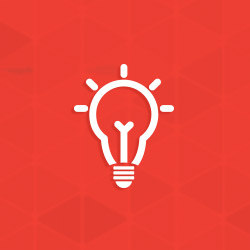
Handling Markings on Hot-Dip Galvanized Coatings
I recently received a product with markings that appear to be caused by the handling of the steel during the galvanizing process. What causes these surface defects and are they acceptable according to ASTM A123?
A hot-dip galvanized coating could have any number of surface defects that can lower the long-term corrosion performance of the product. Some surface defects can be caused by handling the steel during the process. Surface defects may or may not create a bare spot, the coating thickness is zero. According to ASTM A123, bare spots are not acceptable on the surface of a hot-dip galvanized steel product.
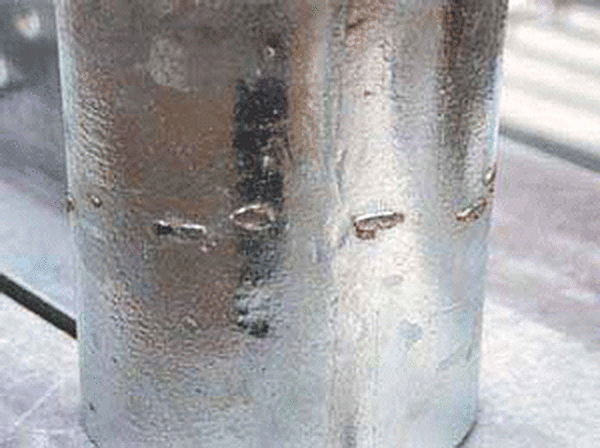
One surface defect can be caused when steel is hung on lifting racks using chains or wires, and transported around the galvanizing plant. Chain or wire marks, like those seen in Figure 1, can sometimes be avoided by proper hanging and transporting techniques. However, some products must be hung in a manner that will create chain or wire marks in order to be galvanized.
Another surface defect caused by handling steel during the galvanizing process is known as touch marks, as seen in Figure 2. Touch marks are either partially coated or uncoated spots on the surface of the galvanized steel and are created when products come in contact with each other during the galvanizing process. This commonly occurs when numerous small products are hung on the same lifting fixture. When you hang products too closely, it creates a higher chance that the products will touch each other when they are placed in the galvanizing kettle. Touch marks can sometimes be avoided by increasing the horizontal and/or vertical spacing between products. To do this, hang fewer products on the same lifting fixture or vary the heights at which the products are hung.
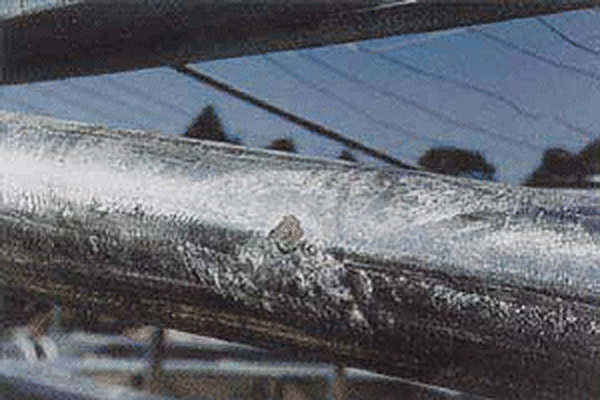
Any surface defect that creates a bare spot that is below the acceptable size criteria for a repairable area and that is properly repaired by the galvanizer is not cause for rejection. According to ASTM A123, the definition of a repairable area is the total area of bare spots on a product must not exceed 0.5% of the accessible surface area to be coated, or must not exceed 36in2 per short ton (256cm2 per metric ton), whichever is less. This means any products with bare spots that meet this definition must be repaired by the galvanizer in accordance with ASTM A780. However, any products with bare spots that exceed this definition must be rejected. They can be stripped and re-galvanized. It is the galvanizers responsibility to properly handle products during the galvanizing process to minimize surface defects, and it necessary, repair any bare spots that may occur.
© 2025 American Galvanizers Association. The material provided herein has been developed to provide accurate and authoritative information about after-fabrication hot-dip galvanized steel. This material provides general information only and is not intended as a substitute for competent professional examination and verification as to suitability and applicability. The information provided herein is not intended as a representation or warranty on the part of the AGA. Anyone making use of this information assumes all liability arising from such use.