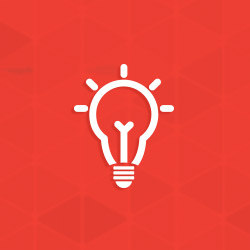
Base Metal Reading (BMR) & HDG
Does the Base Metal Reading (BMR) affect HDG coating thickness readings?
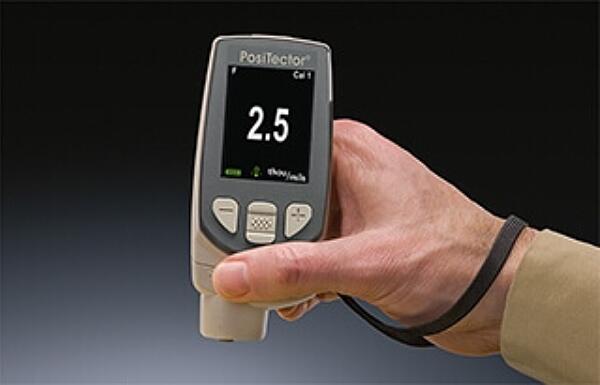
Hot-dip galvanized (HDG) coating thickness can be measured by four separate techniques: magnetic thickness gauge, stripping method, weighing before and after galvanizing, and optical microscopy. However, the most popular measurement technique for HDG coating thickness is the magnetic thickness gauge. The gauge works by measuring either the magnetic attraction between a magnet and a magnetic material such as steel or by measuring the magnetic flux change through a coating to a magnetic steel substrate. The methodology for using this type of gauge is contained in ASTM E376, Measuring Coating Thickness by Magnetic-Field or Eddy-Current (Electromagnetic) Testing Methods. Although quite accurate, these types of gauges should be calibrated and verified often to retain their accuracy and repeatability.
There are three types of magnetic gauges, and all can be used quite easily in the galvanizing facility or the field: a mechanical pencil-style gauge, a mechanical dial type or banana gauge, or an electronic/digital gauge (Figure 1). There are pros and cons for the use of each gauge type, but all are sensitive to effects from the roughness, mass, metallurgy, and other properties of the base steel.
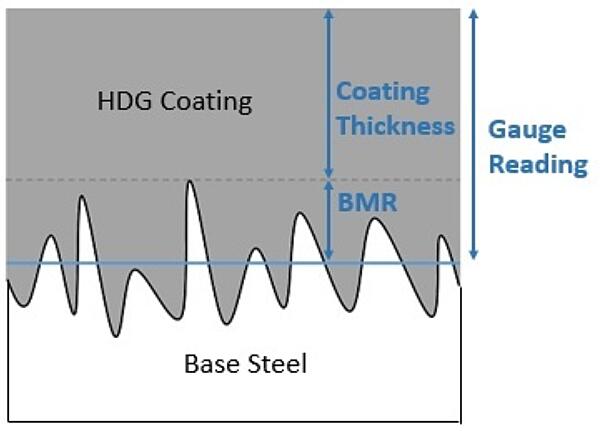
Magnetic thickness gauges measure from a point between the peaks and valleys of the surface roughness (as determined by the base metal properties), and up to the top of the galvanized coating. However, coating thickness is defined as the thickness of coating above any surface roughness. As demonstrated in Figure 2, the difference in these two distances is called the base metal reading, or BMR. If left unmeasured, it can result in overstating the coating thickness.
ASTM E376 Paragraph 4.4 states interferences such as composition, surface roughness, and other properties of the base metal affect the measurement accuracy, and Paragraph 5.7 states any surface roughness can cause gauges to read high. Referenced within E376 is the specification ASTM D7091, Practice for Nondestructive Measurement of Dry Film Thickness of Nonmagnetic Coatings Applied to Ferrous Metals and Nonmagnetic, Nonconductive Coatings Applied to Non-Ferrous Metals. ASTM D7091 defines the term base metal reading and its significance in Section 3, and provides a method to account for the BMR within Section 7.5. As a result, experienced inspectors familiar with the effects of BMR on coating thickness measurements may ask whether BMRs are being obtained by your QA/QC personnel between pickling and the galvanizing kettle.
Practically speaking, in a galvanizing production setting, it can be unsafe, impractical, or at least very difficult to manage the measuring of BMRs for every test article to be inspected for coating thickness. For customers requesting coating thickness measurements to be calibrated off the BMR, there are a couple of considerations which are helpful to consider when determining whether minimum average coating thickness has been achieved.
First, the steel typically sent for hot-dip galvanizing is relatively smooth and will likely have a very low roughness value unless it has been blast cleaned prior to arrival at the plant. Second, for HDG coatings it is common to obtain 5-6 mils of coating thickness or more, even though the minimum average coating thickness outlined within ASTM A123 can range from 1.4 3.9 mils depending on material thickness and category.
In an example, 3.9 mils minimum average coating thickness is required for a 1/4 structural beam per A123, but 5.2 mils average coating thickness is measured upon inspection. In this instance, the accuracy of electronic gauges, ±(0.1 mils + 1-3%), and a potential BMR value of 0-1 mil could result in a combined error of ~1.256 mils. Since the maximum error from these sources is within the 1.3 mils additional coating thickness that was achieved, it can be argued that the requirement for coating thickness has been met.
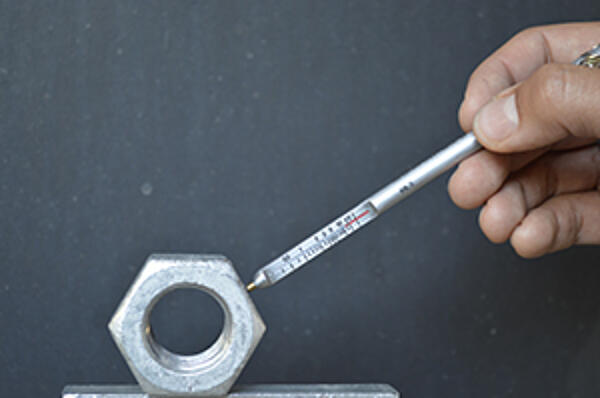
Where it is necessary to compensate for the BMR to determine whether the minimum average coating thickness requirement has been achieved, the following guidelines can be utilized to come to an agreement with the customer:
- Mechanical Gauges (pencil and dial type): with a verified gauge, measure an uncoated and representative sample part (prior to galvanizing) at a minimum of ten arbitrarily spaced locations to obtain a representative average value (BMR), and then subtract the BMR from all galvanized coating thickness readings.
- Electronic Gauges: perform a verification of calibration (zero the gauge) on an uncoated and representative sample part (prior to galvanizing), then adjust the reading if necessary. It is also possible to first verify the gauge accuracy using traceable standards supplied by the manufacturer, and then perform the same instructions for mechanical gauges.
- If the material contains heavy surface oxides (rust) at the time of reading, or if sulfuric pickling is utilized, it should be noted the presence of rust will affect the reading, and overpickling in sulfuric acid (while uncommon) can affect surface roughness and possibly the BMR value.
- A duplex system can present further challenges in obtaining accurate thickness measurements due to the prepared surface of the galvanizing and the presence of two coating systems. The use of a specialized duplex coating thickness gauge is recommended to obtain accurate coating thickness measurements.
© 2025 American Galvanizers Association. The material provided herein has been developed to provide accurate and authoritative information about after-fabrication hot-dip galvanized steel. This material provides general information only and is not intended as a substitute for competent professional examination and verification as to suitability and applicability. The information provided herein is not intended as a representation or warranty on the part of the AGA. Anyone making use of this information assumes all liability arising from such use.