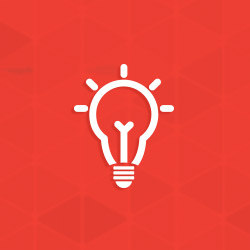
Peeling vs.Flaking
What is the difference between flaking and peeling of a hot-dip galvanized coating?
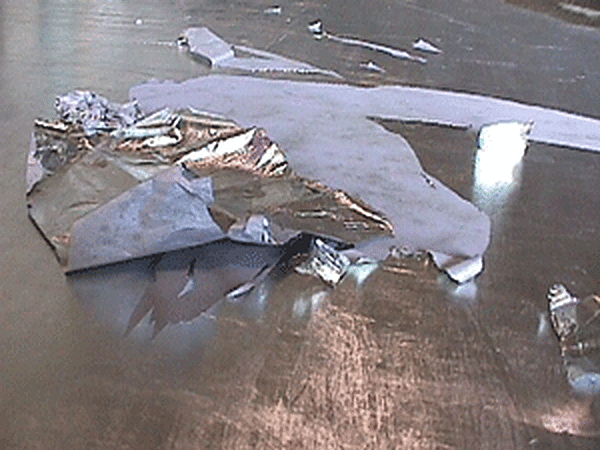
Peeling
Peeling of the galvanized coating is very different from flaking and occurs when the outer free zinc layer separates from the intermetallic layers. When a coating thickness measurement is taken in an area that has peeled, there is some coating left, usually in the range of 2 to 6 mils. One cause of peeling is when a newly galvanized piece cools extremely slowly or when the steel is subjected to high temperatures (excess of 400F) for prolonged periods. When galvanized steel cools very slowly and the part remains in excess of 600F, the galvanizing reaction can continue. The eta layer serves as the source of zinc for further reactions and can be consumed by the galvanizing reaction. This consumption of the eta zinc layer can create voids between it and intermetallics, which then causes peeling of the outer zinc layer, as seen in Figure 1. When peeling is caused in this manner it is called the Kirkendall Effect.
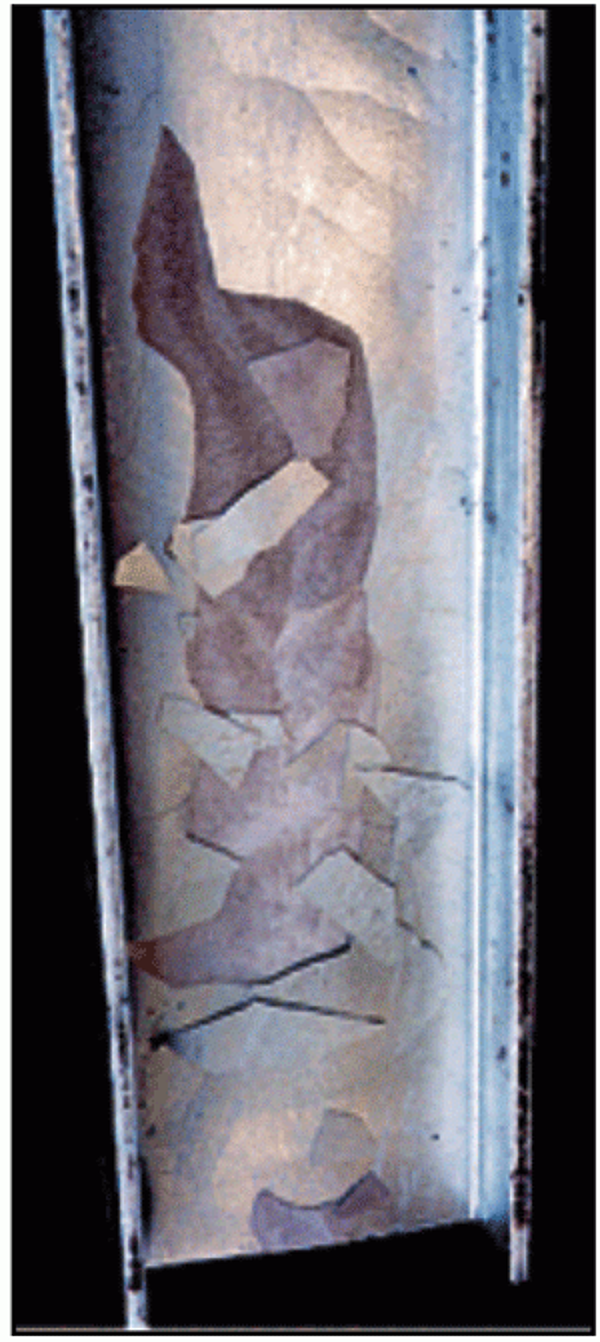
Flaking
Flaking occurs when three of the four galvanized layers detach from the galvanized part. If a coating thickness measurement is taken in the area where the coating has flaked, the measurement will be near zero or even zero in some cases, indicating only the gamma layer is left on the steel. Flaking is caused by excessively thick galvanized coatings that are more brittle than coatings of a normal thickness.
As the galvanized coating grows to and exceeds 10 mils in thickness, it becomes more brittle than thinner coatings. The brittle coating can then flake off the steel when the part is struck, such as during transport or assembly in the field. Pieces of coating that have flaked off the steel usually have very long and distinct edges, as seen in the picture to the right. Because flaking of the coating causes large, nearly bare areas, it is usually cause for rejection and the steel must be repaired or regalvanized.
Some ways to reduce the galvanized coating thickness during regalvanizing include leaving it in the kettle for a shorter time period, decreasing the kettle temperature, and blast cleaning the steel. Ensuring your customers provide steel with recommended chemistry for galvanizing (see ASTM A385) goes a long way to decreasing coating thickness and thereby also reduces the chances for a coating that flakes off the steel. When you know your customer has provided you with reactive steel, blasting the steel prior to galvanizing can reduce the galvanized coating thickness that develops and thereby limits the possibility for flaking. It might also be prudent to have clauses in your purchase orders limiting your responsibility when galvanizing reactive steel that does not meet the recommended chemistry of ASTM A385.
© 2025 American Galvanizers Association. The material provided herein has been developed to provide accurate and authoritative information about after-fabrication hot-dip galvanized steel. This material provides general information only and is not intended as a substitute for competent professional examination and verification as to suitability and applicability. The information provided herein is not intended as a representation or warranty on the part of the AGA. Anyone making use of this information assumes all liability arising from such use.