Structural
Bridges perform a critical function in our highway system, and a galvanized steel bridge will ensure taxpayer money is spent effectively on an attractive, stable bridge that will remain corrosion-free for decades with little or no maintenance. In the Steel Bridge Design Handbook, the National Steel Bridge Alliance (NSBA) explains bridge designers should view corrosion as a long-term threat to the integrity of the bridge structure and a critical design consideration that must be addressed in a rational manner during the design process.
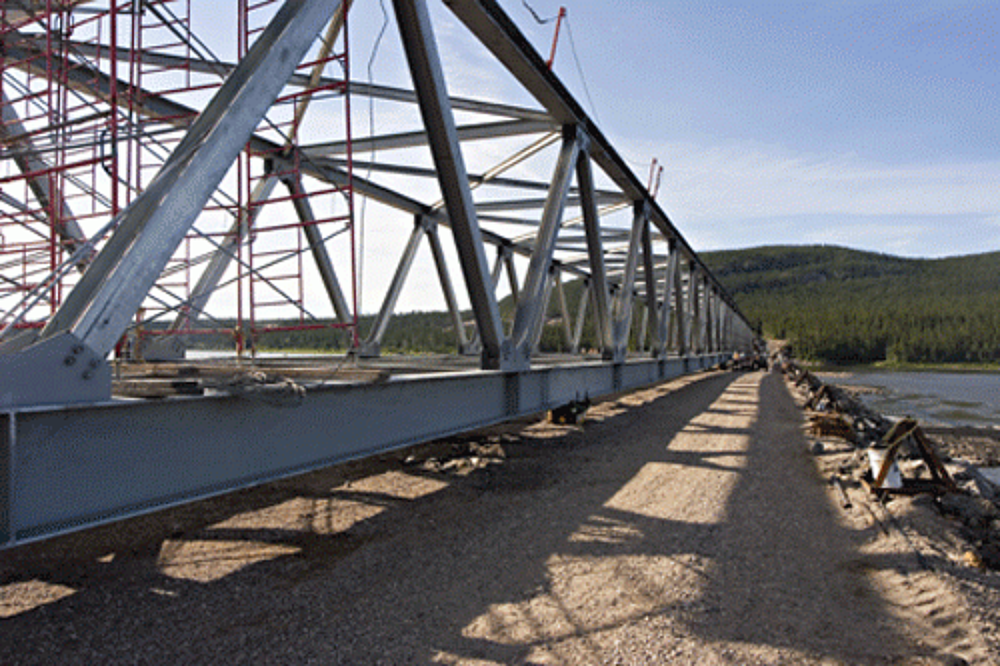
How a designer approaches protecting a steel bridge from corrosion will set the stage for the structures future costs and stability, and can make or break bridge and highway budgeting. An examination of competing bridge materials will reveal how hot-dip galvanized steel stands head above the rest.
One example of galvanized steel in the superstructure is the Bergen County Bridge in Fairlawn/Patterson, New Jersey. The truss bridge is not only functional but also an aesthetic addition to the area. The open trusses allow more visual flow and blending with the landscape, while the choice to hot-dip galvanize will allow the bridge to stand maintenance-free for decades.
Structural Efficiency
Because of the high strength-to-weight ratio of steel, hot-dip galvanized steel bridges are less taxing on the support structure than significantly weightier material options, such as concrete. According to the World Steel Association, the strength-to-weight ratio minimizes substructure costs and can also save money on transportation and handling.
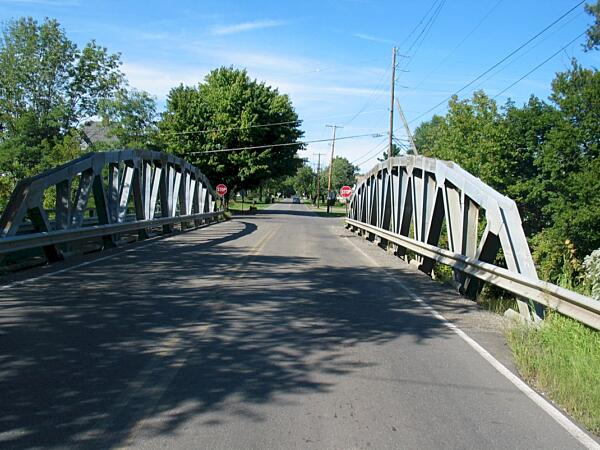
This benefit is particularly important for bridges spanning large bodies of water, wetlands, or environmentally protected areas, which may require cost-effective long span bridge elements. The ability to use long-span beams minimizes the necessary supports and reduces overall stress to the supporting structure, which will allow for lighter foundations and particularly helpful in areas with poor ground conditions.
Reducing the weight of the bridge in total translates to cost savings throughout the process. One of the biggest advantages of steel is weight savings, which mean lower erection costs. The lighter weight of the pieces means they will require lighter, less costly handling equipment during construction.
Speedy Construction
Several elements contribute to the fast erection time of steel bridges. Steel beams are fabricated offsite and delivered to the site ready for construction. The smaller size/weight of the steel pieces makes them more easily maneuverable onsite. Utilizing small, easy to maneuver members with a prearranged method of erection makes construction simple and will have cars speeding across the span in short order.
The hot-dip galvanizing process works swiftly and seamlessly into the assembly progression. After the steel members are fabricated, they are sent to the galvanizing plant. As the galvanizing process is completed at an indoor facility, there are no hindrances due to inclement weather so the pieces are in and out of the galvanizing plant, then promptly delivered to the site. With the swift turnaround time of these elements, builders are measuring completion times in weeks, not months.
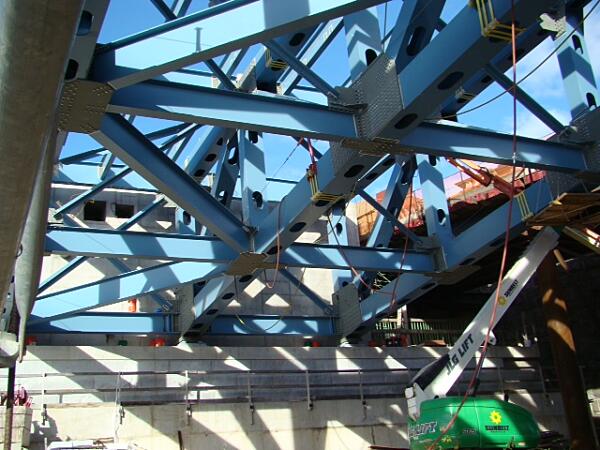
Easier Inspection
With structural stability and safety being of critical importance to bridge construction, the ability to perform easy visual and surface inspections is a great convenience. Rather than relying on intrusive core sampling, as can be necessary with concrete structures, steel bridges can be tested visually or as they stand. This avoids the inconvenience and indirect costs of impeding traffic for routine inspection. The National Steel Bridge Association (NSBA) explains it is easier to inspect and determine the structural state of a steel bridge where all the components are visible. Hot-dip galvanized steel has a consistent and measurable life-expectancy for corrosion protection and can be monitored with easy, visual inspections and surface-based testing.
Safety in Seismic Conditions
Hot-dip galvanized steel bridges can also provide advantages in areas of seismic activity. Steel bridges are more seismic resistant than concrete ones due to the ductile, adaptable nature of the steel elements, and the high strength-to-weight ratio. Structural steel helps minimize weight, which reduces inertia effects under seismic loading. Able to bend within reason without breaking, the tensile strength of hot-dip galvanized steel can protect a bridge from damage or even total failure during seismic activity, protecting both taxpayer investment, and more importantly, the cars and people utilizing the structure.
Aesthetics
Though not critical to the structural stability of the bridge, aesthetics are key to the social impact of the structure. Utilizing galvanized steel allows the designer to take advantage of the flexible nature of steel, as well as the attractive, rust-free appearance of the zinc coating.
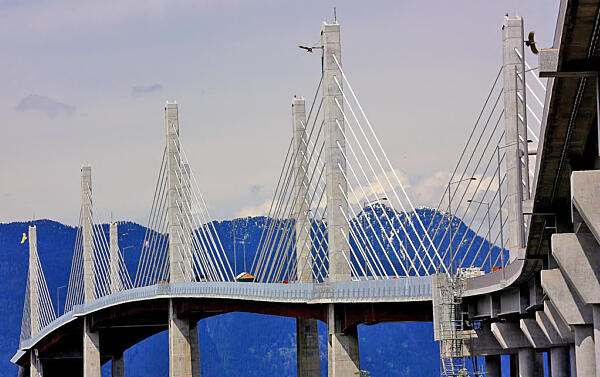
A hot-dip galvanized steel bridge allows for a range of design possibilities affecting both beauty and functionality. Unlimited by the weight constraints of concrete, steel bridges can take on a variety of appearances; whether a truss, suspension, or cable-stayed structure, steel bridge design is limited only by the engineer's imagination.
The bridge frame can take advantage of a wide variety of steel design options by utilizing features such as arched supports or streamlined steel cables, while the deck level can make use of sleek, modern railings and even decorative paneling to make the bridge stand out for more than just function.
Not only can galvanized steel bridges prove to be architecturally inspiring, they also allow for a variety of attractive appearance options. The cool metallic sheen of galvanized steel is a desirable look itself, but the system is also proven to keep the unattractive effects of corrosion at bay for 70+ years. This keeps exposed elements looking their best for generations to come. If a modern gray gleam is not the desired option, galvanized steel also offers the option of utilizing a duplex system, such as paint over galvanizing.