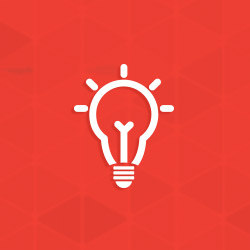
Cracking due to High Residual Stress
Who is responsible for a customers parts that have cracked due to high residual stress?
Prior to hot-dip galvanizing, complex design and standard fabrication methods can result in areas of high residual stress. Afterward, these structures are dipped at an angle into the galvanizing kettle, resulting in uneven and rapid heating of steel to around 830 F. If efforts are not made to relieve or control areas of high residual stress, then the additional thermal stress from the hot-dip galvanizing process can occasionally result in cracking at the most highly stressed area, and minor bath elements can assist in growth of the cracks.
Although the good news is that these structures and the surrounding coating can be repaired, this information is often not enough to address the customers concerns. What can be frustrating to the customer is they may have successfully galvanized the same structure design for many years and only now encountered a problem. This is because this type of cracking issue does not happen all of the time, but only occasionally when the conditions are just right.
Lets take a look at some contributing factors that, when combined, often result in areas of high residual stress, even if correct and proper design, fabrication, and galvanizing methods have been followed.
Identifying Areas of High Residual Stress
Keep in mind, there are often several variables involved which can contribute to the cracking issue. Addressing only one variable may eliminate the issue, or it may be necessary to address more than one variable.
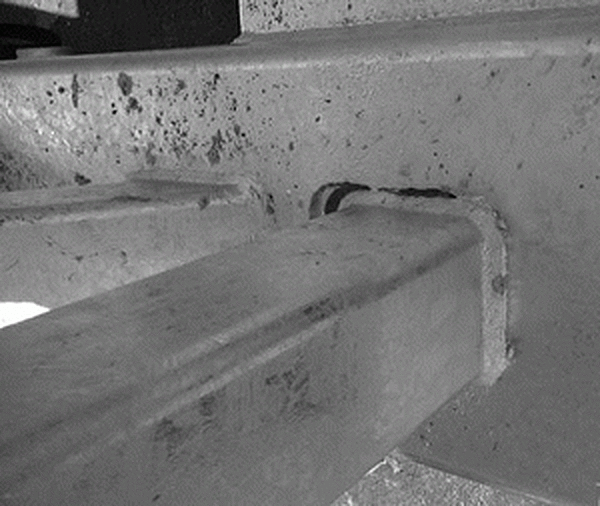
Cut/Welded Areas and the Heat Affected Zone
The stresses from welding are from the weld metal itself, as it is typically harder and stronger than the base metal. The welding process also increases the hardness and reduces the ductility of steel in the area around the weld known as the heat-affected zone (HAZ). As a result, a highly stressed location is created and is more susceptible to brittle fracture.
Thermal cutting techniques also introduce a significant amount of energy in the steel, and can alter the microstructure and properties of the steel within the heat affected zone (HAZ). As a result, thermally cut steel can be extremely sensitive to residual stresses, especially if the surface of the cut remains rough.
Heavy Cold Working
Cold working can include bending, punching, or shearing the steel. If the stresses from these cold working practices are not relieved prior to galvanizing, they become points of high residual stress during the galvanizing process.
Framed Areas & Welding Steel of Varying Thickness
When two steels of different thicknesses are assembled and brought up to galvanizing temperature, the thinner steel heats up and expands more quickly than the thicker steel. If the thicker steel restrains the thinner steel from expanding freely, or if any component is constrained by framing, this will add even more stress to an already highly-stressed area such as the joining weld.
Minimizing Residual Stress
The galvanizer can attempt to minimize additional thermal stress by minimizing immersion time in the kettle where possible and perform air cooling of the parts. However, minimizing areas of high residual stress, typically through changes in design or fabrication methods, have the greatest impact on minimizing or eliminating the potential for cracking when the inevitable differing rates of heating and cooling occur.
Designs can be modified to better allow for thermal expansion of the steel, especially near corners and for assemblies containing steel of varying thickness. Additionally, heavy cold working can be avoided to reduce stress. Cutting and welding practices (methods, temperature, the roughness of cuts, heat inputs) can also be adjusted to minimize stress in the HAZ. Where possible, use balanced welding techniques and avoid a welding sequence that results in forcing or clamping materials together to complete the weld. Alternatively, assemble separate parts after HDG by bolting or welding.
Where areas of high residual stress cannot be avoided, perform a thermal treatment of susceptible areas before HDG to relieve stress. One such stress-relieving procedure can be found in Paragraph 6.3 of ASTM A143, Standard Practice for Safeguarding Against Embrittlement of Hot-Dip Galvanized Structural Steel Products and Procedure for Detecting Embrittlement.
Responsibility for Cracking due to High Residual Stress
It can be difficult to determine responsibility for remediation or rework after cracking due to high residual stress because it is typically a complex issue with many variables. Regardless of design and fabrication methods used, the temperatures involved in the hot-dip galvanizing process do contribute to the issue. Often times the responsibility for cracking is shared between the fabricator, owner, and galvanizer but not always. Regardless, there are several steps galvanizers can take to protect themselves from unnecessary responsibility.
The galvanizer can inspect all products before hot-dip galvanizing, and flag susceptible fabrications to the customer so they are aware of any potential risks upon running the material. Then afterward, the material should be checked again after galvanizing to determine the presence of any cracks. Should a crack be discovered, the customer will greatly appreciate the time, effort, and money saved by informing them of the issue at the galvanizing plant upfront as opposed to discovering cracks on their own after delivery or erection at the job site.
© 2025 American Galvanizers Association. The material provided herein has been developed to provide accurate and authoritative information about after-fabrication hot-dip galvanized steel. This material provides general information only and is not intended as a substitute for competent professional examination and verification as to suitability and applicability. The information provided herein is not intended as a representation or warranty on the part of the AGA. Anyone making use of this information assumes all liability arising from such use.