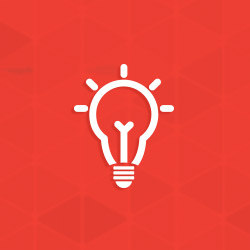
Rough Coatings on Boat Trailers & Handrail - Silicon and Phosphorus
I've been doing boat trailers or handrails for a number of years and every once in a while the coatings will come out looking very rough. Why is this happening and why does it happen in the center section of the part?
There are a couple of reasons that galvanizers may find a very rough coating on a part such as a boat trailer or a section of the handrail. The most obvious reason is the fabricator used a different piece of steel for one section of the assembly. The different piece of the steel had high levels of silicon or phosphorus and was very reactive, causing the thick and rough coatings. The rest of the assembly may be smooth and normal. The inclusion of a reactive piece of steel in the assembly is apparent when the rough coating stops abruptly at a weld line or assembly joint. Sometimes it is an attached bracket or clip which has the rough coating. In the case of a handrail, this rough coating may be the cause for rejection of the assembly since the handrail must be smooth for people to run their hands along.
A second, more subtle reason for the rough coating can be the steel chemistry of the steel tubing used to fabricate the assembly. The fabricator will often have specified a steel with a low silicon and phosphorous content. The steel manufacturer will furnish the mill certification for the steel used to manufacture the tubing and the chemistry will appear to be low reactivity material as in the table below.
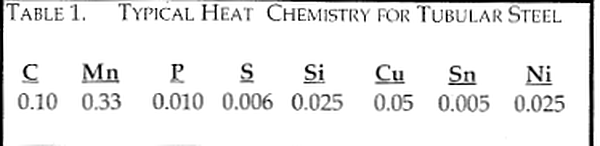
The two reactive elements, phosphorous and silicon, appear to be below the level where they cause thick and rough coatings. When the rough coating appears, some galvanizers are suspicious of the steel chemistry despite what the heated chemistry shows. The galvanizers have taken samples of the actual steel tubing used in the assembly and the results of one example of this steels chemistry are shown in the table below.
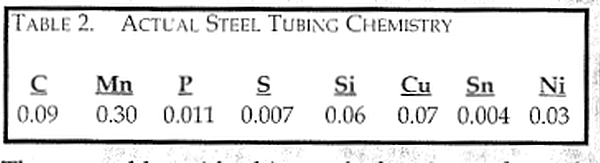
The assembly with this steel chemistry showed rough coatings on some of the pieces. The picture shows the rough appearance of the coating. This looks like the typical example of high phosphorous steel but the actual reactive element in the silicon. The silicon level of 0.06 puts the steel on the leading edge of the Sandelin peak. Added factors such as cold working the tubes inform the shape of the boat trailer and the temperature cycle for the section of tubing in the center of the assembly add to the silicon reactivity.
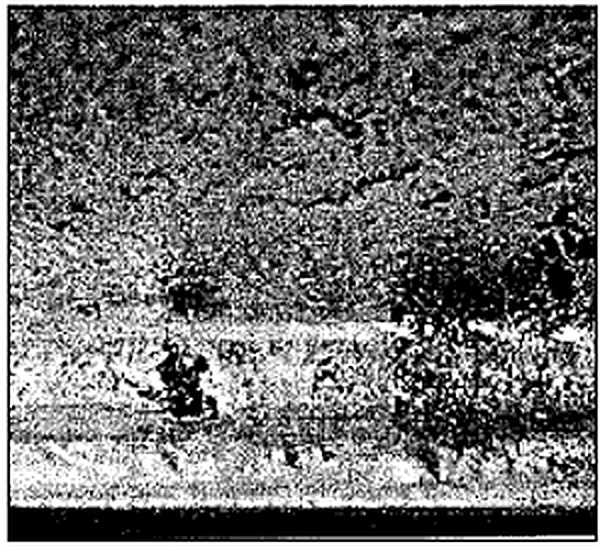
The silicon is on the edge of the reactivity curve and will cause problems on some pieces and not on others. This can be very difficult to diagnose. These assemblies will provide adequate corrosion protection but may be difficult to deliver to a very particular customer because of the rough coating appearance. As a galvanizer, there is very little that can be done about his rough appearance because the problem is caused by the steel chemistry. Steel heat chemistries are an average of sample pieces and do not always reflect the actual chemistry of the tubing parts.
© 2025 American Galvanizers Association. The material provided herein has been developed to provide accurate and authoritative information about after-fabrication hot-dip galvanized steel. This material provides general information only and is not intended as a substitute for competent professional examination and verification as to suitability and applicability. The information provided herein is not intended as a representation or warranty on the part of the AGA. Anyone making use of this information assumes all liability arising from such use.