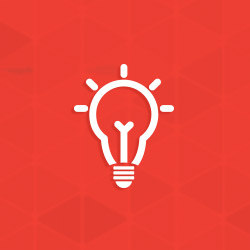
Surface Preparation Prior to Galvanizing
What surface preparation of the steel or iron is necessary prior to it arriving at the hot-dip galvanizing plant?
Many specifications for protective coatings include provisions for surface preparation prior to coating application and inspection requirements during/after coating application. For galvanizing there is usually no special preparation required. Let me explain.
ASTM specifications for batch hot-dip galvanizing are arranged differently. For example, ASTM A123/A123M and A153/A153M (the most commonly used hot-dip galvanizing specifications in North America) cover the inspection requirements of the finished galvanized product but do not discuss surface preparation of the steel or iron prior to it being galvanized. ASTM A143/A143M, A384/A384M, and A385/A385M discuss fabrication procedures for steel to be hot-dip galvanized and address some surface preparation recommendations prior to galvanizing.
Surface Preparation Prior to Hot-Dip Galvanizing
.gif)
Batch hot-dip galvanizers have a simple process they use to prepare steel or iron prior to galvanizing. After the steel has been inspected to ensure it has adequate vent and drain holes, it is dipped into a series of cleaning chemicals. The first chemical is a degreasing bath that removes organic contaminants such as dirt, grease, and oil from the metal. The next chemical used is pickling acid, which removes mill scale and rust (oxides) from the steel. The last step before galvanizing is dipping the steel or iron into a flux bath, which prevents oxidation of the metal prior to entering the galvanizing bath and also aids the galvanizing reaction in developing the hot-dip galvanized coating.
ASTM specifications do not have required parameters for cleaning chemicals used in the galvanizing process. There are general concentration ranges these chemicals are most effective and each galvanizer optimizes their cleaning chemicals to give them the best results at cleaning the steel or iron and achieving a high-quality hot-dip galvanized coating.
Materials the Cleaning Chemicals Cannot Remove
There are some materials the cleaning chemicals used prior to galvanizing cannot remove or have great difficulty removing. Here is a list of the most common of these materials:
- Weld slag and other welding flux residues
- Weld splatter and anti-splatter
- Burrs (could include excessively rough edges from flame cutting)
- Very heavy or extremely adherent mill scale
- Mill coatings such as varnishes or lacquers present on some types of pipe
- Epoxies, types of vinyl, and asphalt
- Sand and other impurities on castings
- Oil-based paints and markers
- Crayon markers
- Very heavy or thick deposits of wax or grease
These materials should be removed from the metal prior to it being delivered to the galvanizing plant. SSPC and NACE have a variety of commonly used standards for abrasive blast cleaning, hand cleaning, and power tool cleaning, effective at removing these materials. Abrasive blasting is usually necessary on castings to remove sand and other impurities from the casting process. Alternatively, different products can be used on the steel or iron which are compatible with the hot-dip galvanizing process to reduce the need for blasting or hand/power tool cleaning. For example, using uncoated electrodes avoids the problem of depositing flux on the metal during welding, and galvanizing-safe markers are available that dissolve in the cleaning baths used in the galvanizing process. Different types (specifications) of pipe can be ordered that are free of mill coatings such as varnishes, lacquers, or oils.
Other Considerations
Some specifiers use generic preparation processes for steel or iron that will be coated, such as always abrasive blasting it. In most cases, this is not necessary prior to the galvanizing process unless the metal to be galvanized is contaminated with the materials listed above. The cleaning steps prior to the hot-dipping process adequately clean the metal and ensure a high-quality hot-dip galvanized coating develops on the metal. In fact, the only way a galvanized coating can develop is if the metal is free of organic contaminants, mill scale, and oxides. This is a built-in quality control process in that if a galvanized coating has developed, the underlying metal must have been free of contaminants.
If steel is excessively rusted or pitted, these problems should be discussed with the engineer to ensure there will not be any structural integrity concerns. Additionally, excessively rough or pitted steel or iron will tend to develop a rough galvanized coating.
If you have questions concerning the condition or contamination of the steel or iron you would like galvanized, you can discuss them with your galvanizer or contact the American Galvanizers Association Technical Department at 720-361-4485.
© 2025 American Galvanizers Association. The material provided herein has been developed to provide accurate and authoritative information about after-fabrication hot-dip galvanized steel. This material provides general information only and is not intended as a substitute for competent professional examination and verification as to suitability and applicability. The information provided herein is not intended as a representation or warranty on the part of the AGA. Anyone making use of this information assumes all liability arising from such use.