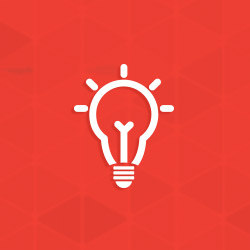
Galvanized vs. Epoxy-Coated Rebar
Area contractors have recently been using epoxy-coated rebar in many newly-constructed bridges. I know HDG is a superior coating, but in what areas does it really outshine epoxy?
Hot-dip galvanized steels superior corrosion protection can easily be recognized when a simple evaluation of field performance is reviewed. HDG reinforcement has been used since the 1950s. One of the earliest examples of this is the Longbird Bridge in Bermuda, constructed in 1953. Bermuda is classified as a marine environment, which is subject to high chlorides levels and, consequently, elevated corrosion rates for steel materials. A 1978 inspection of this bridge by the Construction Technology Labs found that chloride levels in the concrete reached up to 7.3 lbs/yd3 (4.3 kg/m3).
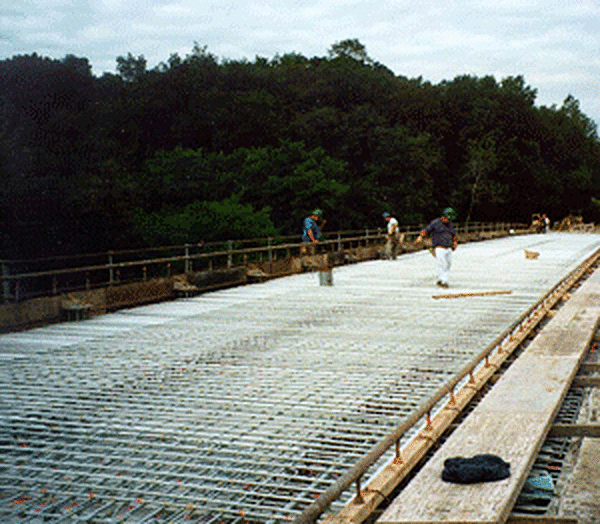
High chloride levels accelerate corrosion rates by locally lowering the pH at a corrosion site. A cross-sectional chloride analysis of the concrete section pointed that the cement was probably made up with seawater, introducing high levels of chlorides, immediately contacting the HDG rebar. Nevertheless, the galvanized coating shows only slight signs of corrosion (98% intact) even after almost 50 years in service under aggressive environmental conditions. This outstanding performance won the respect of several state DOTs which now specify galvanized steel extensively, including both the New York State Thruway Authority (NYSTA) and the Pennsylvania DOT.
By the 1960s, the NYSTA started to see the deleterious effect of deicing the road with salts. The freeze-thaw cycles, coupled with a marine environment and additional chlorides from salting, added up to harsh environment for steel materials. The corrosion products of steel rebar can increase the encased volume by 10%, in many cases rupturing the surface of the concrete, causing large spalling in sections of concrete bridges. Something was needed to protect the embedded steel reinforcement. In the 1970s, a solution appeared on the market.
The concept of a barrier coating was successfully being used by the underground pipe industry, and, following suit, the NYSTA began coating rebar with epoxy by the early 1980s. After ten years of extensive epoxy use, the NYSTA again began a search for a new coating type, after discovering the epoxy-coated rebar had many flaws:
- Pits or discontinuities in the epoxy film can lead to immediate corrosion at the uncoated site
- The coating lacks abrasion resistance and thus is easily damaged in transport to the job site and installation.
A life-cycle cost analysis was performed by the NYSTA to compare epoxy to HDG rebar and other coating types in lieu of the poor epoxy-coated performance. Initially, the cost of HDG rebar is slightly greater than epoxy, based on a per-pound basis, but the amount of epoxy-coated rebar needed for constructions is far greater than that of HDG rebar, due to the inferior bond strength of epoxy. This brings HDG to an extremely competitive position, financially. On a life-cycle cost analysis, the maintenance-free service life of HDG rebar is unmatched.
The Pennsylvania DOT has specified galvanized rebar for decades and one of the examples of this is the Athens Bridge built in 1973. Inspected eight years following its construction to ensure the HDG rebar was providing the expected level of performance, cores were drilled to evaluate chloride levels; those found ranged from 1.8 to 7.9 lbs/yd3, at the maximum value well-exceeding the threshold for active corrosion to occur on bare steel. However, the galvanized rebar inspected showed over 15 mils of coating with no signs of active corrosion present. The bridge was inspected again in 1991 and 2001, where, again, the rebar showed no active signs of corrosion. These results point to an additional 40+ years of service.
The case histories described here are only a few of the many examples of the superior performance of galvanized rebar. It is estimated that over 500 bridges use HDG as the corrosion protection system. Currently, inspections being done on bridges containing galvanized rebar all report excellent performance, most bridges with maintenance-free service estimates of at least 75 years.
Learn more about galvanized rebar and earn continuing education credits by requesting an in-person seminar or taking our online rebar seminar.
© 2025 American Galvanizers Association. The material provided herein has been developed to provide accurate and authoritative information about after-fabrication hot-dip galvanized steel. This material provides general information only and is not intended as a substitute for competent professional examination and verification as to suitability and applicability. The information provided herein is not intended as a representation or warranty on the part of the AGA. Anyone making use of this information assumes all liability arising from such use.