or aluminum in recommended bath concentrations
- Utilize common procedures which have the potential to control coating overgrowth of reactive steels (nickel additions to the bath, blast cleaning prior to galvanizing, reduce dip time)
Paintability / Coating Too Smooth
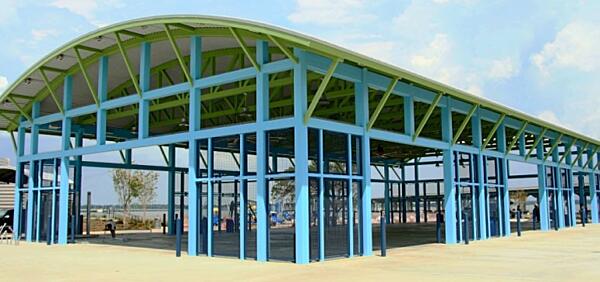
There is a misconception that because high temperature galvanized coatings are rough in texture, they are easier to paint than traditional hot-dip galvanized coatings. Hot-dip galvanized surfaces are successfully prepared for painting per ASTM D6386, Practice for Preparation of Zinc (Hot-Dip Galvanized) Coated Iron and Steel Product and Hardware Surfaces for painting, or for powder coating per ASTM D7803, Practice for Preparation of Zinc and Hardware Surfaces for Powder Coating. Additionally, there are instructional guides and videos available on the AGA website regarding this topic.
Occasionally, a customer may require a rough finish for other types of project requirements. Other than hot-dip galvanizing reactive steel, a roughened surface can be obtained by sweep blasting, or by application of a wash/etch primer or phosphate treatment. For slip-critical connections where an increased slip resistance is required, explain the benefits of applying zinc silicate paints on faying surfaces or describe the lock-up phenomenon if some initial slippage of the joint is acceptable.
Abrasion Resistance of Coating Surface
The delta layer is a highly abrasion resistant surface layer of the high-temperature galvanized coating, leading to the misconception that high-temperature galvanizing provides a coating of greater abrasion resistance than traditional hot-dip galvanizing. Although the hardness of the delta layer certainly provides exceptional abrasion resistance, this layer is also present within traditional hot-dip galvanized coatings along with a similarly abrasion resistant Zeta layer. In addition, the outer and more ductile Eta layer (pure zinc layer) provides impact resistance. The combined benefits of these layers make damaging the coating very difficult during handling, transportation, installation, or even in-service.
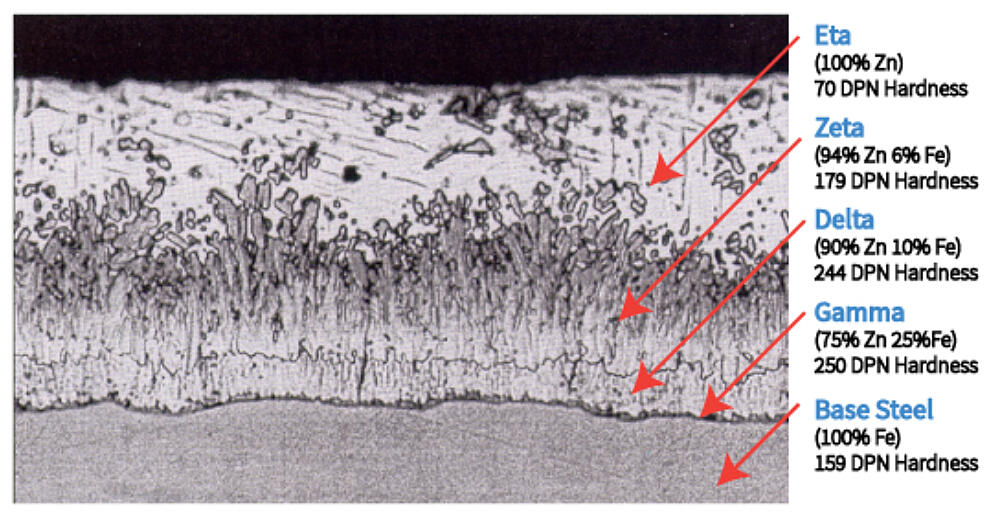
© 2025 American Galvanizers Association. The material provided herein has been developed to provide accurate and authoritative information about after-fabrication hot-dip galvanized steel. This material provides general information only and is not intended as a substitute for competent professional examination and verification as to suitability and applicability. The information provided herein is not intended as a representation or warranty on the part of the AGA. Anyone making use of this information assumes all liability arising from such use.