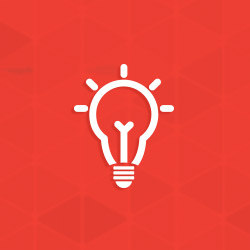
Venting and Draining
What considerations should I keep in mind for venting and draining when designing steel fabrications to be galvanized?
In the hot-dip galvanizing process, steel is completely coated with corrosion-inhibiting zinc, which forms a highly abrasion-resistant metallurgical bond with the base steel. In order to ensure that all interior and exterior surfaces are protected from corrosion, entire steel fabrications are lowered into and raised out of cleaning solutions, flux solutions, and molten zinc metal. In order to facilitate interior and exterior cleaning and coating, it is necessary to provide holes in fabrications to be galvanized.
The primary reason for vent and drain holes is to allow air to be evacuated from within and around the fabrication, allowing it to be completely immersed in the cleaning solutions and molten zinc and for the excess zinc and solutions to drain out and away from the part.
The secondary reason is if fabrications to be galvanized are not properly vented, cleaning solutions or rinse waters trapped in overlapping or contacting surfaces flash to steam. The resulting pressure increase (up to 3600 psi [25MPa]) can rupture the fabrication. Additionally, trapped moisture that flashes to steam can result in localized uncoated surfaces.
Because items being galvanized are immersed in and withdrawn from all cleaning solutions and molten zinc at an angle, vent holes should be located at the highest point and drain holes at the lowest point as mounted during the galvanizing process.
Drainage
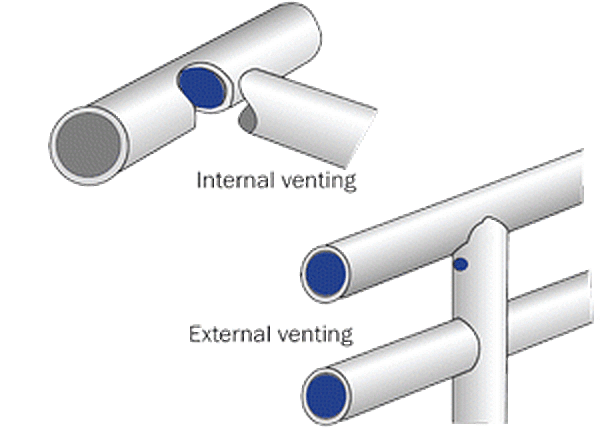
For effective galvanizing, cleaning solutions and molten zinc must flow without undue resistance into, over, through, and out of the fabricated article. Failure to provide for this free, unimpeded flow can result in complications for the galvanizer and the customer. Improper drainage design results in poor appearance, bare spots, and excessive build-up of zinc. All of these are unnecessary and costly, and another example of why communication throughout the project is key.
A few common fabrications where drainage is important are gusset plates, stiffeners, end-plates, and bracing. Following these best design practices will help ensure the highest quality coatings:
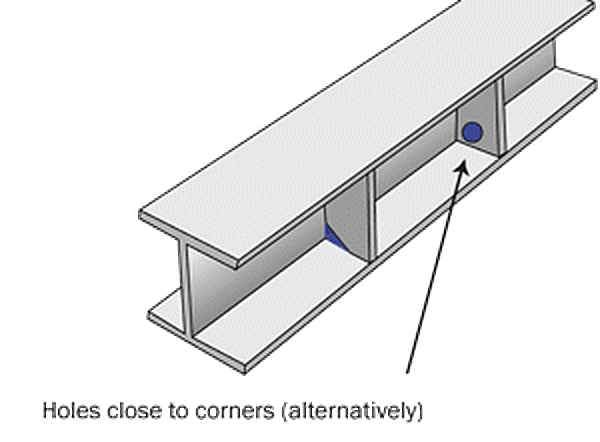
- Where gusset plates are used, generously cropped corners provide for free drainage. When cropping gusset plates is not possible, holes at least 1/2 (13 mm) in diameter must be placed in the plates as close to the corners as possible.
- To ensure unimpeded flow of solutions, all stiffeners, gussets, and bracing should be cropped a minimum of 3/4 (19 mm).
- Provide holes at least 1/2 (13 mm) in diameter in end-plates on rolled steel shapes to allow molten zinc access during immersion in the galvanizing bath and drainage during withdrawal.
- Alternatively, holes at least 1/2 (13 mm) in diameter can be placed on the web within 1/4 (6 mm) of the end-plate. To facilitate drainage, end-plates should have holes placed as close to interior corners as possible.
The following pages provide more detailed venting & drainage information for specific products:
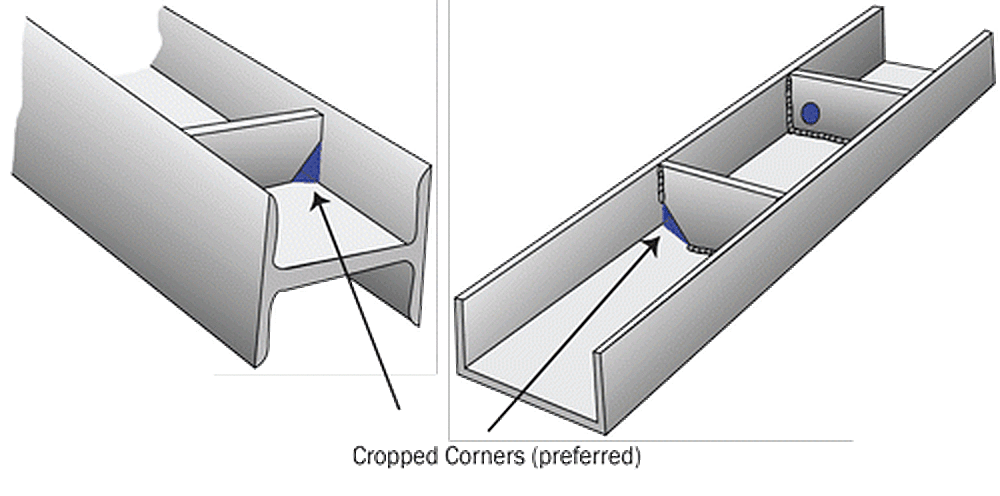
© 2025 American Galvanizers Association. The material provided herein has been developed to provide accurate and authoritative information about after-fabrication hot-dip galvanized steel. This material provides general information only and is not intended as a substitute for competent professional examination and verification as to suitability and applicability. The information provided herein is not intended as a representation or warranty on the part of the AGA. Anyone making use of this information assumes all liability arising from such use.