Transmission
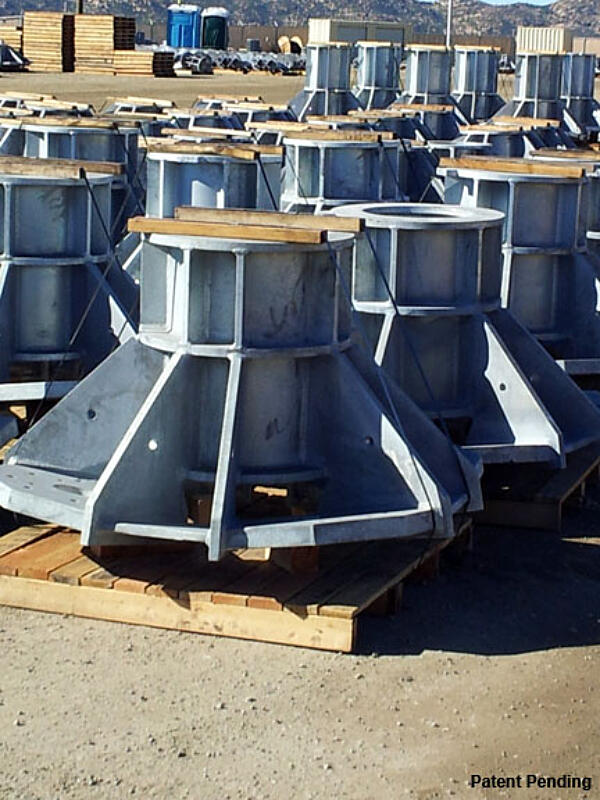
Though there is still uncertainty about the power generation sources of the future, the North American transmission grid will have to be upgraded and expanded. As the demand for power has increased, new generation facilities have followed suit; however, the investment in North Americans transmission grid has not. The Consumer Energy Council of American (CECA) estimates new transmission lines will be added at only 1/3 the rate of demand from 2003 to 2013. This coupled with the $0.6 billion annual price tag for corrosion along the transmission grid, North Americas transmission capacity is falling further and further behind the energy demands.
In 2002, the US Department of Energy acknowledged increasing concern with the overextended transmission grid:
There is growing evidence the US transmission system is in urgent need of modernization. The system has become congested because growth in electricity demand and investment in new generation facilities have not been matched by investment in new transmission facilities…Because the existing transmission system was not designed to meet present demand, daily transmission constraints or bottlenecks increase electricity costs to consumers and increase the risk of blackouts.
As energy demands are expected to continue to rise at least 1% per year over the next 25 years, the transmission grid is in need of additions and upgrades. The blackout in August of 2003 across parts of the Northeast and Canada highlighted how costly the overexerted system and blackouts can be with estimates in the billions of dollars. Additionally, as the grid becomes more overloaded, even maintenance of existing structures could lead to costly shutdowns or brownouts.
Substations
To get energy from a power source to the consumer, energy travels along a power distribution grid. After leaving the power generation plant, electricity travels to a transmission substation , which up-converts voltage to travel long distances along the transmission grid. Eventually, the electricity passes through an electrical substation which converts, or steps-down, the voltage from transmission strength to distribution strength levels that can safely transmit to the consumer. Electric power may flow through several substations between generating plant and consumer, and may be changed in voltage in several steps.
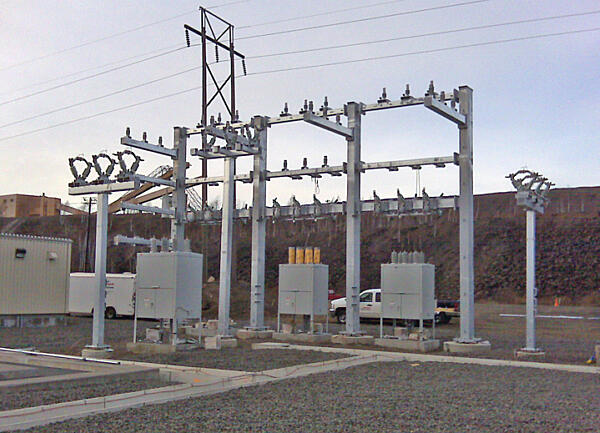
Throughout this process, reliable and consistent transmission of power is of the upmost concern, and should be taken into consideration when planning the development of any substation. Utility companies are in the business of delivering energy to their customers; therefore, minimizing interruptions and ensuring the substations have the longest service life possible is both desirable and economical. Aiding this effort, accessible inventory is a necessity to prevent lengthy shutdowns for emergency repairs.
To retain any credibility as a public company, energy must be provided consistently and on-demand. Anything distracting the power company from that objective compromises their public image and their ability to meet consumer needs. Hiccups in power transmission due to routine maintenance or difficult-to-access inventory should be avoided, and galvanized steel provides a way to prevent such delays. Because hot-dip galvanized (HDG) steel can last 70+ years with little or no maintenance, galvanizing steel substation elements such as structural steel, bolts, and pipes will prevent the indirect costs of stopping operations for routine maintenance. Shutting down a substation would not only be inefficient for the power company, but also detrimental to consumers expecting consistent power to be supplied.
Substations are constructed of massive quantities of various steel elements, from fasteners and base plates to structural steel and poles. If an emergency repair is required, acquiring the correct steel parts in a timely matter to ensure shutdowns or breaks in service are kept to a minimum is imperative. Because of its durable, maintenance-free nature, galvanized steel elements can be stockpiled outside for years, waiting for immediate implementation, without compromising the zinc coating and its corrosion protection. Not only can the steel pieces be bought and saved for future use, they can even be purchased and stored when steel and galvanizing prices are low to reduce the cost of an expensive, hard-to-get emergency replacement.
Highly flexible for adaptation, a steel substation frame is ideally suited for expansion and additional steel reinforcement will couple easily with the original design. By using techniques such as welding, bolting and splicing of existing vertical and horizontal structural elements, a steel framing system is easily expanded to maximize the efficiency of available space. Steel gives the designer more flexibility to negotiate problem areas and develop efficient solutions for expansion. In addition to the durability allowing hot-dip galvanized steel to be stocked, hot-dip galvanized is readily and rapidly available. Speedy delivery and easy adaptation for expansion mean hot-dip galvanized steel substations will provide even more power quicker, and with fewer breaks in service.
Lattice Towers/Poles
The power grid is interconnected and essentially functions as one system throughout the U.S. and Canada, not having any particular divisions. Electricity flows not just from the generation point and over the transmission lines to the end-user, but between transmission lines as well. This networked system helps to achieve a high reliability for power delivery, since any one power plant that shuts down should only constitute a fraction of the power being delivered by the power grid. Integral to that high reliability is a stable infrastructure of hot-dip galvanized transmission towers and poles.
Galvanized steel lattice towers and poles have been utilized for high voltage electricity transmission by power companies for over 100 years for good reason they reliably support conductors without maintenance, can withstand strong external wind and ice loads, and are durable against the ravages of abrasion and corrosion. Hundreds of thousands are in place in rural, urban, and suburban environments, in configurations such as H-frames, three-pole, lattice, and monopole. Perhaps the most famous of these is a lattice tower, the Eiffel Tower in Paris. Hot-dip galvanizing offers poles a number of options for construction and installation and are reliable over decades.
There are three distinct corrosion environments for transmission towers and poles not mounted on concrete foundations, i.e. placed directly in soil. Specifically, those three environments are in the soil, at ground level, and in the atmosphere. As the same steel piece is subjected to all three of these environments simultaneously, it is necessary to specify a corrosion protection system versatile enough to withstand the varying conditions.
More insidious than corrosion easily visible on the exterior surface of a steel element is the possibility of corrosion on the inside of tubular steel sections. Moisture from condensation collects inside the hollow structures creating a highly corrosive environment. Over time, this moisture pools at the base of the poles weakening the structure which can lead to a collapse under wind forces or other stress. Hot-dip galvanized steel is better suited for this environment than other common materials such as painted and weathering steel because of its complete coverage. Hot-dip galvanizing is a total immersion process completely coating the interior and exterior of hollow structures.
As technology increases, and more power is necessary in our everyday lives, the infrastructure carrying the electricity must also grow. However, no one wants to see additional transmission towers in their backyard. The more unobtrusive the new lines, the better in the minds of most in the community. The matte gray finish of hot-dip galvanizing blends in almost any environment seamlessly. However, at times, the combination of galvanized steel and paint, or a duplex system, are used to disguise the towers even further. Working in synergy, a duplex system protects steel for 1.5 to 2.3 times the sum of the two systems alone providing aesthetically pleasing long lasting protection for these power necessities.
Utilizing hot-dip galvanized steel throughout the new and upgraded transmission grid will help alleviate future corrosion costs and maintenance shutdowns. Whether substations or lattice towers and poles , hot-dip galvanizing will provide maintenance-free corrosion protection for decades ensuring the new transmission structures capacity remain in full operation for generations.
Transmission Case Study
Tulsa Port of Catoosa Substation- Catoosa, OK; 2013
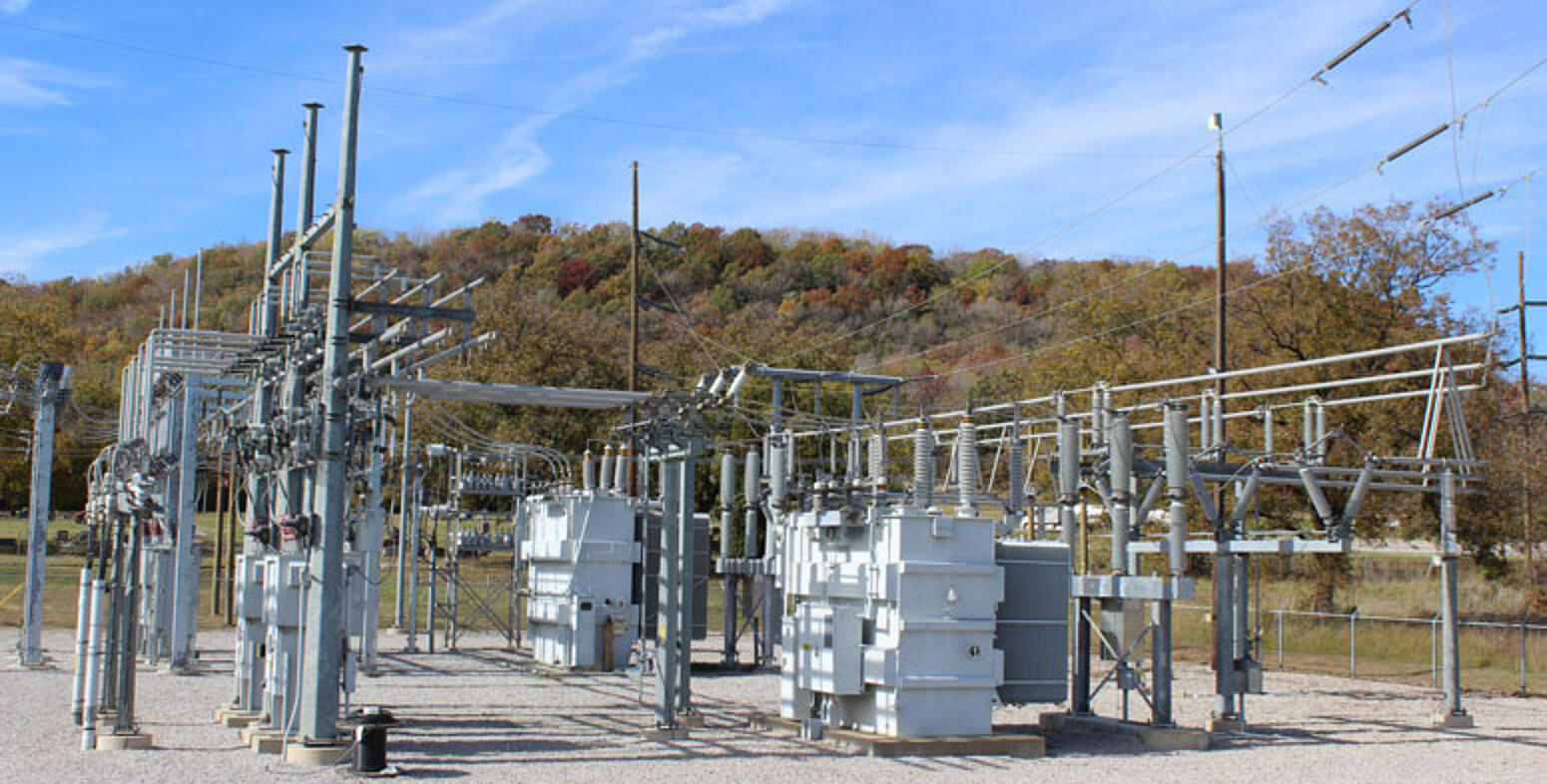
The Tulsa Port of Catoosa is one of the largest, most inland river-ports in the United States. Located in Northeast Oklahoma, the Tulsa Port of Catoosa offers year round, ice-free barge service with river flow levels controlled by the U.S. Army Corps of Engineers. With worldwide access capabilities, product and materials travel easily and efficiently from America's heartland to the rest of the globe.
The expansion of the Tulsa Port of Catoosa substation ensures port operations will continue without risk of interruption and positions the port to host additional business growth. The selection of hot-dip galvanized steel to construct this critical infrastructure will ensure the reliable, cost-effective delivery of electric service to the Tulsa Port of Catoosa for generations to come.