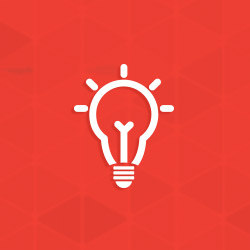
Corner Cracking of Square and Rectangular HSS
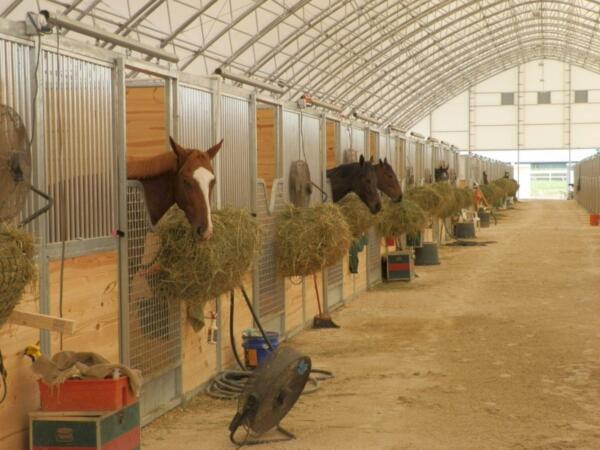
How Is Corner Cracking of Square and Rectangular HSS Prevented?
Cold formed Hollow Structural Sections (HSS) are commonly hot-dip galvanized for a variety of projects and industries because full immersion in the galvanizing kettle allows full coverage including interior protection from corrosion.
Anytime cold worked steels such as HSS products are to be hot-dip galvanized, the specification ASTM A143 Practice for Safeguarding Against Embrittlement of Hot-Dip Galvanized Structural Steel Products and Procedure for Detecting Embrittlement should be consulted for best practices to avoid severe cold working which could increase the potential for strain-age embrittlement. In the manufacturing of HSS, cold working occurs when a flat steel coil is deformed plastically into the final desired shape. To avoid strain-age embrittlement, ASTM A143 states it is best to keep bend radii as large as possible when forming and bending, but preferably a minimum of three times the steel thickness (3 x T). ASTM A143 does not explicitly specify whether the the minimum bending radius of 3 x T applies to the inside or outside radius, but relevant industry research confirms this recommendation refers to the inside radius.
The North American standard for square and rectangular HSS (ASTM A500 Specification for Cold-Formed Welded and Seamless Carbon Steel Structural Tubing in Rounds and Shapes) requires the maximum outside bending radius be 3 x T, where T is the wall thickness of the as-produced HSS. This requirement results in an inside maximum radius of 3T – T = 2T (Figure 1) which is below the recommended bend radius provided in ASTM A143.
Square and rectangular A500 HSS members are galvanized successfully all the time, but such tight corner radii can occasionally lead to cracking in the corners (the most highly stressed areas) upon galvanizing. The potential increases as wall thickness increases or when other internal stresses are present from the welding or framing of the parts (Figure 2).
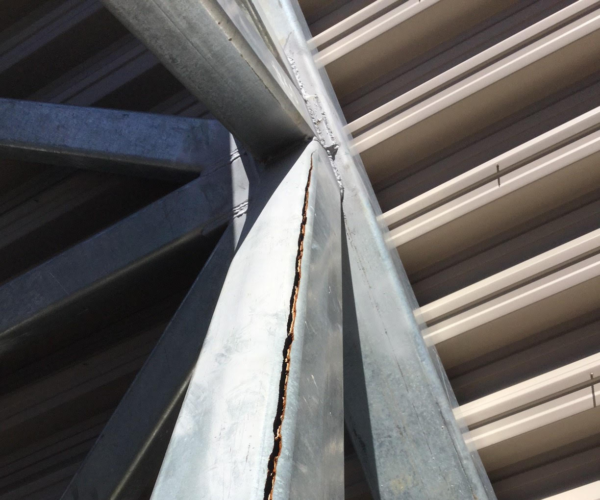
When pre-galvanizing measures are considered, the chance for embrittlement can be greatly reduced1. HSS manufacturers are aware of the issues with tight corner radii and can attempt to establish a minimum boundary when specified for galvanizing. Decreasing tolerances for local surface imperfections (such as gouges or grooves) and grinding the inside corners at the member ends are two additional methods found to be effective.1 Though the corner bending radii is the most important factor when considering potential for cracking, HSS members can also be heat-treated to relieve the stresses prior to galvanizing2 in accordance with ASTM A143 procedures and then air cooled. Once at the galvanizing plant, additional best practices include increased inspection of square and rectangular HSS corners immediately after galvanizing to help identify a potential cracking issue.
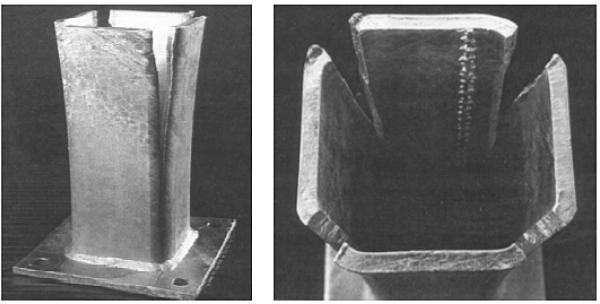
Another example of a cracking phenomenon related to HSS products is shown in Figure 3. This phenomenon usually occurs when one end of a tube is connected to a baseplate, and the entire tube tries to expand while immersed in the galvanizing bath. The baseplate constrains movement on one end of the tube, and stresses flow up the structure and away from the confined stress at the baseplate.
The result is high residual and thermal stresses in the transverse direction that cause the other end to explode and crack at the most highly stressed area(s). In square and rectangular HSS, the cracking location would be observed at the corners instead of the weld seam.
In 2013, a new standard for HSS, ASTM A1085 Specification for Cold-Formed Welded Carbon Steel Hollow Structural Sections (HSS), was developed to enhance the performance of HSS and make designing with HSS easier and more efficient for structural engineers. ASTM A1085 has increased the lower bound bend radius to address corner cracking during galvanizing so it is much less frequent and the need for heat treatment is less common. Although the specification of A500 is still very abundant, the design and material improvements within A1085 are leading to increased availability and use in seismic, bridge, and transportation structure applications. More information about A500 and A1085 are available from the Steel Tube Institute (STI).
Despite changes to HSS standards, there is still a small potential for cracking on corners of HSS tubing due to the tight corner radiuses used. Corner areas should be visually inspected after galvanizing to detect the presence of any cracks. Cracking occurs at the tubing ends so the affected area is often accessible for repair. Following repair of the HSS member, the galvanized coating can be repaired per ASTM A780 Practice for Repair of Damaged and Uncoated Areas of Hot-Dip Galvanized Coatings.
Footnotes:
- Sun, M., Packer, J.A. Hot-dip galvanizing of cold-formed steel hollow sections: a state-of-the-art review. Front. Struct. Civ. Eng. 13, 49–65 (2019). https://doi.org/10.1007/s11709-017-0448-0
- Kinstler, Thomas J. (GalvaScience LLC). Current Knowledge of the Cracking of Steels During Galvanizing. American Institute of Steel Construction Report No. 3213 (2005).
© 2025 American Galvanizers Association. The material provided herein has been developed to provide accurate and authoritative information about after-fabrication hot-dip galvanized steel. This material provides general information only and is not intended as a substitute for competent professional examination and verification as to suitability and applicability. The information provided herein is not intended as a representation or warranty on the part of the AGA. Anyone making use of this information assumes all liability arising from such use.