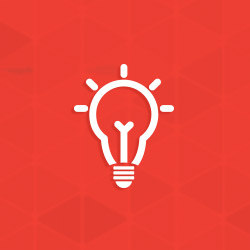
Difference Between Hydrogen and Strain-Age Embrittlement
What are the differences between hydrogen embrittlement and strain-age embrittlement?
Although it happens infrequently, embrittlement of steel during the hot-dip galvanizing process is possible. The most known type of embrittlement is hydrogen embrittlement, but this type of embrittlement is very rare during the galvanizing process. If a steel member embrittles during galvanizing, odds are it is due to strain-age embrittlement, not hydrogen embrittlement. To differentiate hydrogen embrittlement from strain-age embrittlement, it is best to start with the definition of the word embrittlement.
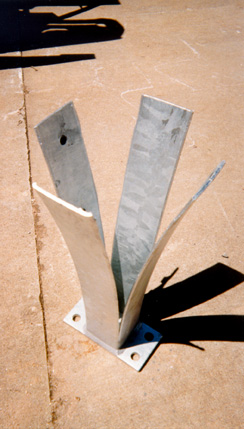
To paraphrase the definition as the term is defined in ASTM A143/A143M Standard Practice for Safeguarding Against Embrittlement of Hot-Dip Galvanized Structural Steel Products and Procedure for Detecting Embrittlement, embrittlement is the loss or partial loss of ductility in steel that fails by fracture without appreciable deformation. Another way to think about embrittlement is steel cracking without any bending or flexing to indicate the steel is yielding.
Strain-Age Embrittlement
The most common type of embrittlement encountered in the hot-dip galvanizing process is strain-age embrittlement. Strain-ageing is a process where steel becomes very brittle in areas of high stress when exposed to elevated temperatures. At room temperature, strain-aging happens very slowly, but at elevated temperatures, like those used in the galvanizing process, strain-aging can happen very quickly. When the steel has incurred enough stress due to strain-aging, it can become embrittled. For strain-aging to occur, two components are necessary.
The first component is stressed must be induced into the steel prior to the galvanizing process. This normally occurs through cold working the steel. Cold working can include bending, punching, or shearing the steel. If the stresses from these cold working practices are not relieved prior to galvanizing, they become points of high residual stress during the galvanizing process and can lead to strain-age embrittlement. Strain-ageing can also be caused by impurities in the steel, such as those found in lower quality steels used for reinforcing bar. If a part cracks due to strain-age embrittlement, the cracking occurs immediately after galvanizing but is also often seen at the job site, as in the case of reinforcing bar. Often times simple handling is enough stress to cause a strain-age embrittled member to crack.
Cracking of the steel shortly after galvanizing is a critical distinction between strain-age embrittlement and hydrogen embrittlement. There are several ways to reduce the occurrence of strain-age embrittlement, but all methods focus on one aspect reducing the stresses induced into the steel prior to galvanizing. Instead of cold working, which induces stresses into steel, the steel can be hot worked at temperatures between 1100F and 1300F. If it is necessary to cold work the steel, relieving the stresses induced from cold working can be accomplished by heating the steel to 1200 1300F for heavy cold working and up to no more than 1200F for less severe cold working. When bending steel, it is best to allow for a bend diameter at least three times the section thickness. When punching is necessary on thicker steels (3/4 or greater in thickness), the holes should be reamed at least 1/16 around the edge of the hole. When flame cut coping is necessary, such as on structural beams, the minimum radius of the copes should be one inch or greater. Grinding the areas around the cope is recommended to remove small micro-cracks in the steel from the flame cutting process.
Hydrogen Embrittlement
Hydrogen embrittlement occurs when steel cracks due to hydrogen trapped between the grains of the steel. Although steel commonly absorbs hydrogen during the hot-dip galvanizing process, it is usually expelled due to the temperature of the zinc in the galvanizing kettle. In some cases, however, the grain size of the steel is too small to allow the release of atomic hydrogen. This can later cause cracking due to increased stress at the location of the hydrogen between the grains. Grains of steels with a tensile strength below 170 ksi (170,000 psi) are usually big enough to allow escape of hydrogen, but for steels having a tensile strength of 170 ksi or greater, there is a potential for hydrogen to remain trapped between grains leading to hydrogen embrittlement. Hydrogen embrittlement is not observed until the part is under load, unlike strain-age embrittlement which is observed shortly after galvanizing. In other words, whereas strain-age embrittlement can be observed shortly after galvanizing, hydrogen embrittlement is not seen until the steel has been under load for some extended period of time. Hydrogen embrittlement can be avoided in several ways.
The most obvious way is to ensure the designer has chosen steel with a tensile strength less than 170 ksi. As stated earlier, these types of steels have grains large enough to allow escape of any trapped hydrogen. When it is necessary to galvanize high-strength steel, a modified galvanizing process can be used to minimize the chances of hydrogen embrittlement. Rather than pickling the steel for the normal length of time, this modified process includes mechanically cleaning the steel, such as by blast cleaning, and then flash pickling (less than 30 seconds in the pickling bath) the steel. Flash pickling is necessary to remove any residues from the blasting operation. This reduces the amount of hydrogen the steel is exposed to and thus reduces the chances of hydrogen becoming trapped in the small grains of high-strength steel.
Who Is Responsible for Avoiding Embrittlement?
ASTM A143/A143M spells out who is responsible for avoiding embrittlement. The responsibility lies on the designer, fabricator, and the galvanizer, but each party has different responsibilities. Choosing steel appropriate for the practices normally encountered in the galvanizing process and designing the product to avoid embrittlement are the responsibilities of the designer. The fabricator is responsible for using suitable fabrication procedures to avoid embrittlement, such as following minimum bend recommendations and reaming holes on thicker steel (as discussed above). And finally, the galvanizer is responsible for employing proper pickling and galvanizing procedures during the galvanizing operation. Communication between the designer, fabricator, and galvanizer is key. Communication throughout the design, fabrication, and galvanizing processes ensures best practices are used throughout and thus minimizes the possibility of strain-age or hydrogen embrittlement. For more information on avoiding embrittlement during hot-dip galvanizing, see ASTM A143/A143M or contact the AGA Technical Department.
© 2025 American Galvanizers Association. The material provided herein has been developed to provide accurate and authoritative information about after-fabrication hot-dip galvanized steel. This material provides general information only and is not intended as a substitute for competent professional examination and verification as to suitability and applicability. The information provided herein is not intended as a representation or warranty on the part of the AGA. Anyone making use of this information assumes all liability arising from such use.