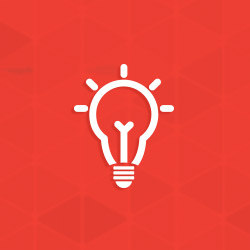
Rough Galvanized Coatings
Why does my galvanized coating look like it developed a bad case of acne in the zinc bath?
Rough galvanized coatings can be caused by steel chemistry, dross inclusions, and a few other factors.
Steel Chemistry
Silicon and phosphorus in steel act as catalysts during the galvanizing reaction. Steel with silicon and/or phosphorus levels outside the recommendations in ASTM A385 is considered reactive steel and can create galvanized coatings with thicker and rougher looking coatings, as seen in Figure 1. Steel heat chemistries are helpful for determining element levels in steel; however, they are samples of the total heat of steel and sometimes are not completely representative of the steel since individual pieces of steel can have levels higher or lower than the sample. In addition, silicon and phosphorus are not always distributed evenly throughout the steel. Some areas of the steel can have higher silicon or phosphorus levels and thus create coatings that grow differently than the surrounding areas. The galvanized coating on reactive steel can have ridges or striations, as seen in Figure 2, and at other times be rough over the entire surface. Rough galvanized coatings do not affect the corrosion resistance of the steel and sometimes can increase the service life of the product because reactive steel has thicker coatings than non-reactive steel.
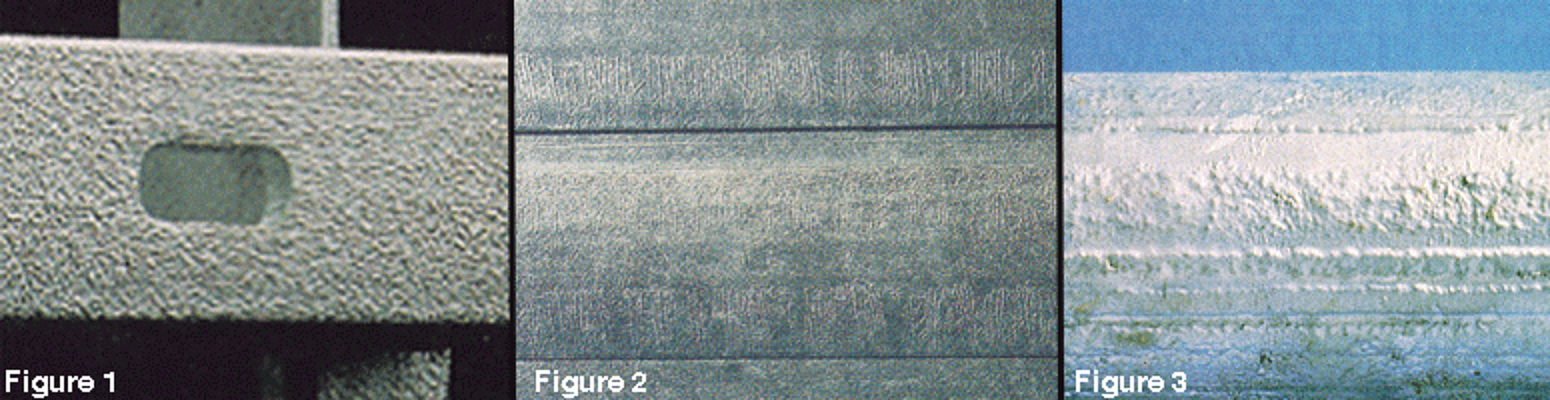
On applications where the steel will be handled frequently, such as on handrails, the coating must be smooth for its intended use and will be rejected if the galvanized coating is rough. Steel with phosphorus levels over 0.04% produces dull coating areas and ridges of the thicker coating where there is increased intermetallic growth. The end result is a rough surface with a ridged appearance, as seen in Figure 3.
Dross Inclusions
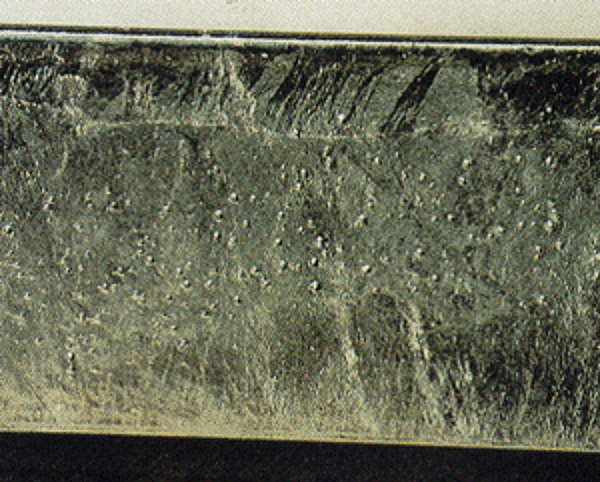
Another source of rough of galvanized coatings is dross inclusions. Dross is created when free iron particles in the galvanizing kettle react with the molten zinc. The dross particles can then adhere to the galvanized coating as the steel is lowered or raised from the kettle and appear as pimples on the coating, as seen in Figure 4. Dross inclusions do not affect the corrosion resistance of the coating; however, if the dross inclusions are large and can be knocked off the galvanized coating and create a bare spot, then that situation is rejectable if those areas cannot be repaired in accordance with ASTM A780. Galvanized steel can also be rejected when dross inclusions affect the intended use of the product, such as on handrail or steel to be painted after galvanizing, as mentioned previously. There are several ways to reduce production of dross in the kettle and therefore minimize dross inclusions. Iron particles in the kettle can be reduced by fully rinsing the steel after cleaning in the pickling tank and limiting the iron content in the preflux. Regulating element additions, such as nickel and aluminum weekly helps to limit iron precipitation in the molten zinc because these elements can decrease iron solubility in the zinc. Maintaining zinc kettle temperatures, especially near the top of the kettle along the walls, greatly reduces floating dross. Lastly, frequently drossing the kettle will help to remove dross.
Other Factors
Rough galvanized coatings can also be caused by conditions other than steel chemistry or dross inclusions. If a steel surface is very rough prior to galvanizing due to mechanical cleaning such as blasting the possibility for that steel to have a rough galvanized coating is much higher than steel with a smooth finish. Excessive blasting or excessive pickling can also create rough galvanized coatings because they create surface roughness in the steel before it enters the galvanizing process.
Summary
Rough galvanized coatings can be caused by several factors, including steel chemistry, dross inclusions, rough steel surfaces prior to galvanizing, excessive blasting or excessive pickling. Rough galvanized coatings can only be rejected when the roughness of the coating affects the intended use of the product, such as on handrail or parts to be painted after galvanizing.
© 2025 American Galvanizers Association. The material provided herein has been developed to provide accurate and authoritative information about after-fabrication hot-dip galvanized steel. This material provides general information only and is not intended as a substitute for competent professional examination and verification as to suitability and applicability. The information provided herein is not intended as a representation or warranty on the part of the AGA. Anyone making use of this information assumes all liability arising from such use.