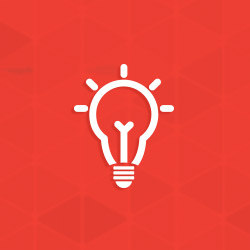
Minimizing the Risk of Warpage and Distortion
What considerations should I keep in mind when designing steel fabrications to be galvanized?
As the name implies, steel is dipped into a bath of molten zinc during the hot-dip galvanizing process. While the process is inherently simple, hot-dip galvanizing is different than painting or other corrosion protection coating systems, and therefore presents unique requirements during the design stage in order to ensure a high-quality zinc coating. ASTM A385, Standard Practice for Providing High-Quality Zinc Coatings(Hot-Dip), specifies design recommendations that should be followed when fabricating steel to be galvanized. There are too many recommendations to be discussed in this issue, so they will be broken up and presented as a series continuing into later issues.
Part 4: Minimizing the Risk of Warpage and Distortion
The hot-dip galvanizing procedure rapidly heats steel assemblies to a temperature between 815 - 850° F. They are then cooled by either quenching or air cooling. This heating and cooling cycle makes some steel assemblies warp and distort if some design practices are not followed. Unlike most design considerations for steel to be hot-dip galvanized, the guidelines for minimizing the risk of warpage and distortion are found inASTM A384 Standard Practice for Safeguarding Against Warpage and Distortion During Hot-Dip Galvanizing of Steel Assemblies. These guidelines are summarized and explained here.
- Cold-formed steel or steel that has been cold worked during fabrication, is subject to warpage and distortion during the galvanizing process. In order to minimize this risk, the steel can be heat-treated according to the procedure outlined in ASTM A143. Avoiding tight bend radii especially in steel plate also reduces the risk of warpage and distortion.
- Great care should also be taken when welding a fabrication together. If the material must be clamped into place with much force in order to be welded, internal stresses will be introduced which may cause warping in the galvanizing kettle. Clamps should only be used to prevent shifting during welding procedures.
- Welding or riveting steel of varying thicknesses together before galvanizing the fabrication should be avoided. A steel fabrication made up of sheet steel welded to plate or bar-sized shapes is one of the most commonly distorted assemblies by the hot-dip galvanizing process. This is due to the varying thicknesses of the two pieces of material and how they will expand and contract at different rates during the thermal cycling. The steel sheet will contain residual stresses from the welding and rolling operations that will be slightly relieved at the galvanizing temperature. The constraints of the larger pieces, however, will not allow the stress to be fully relived; causing the plate to warp.
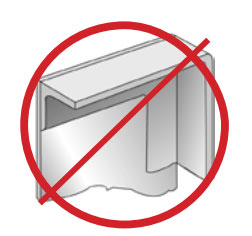
While it may be possible to roll or bend a fabrication back into place if it has been warped or distorted, it is clearly preferable to avoid this issue in the first place. During the design phase, using a material of equal or near equal thickness reduces the risk for warpage. Galvanizing pieces of a fabrication separately, then having them bolted, riveted, or welded together will also reduce this risk.
Much like the subject of steel of varying thickness, asymmetrical pieces and designs run a moderate risk of being warped or distorted when they are hot-dip galvanized. The internal stresses in angles or channel frames, for example, will not be relived evenly due to the constraints of the materials shape. T-beams and checkered plate are also examples of materials subject to warpage. Using shapes that are symmetrical around all major axes such as I-beam, pipe, or H-column, reduce the risk of warpage during hot-dip galvanizing. If it is not possible to use a symmetrical design, adding temporary bracing to asymmetrical designs lowers the risk of the fabrication warping during galvanizing.
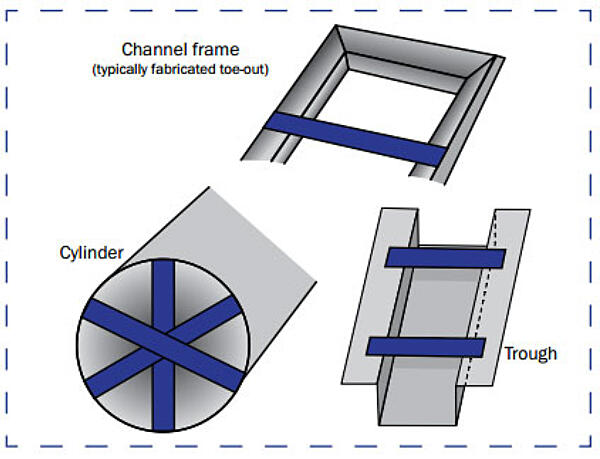
Depending on the size of the galvanizers kettle, some large fabrications may need to be dipped one half at a time. This procedure is known as progressive dipping and the uneven heating and cooling of the material may cause warpage or distortion of the fabrication. Creating two or more smaller subassemblies that can be dipped at one time, and then bolting them together after the steel is galvanized eliminates the need to progressively dip. Communication with your galvanizer about this subject is very important as they know the limitations of their process.
© 2025 American Galvanizers Association. The material provided herein has been developed to provide accurate and authoritative information about after-fabrication hot-dip galvanized steel. This material provides general information only and is not intended as a substitute for competent professional examination and verification as to suitability and applicability. The information provided herein is not intended as a representation or warranty on the part of the AGA. Anyone making use of this information assumes all liability arising from such use.