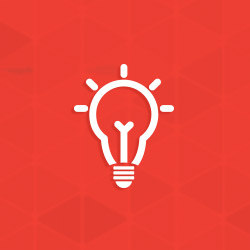
Controlling Spangle - Influences
Some of my customers are asking me to produce a galvanized coating with highly spangled appearance. What controls spangle in the galvanized coating and what can I do to control how much spangle will be present?
Let's first begin by defining "spangle." Spangle is the appearance of tiny triangular and/ or flower~shaped crystals on the outer surface of the galvanized coating. Often times they are referred to as "flowers of zinc." Now, isn't that pretty? Architects and engineers who appreciate the aesthetic value of the galvanized coating frequently desire this spangled appearance. This coating phenomenon is a combined product of multiple variables; however, it can ultimately be controlled by adjusting bath chemistry and cooling time. The presence of spangle on the galvanized coating is the result of minor bath additions forming alloy crystals with zinc. Elements that alloy with zinc to produce spangle include lead, tin, aluminum, cadmium, antimony, copper and a variety of others. The most common bath components are Zn-Pb-Sn or Zn-Al-Pb. The size and type of spangle are greatly affected by the concentrations of the two alloying elements and rate at which the article is cooled. Figure l & 2 are charts that approximate the size of spangle that will be produced from varying bath compositions and cooling rates for a Zn-Pb-Sn kettle. A general trend that is clearly evident from the two charts is that the largest (and most defined) spangles are produced from the slowest possible cooling times and higher amounts of the minor alloying element (in this case tin).
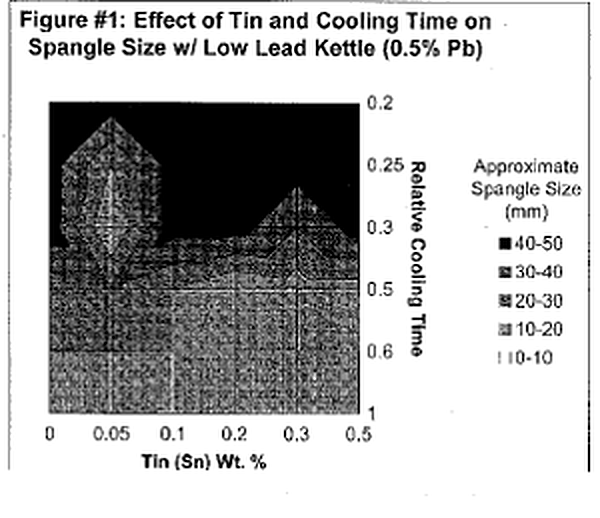
The largest crystals, or spangle, are formed on smooth surfaces with a thin layer of Zi1"lC. Sufficient time for crystal growth is also required. Quenching articles after galvanizing will cool the zinc coating to a level below that at which crystals form and the appearance of spangle will be significantly decreased if any is present at all. When galvanizing reactive steels, the intermetallic layers will consume all of the shiny, free zinc available to create spangle, resulting in a dark, matte gray, Zn-Fe alloy coating. Thus, aesthetically pleasing spangle cannot be produced on reactive steels, unless the rapid coating growth is controlled by the bath additions.
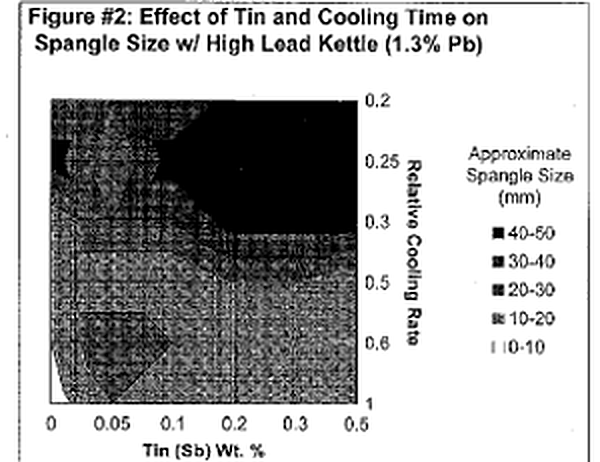
The immersion time of the part in the galvanizing kettle also plays a role in producing spangle. The longer the dip time, the thicker the intermetallic alloy layers, which results in less free zinc available to form crystals once removed from the kettle. Studies have shown that the base steel roughness and grain size also affect the formation of crystals. Rougher steel surfaces have shown to produce spangle of smaller size than with smooth, uniform surfaces.
Also, steels that absorb large amounts of hydrogen from the pickling process produce a less spangled finish. The amount of hydrogen absorbed by the pickling process must be expelled in the galvanizing kettle. The subsequent release of hydrogen causes disturbances in the coating formation that disrupt the formation of crystals. So if you want to have the prettiest darn galvanized coatings in town, make sure you know that the only way to produce a "garden" of zinc flowers on your steel is to start "seeding" your bath with tin or aluminum and don't forget to not water (quench) them!
© 2025 American Galvanizers Association. The material provided herein has been developed to provide accurate and authoritative information about after-fabrication hot-dip galvanized steel. This material provides general information only and is not intended as a substitute for competent professional examination and verification as to suitability and applicability. The information provided herein is not intended as a representation or warranty on the part of the AGA. Anyone making use of this information assumes all liability arising from such use.