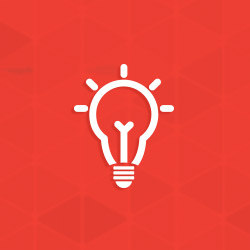
Quench Discoloration
My galvanized coating was stained an unsightly yellow color when it was dipped in the chromate quench tank. What happened?
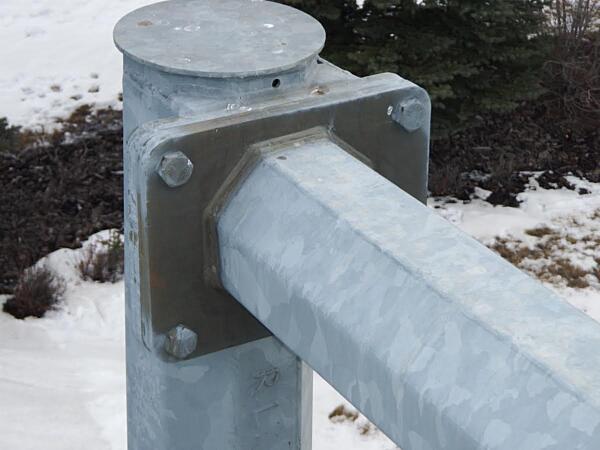
First of all, it is important in this situation to understand the galvanized coating has not been stained. The temporary appearance change of the galvanized coating is only cosmetic in nature and will not affect the long-term corrosion protection performance of the coating. Sometimes, when a chromate passivation treatment is performed on a hot-dip galvanized coating, the steels appearance may be changed by the actual color of the chromate coating itself. Chromate coatings are often clear and do not change the color of the coating. This passive coating, however; becomes thick enough to allow its color to be visible on the galvanized steels surface. Colors of the coating range from iridescent-yellow, to brass, brown, olive-drab, and black. The different colors may be attributed to the presence of zinc chromates, iron chromates, or other dissolved minerals.
Chromate conversion coatings are used in the hot-dip galvanizing industry to protect newly galvanized surfaces from the formation of wet storage stain. A very thin conversion coating will be able to adequately perform this task until the galvanized steel is allowed to properly weather. Most chromate conversion coatings are colored, but thin enough not to cause a discoloration of the galvanized coating. When the coating becomes thicker, its color becomes more apparent and is visible to the naked eye. As the soluble chromate coating dissolves through the natural weathering process, the color present on the surface of the steel will disappear and the natural matte gray appearance of galvanized steel will remain.
It may be required this discoloration be removed from the surface of the steel. In most cases, weathering of the galvanized steel that has been chromate treated for about six months will remove any color on the surface from the conversion coating. If this time frame is not acceptable, and the color needs to be removed immediately, it can be done mechanically. ASTM D7803 Standard Practice for Preparation of Zinc (Hot-Dip Galvanized) Coated Iron and Steel Product and Hardware Surfaces for Powder Coating requires a galvanized surface to be free of chromates before it is powder coated. Therefore, it gives procedures for removing a chromate coating that may also be used for the purpose of removing a colored chromate coating. The standard provides the options of surface grinding with power tools or abrasive sweep blasting for removal. Grinding should be done with care so as not to remove the entire zinc coating, and sweep blasting should be done with a rapid nozzle movement in accordance with SSPC SP 16. Guidelines for these procedures can be found in sections 5.1.3.1 and 5.1.3.3 of ASTM D7803.
Again, the new color observed on the surface of the steel is not a stained galvanized coating, but the color of the passive chromate coating. A colored coating will provide the same protection against the formation of wet storage stain and allow a tough, insoluble zinc patina to form naturally. A very thin chromate conversion coating will adequately protect against wet storage stain and cause little to no appearance change on the surface of the galvanized coating; therefore, avoiding a thick chromate conversion coating will avoid the problem of a discolored galvanized surface after chromate treatment.
Similar to the hot-dip galvanized coating, the properties of a chromate conversion coating can be affected by the temperature of the quench tank and the time the part is immersed in the bath. The pH of the solution also affects the properties of the final coating. Paying attention to the quench bath chemistry, temperature, and time of immersion will allow a galvanizer to determine what conditions lead to a thicker coating that causes a discolored surface.
© 2025 American Galvanizers Association. The material provided herein has been developed to provide accurate and authoritative information about after-fabrication hot-dip galvanized steel. This material provides general information only and is not intended as a substitute for competent professional examination and verification as to suitability and applicability. The information provided herein is not intended as a representation or warranty on the part of the AGA. Anyone making use of this information assumes all liability arising from such use.