Distribution
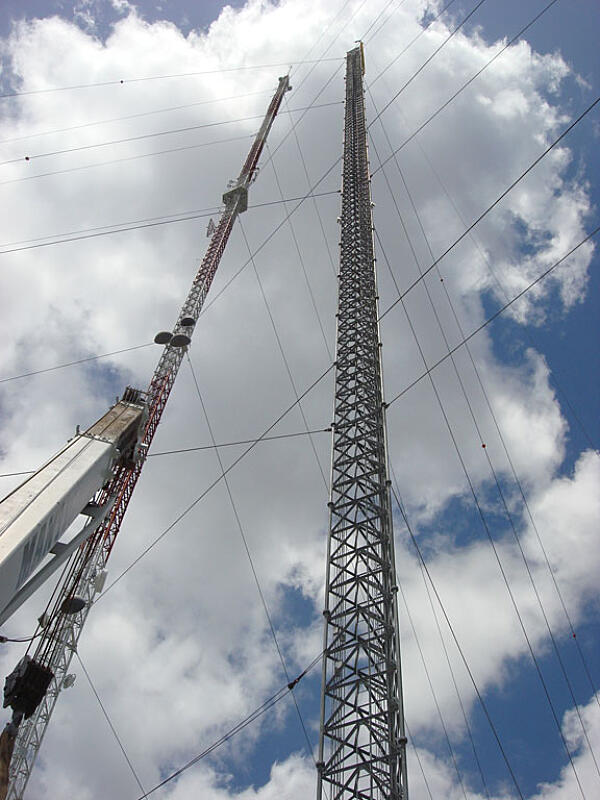
Once power is generated and transmitted over long distances to substations, it is stepped-down and distributed to residential, commercial, and industrial consumers. When distribution lines were first being built more than 50 years ago, wooden poles were used and placed directly in the soil to bring power to every demand point. At the time, wooden poles were relatively durable, plentiful, and inexpensive. However, in recent years the wooden poles have shown the cracks in their armor.
There are approximately 185 million utility distribution poles in North America, and 2-4 million are replaced annually. In the last 20 years, galvanized steel poles have made inroads in the marketplace, because they provide a variety of advantages over wood and are less expensive than in-ground placement of cables. Galvanized steel support poles prove to be a more sustainable solution than wooden poles, and without any of the complications or constraints in the design or durability.
Being environmentally conscious is currently a tremendously important factor as utility companies struggle to balance present needs without compromising the future environment. With preservation of the country's resources in mind, it is pertinent to utilize materials that are not only abundant, but also durable enough to withstand the rigors of the environment. On average, it will take a tree 25 years to mature in the environment, barring any natural or man-made interruptions. With more than 185 million utility poles in the nation, and a replacement rate of 2-4 million per year, it would be nearly impossible to plant and mature new trees at the rate they would be depleted for replacement poles.
Wooden distribution poles not only have environmental limitations, but also logistical ones. Wooden poles have limited tension strength and limited load bearing ability, which are needed in distribution environments to support larger and heavier loadings, and longer spans and height requirements. Additionally, wood poles require toxic chemical preservatives to prolong their service life, which at the end of life create hazardous waste disposal concerns and are susceptible to wood rot and insect damage which can cause them to fail before their intended design life.
With the limitations to wood, the conversion to hot-dip galvanized (HDG) steel poles makes sense. The primary components of galvanized poles; steel and zinc are both readily available. In fact, zinc is the 24th most abundant element in the Earth's crust and steel is the most recycled material in the world. And at the end of life, hot-dip galvanized steel (zinc and steel) is infinitely and fully recyclable without the loss of any properties.
Furthermore, HDG poles can be designed to encircle existing structures with ease and facilitate future expansion or retrofitting. A great example of this flexibility is the Pole-Max produced across North America which adds additional capacity to existing poles. HDG steel poles are self-conducting and thus have no need for a full-length copper grounding wire, and they can either be embedded or have an anchor base, and do not require fastener retightening due to pole shrinkage.
In addition to the abundance, availability, and flexibility of natural zinc and steel, HDG steel distribution poles provide consistent, superior strength for decades without maintenance. No maintenance means no additional consumption of raw materials and no preservation chemicals or emissions to the environment throughout the life of the galvanized pole. HDG steel's longevity will not only save money on replacement poles, but also keep forests green and growing.
Distribution Case Study
Omaha, NE Transmission Line- Galvanized starting in 1971
In 1970 Omaha Public Power District (OPPD) collaborated with the American Society of Civil Engineers (ASCE) and a local steel fabrication facility to design and test a new octagonal transmission pole. Time proved that round, painted utility poles did not withstand Nebraska's beautiful, but often harsh seasonal changes. Therefore, this newly designed trial pole was specified to be hot-dip galvanized to provide a cost effective and high quality coating to ensure the large exposed structure would have long lasting corrosion protection. Not only does the manufacturer agree that hot-dip galvanizing is the best choice for long lasting corrosion protection, but a galvanized coating also supports service life improvement for the many diverse utility structures and products his company manufactures around the world.