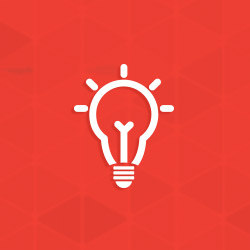
ASTM F2329 vs. ASTM A153
What is necessary to certify to the galvanizing standard ASTM F2329 (2015 revision)?
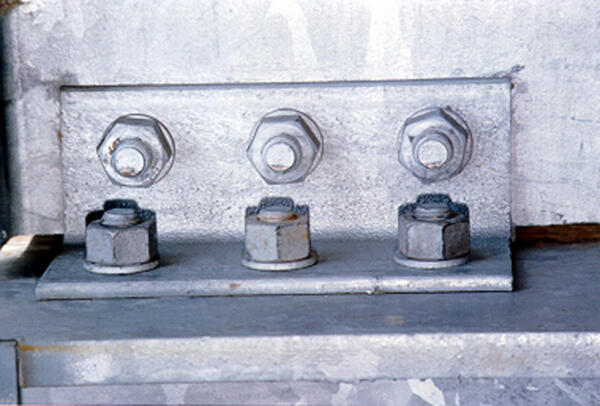
ASTM A153 and ASTM F2329 are similar specifications for galvanizing hardware centrifuged after galvanizing, although F2329 does not cover galvanizing nails or rivets. Galvanizing fasteners in accordance with A153, will usually meet or exceed the requirements of F2329, because F2329 defers to A153 in many sections. However, there are some differences between the specifications the galvanizer and customer should be aware of to determine whether it is practical for a particular galvanizing plant to meet the customers specific requirements under the latest F2329 revision (2015).
The major differences between the two specifications, described below, include topics related to sampling protocol, coating thickness, inspection, embrittlement, and documentation.
Sampling Protocol: Batch Lots vs. Production Lots
ASTM F2329 describes two different sampling plans for batch lots and production lots. Furthermore, there are two types of production lots: Production Lot Detection Process and Production Lot Prevention Process. The differences in the types of lots entail different sampling plans, which specify the number of test articles for performing various test methods during inspection of the finished product. It is important to ensure the customer specifies which type of lot is required. F2329 defines the two different lots and their associated sampling plans as follows:
Batch Lots
A batch lot is defined as a quantity of identical parts cleaned, pickled, fluxed, and galvanized together at one time in a galvanizing basket. F2329 Table 1 provides the sampling plan for batch lots. The batch lot inspection process is more similar to inspection under A153 than inspection of production lots, but Table 1 of F2329 has some additional requirements to consider. See excerpt of Table 1 below.
There are three columns listing the number of test articles for three different inspection tests required under F2329: coating thickness, adhesion, and appearance. Compared to the sampling plan in A153, F2329 requires fewer samples per batch lot size, but the galvanizer is required to also conduct adhesion testing and visual inspection for appearance on these test articles as defined by Table 1. It is important to note the acceptance criterion in all cases is zero defects.
Production Lots
Production lots are defined as batches of parts originating from the same manufacturing lot, processed continuously through cleaning, pickling, fluxing, dipping in molten zinc and spun in a centrifuge, or other means, without any significant change in time, temperature, and concentration of the constituents of the process. There are two types of production lots one for a detection process and the other for a prevention process. For each of these types, there are also inspection criteria for coating thickness, visual appearance, and adhesion. The acceptance number in all cases is zero defects. To determine how many samples are required to test for conformance based on the lot size, F2329 refers to Table 3 of F1470, Practice for Fastener Sampling for Specified Mechanical Properties and Performance Inspection.
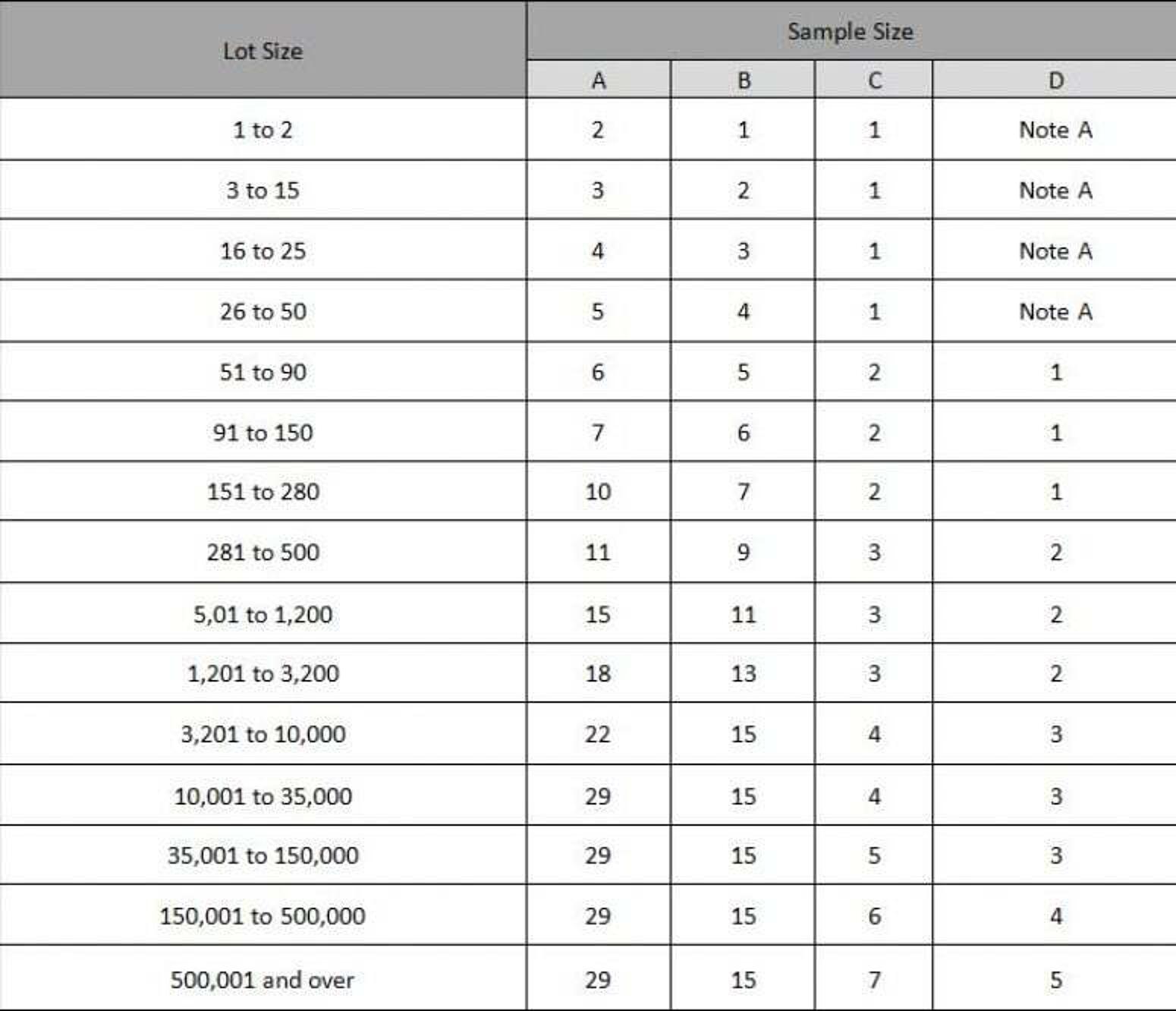
Note A: Suppliers shall furnish certified test results from which the shipping lots originated. If certified test reports are not available, then the supplier must default to Sample Size C and conduct the tests required.
The type of production lot process will determine which column should be referenced for the sample size of each inspection criteria, as summarized in the table below, or per the F2329 Sampling Plan Flow Chart. For example, a lot size of 500 articles under the detection process requires testing of 11 samples for coating thickness, 11 samples for visual appearance, and 3 samples for adhesion.
Inspection
Under F2329, inspection of coating thickness is performed in accordance with Practice E376, which is the same method as required by ASTM A153. According to Note C of Table 1, It is only required to conduct testing on samples for coating thickness once every five batch lots. For long pieces (anchor rods or articles greater than five feet in length), coating thickness measurements must be taken on each end and in the middle of the article. This method is similar to an inspection of coating thickness on multi-specimen articles galvanized per ATSM A123. This additional form of inspection is not required under ASTM A153.
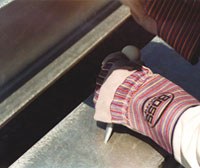
Adhesion testing is not typically performed when galvanizing to the requirements of A153 unless there is evidence of an adhesion concern, but F2329 requires adhesion testing (stout knife test) to be performed for the number of articles listed in Table 1, and for every batch lot.
The test methods for appearance and smoothness under F2329 shall be conducted for every batch lot by visual inspection in accordance with methods provided in A153.
For materials that do not conform to the required test methods in F2329, it is necessary to reference and utilize Paragraph 8 of ASTM F1470, Practice for Fastener Sampling for Specified Mechanical Properties and Performance Inspection, for nonconforming lots.
Coating Thickness
Table 2 of F2329 lists average coating thickness requirements for production lots, batch lots, and individual specimens. A summary of the numerical differences between the two specifications related to coating thickness requirements for all materials is presented in the table: Zinc Coating Thickness Requirements: ASTM A153 vs. F2329. The coating thickness requirements of A153 Table 1 meet or exceed those of F2329 Table 2 except for:
- Fasteners and nuts 3/8 inch and under in diameter: average coating thickness on individual specimens under F2329 is 1.5 mils which is greater than the 1.4 mils required by A153.
- Washers less than 3/16 inch in thickness: average coating thickness on individual specimens under F2329 is 1.5 mils which is greater than the 1.4 mils required by A153.
- Grade A394 Bolts: ASTM F2329 contains Supplementary Requirement 1 for minimum average coating thickness on A394 bolts (2.8 mils average for all specimens and 2.5 mils for individual specimens), which is significantly greater than that required by A153. In ASTM A153, these bolts would fall under the coating thickness requirements of Class C (2.1 mils average for all specimens and 1.7 mils for any individual specimen).
Minimizing Embrittlement
Both ASTM A153 and F2329 point to two methods for preventing hydrogen embrittlement: baking after pickling and before galvanizing, or abrasive blasting and then flash pickling prior to galvanizing. If it is necessary to test for embrittlement under ASTM A153, it is to be conducted per A143 Paragraph 9. On the other hand, if embrittlement testing is necessary under F2329, it is to be conducted per ASTM F606 (a wedge positioned and tensioned under a bolt head), which is a different method than any of the methods described within A143 Paragraph 9. Each bolt specification may list additional methods to prevent hydrogen embrittlement as well as place additional requirements on embrittlement testing which should be researched separately.
Mechanical Testing & Recording of Bath Temperature
The temperatures used in the hot-dip galvanizing process typically do not appreciably alter the mechanical properties of steel, but there are some instances when there are potential concerns. These instances can include when steel has been severely work hardened or when the galvanizing bath temperature exceeds the stress relief or tempering temperatures of the fasteners. Fasteners which are subjected to severe work hardening must be stress-relieved prior to galvanizing. Paragraph 7.2.1.2 of F2329 requires the purchaser arrange for mechanical testing after galvanizing if the galvanizing bath temperature (noted as 820-900 F) is greater than the stress relieving or tempering temperatures.
It is necessary for the galvanizer to communicate the bath temperature to the customer to ensure the end user understands the effects the galvanizing temperature will have on the steel. If the customer specifies, the galvanizer will be required to provide the average galvanizing temperature the fasteners will be exposed to. Best practice is to note the bath temperature when galvanizing steel to F2329, although only the average bath temperature is required.
Quenching
According to F2329 Paragraph 5.3.1, all parts are to be quenched in water unless air cooling is specified by the customer to prevent the formation of zinc oxide. Additionally, Paragraph 5.5.1 allows the customer to request a post-treatment such as chromating to reduce the possibility of wet storage stain, or phosphating to assist in subsequent painting. Because A153 does not require water quenching nor chemical post-treatments, communication between the customer and the galvanizer is required to determine whether the galvanizer has a quench tank and the capability to perform chemical post-treatments, or if air-cooling will be acceptable.
Lubrication
ASTM A153 does not require lubrication of hot-dip galvanized fasteners, but F2329 Paragraph 5.5.2 allows the customer to request lubrication be applied to nuts, bolts, or screws to enhance assembly. Therefore, it must be clarified whether the plant has the ability to lubricate hardware after hot-dip galvanizing. Otherwise, a third party will be required to apply the lubricant at an additional cost.
Delivery & Documentation
ASTM F2329 requires more detailed ordering information by the customer and more documentation by the galvanizer required upon delivery than ASTM A153. The amount of additional documentation beyond ASTM A153 requirements will vary depending on a number of optional requirements the customer can specify under F2329. However, if a purchaser also requires the galvanizer to inspect dimensional requirements of parts upon delivery, they must provide the galvanizer with the necessary tools and inspection gauges.
© 2025 American Galvanizers Association. The material provided herein has been developed to provide accurate and authoritative information about after-fabrication hot-dip galvanized steel. This material provides general information only and is not intended as a substitute for competent professional examination and verification as to suitability and applicability. The information provided herein is not intended as a representation or warranty on the part of the AGA. Anyone making use of this information assumes all liability arising from such use.