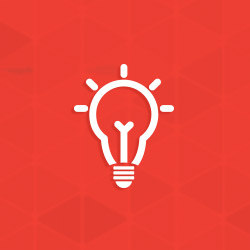
Meeting Minimum Coating Thickness Requirements on Machined Plate
Why is it hard to achieve the required coating thickness on typical 2 thick hot-rolled carbon plate that has been machined smooth? I usually have too much zinc when galvanizing thick plate?
The zinc-iron intermetallic layers of the galvanized coating form when the heat in the molten zinc energizes the iron atoms in the steel to diffuse to the surface of the solid layer and react with the molten zinc to form more of the solid. This diffusion of iron atoms proceeds normally with hot-rolled carbon steel. However, for machined steels and even to some degree cold-rolled steels, the diffusion is slowed and the solid, intermetallic layers take longer to form. Let me explain the science on a micro level first and then on a macro level.
When the smooth, machined steel is initially immersed in the zinc bath, the Gamma layer forms first. Remember, this is not a coating simply attached to the steel, but rather a combination of the iron atoms and the zinc atoms, an actual metallurgical combination of the two. Now, because the surface of the steel is very smooth and the Gamma layer is a very good crystal structure match to the steel structure, the Gamma layer coating is very dense and this slows further diffusion of the iron atoms.
The formation of the Delta and Zeta layers need iron atoms to form new layers. Due to the dense Gamma layer, the iron/zinc intermetallics are much more tightly bound and close than the typical steels galvanized. So, in order for more iron to escape the bonds in the steel so they can react with the molten zinc, they need more energy than normal to pass through the Gamma layer to react with the zinc to form the Delta layer. The same is true for the formation of the Zeta layer.
Now, on a macro level, think of it this way. Hot-rolled steel surfaces, those with mill scale or normal surface rust, generally form normal intermetallic coatings. These steels are the normal steel to be hot-dip galvanized. When there are special requirements for a flat, very smooth surface or a particular it issue with a steel assembly, the steel may be machined to meet the needs of the final assembly. The machined surface is changed from the normal steel crystal structure to something denser and tightly packed. The change in surface characteristics impacts the ability of iron atoms to diffuse during the galvanizing process and results in a thinner coating with the normal kettle time for the steel thickness.
Your follow-up question might be, How can I get enough zinc coating to meet the specification? There are two suggestions but neither is perfect or predictable in its result. You can anneal the steel prior to galvanizing to soften it. This essentially changes the surface density and lessens the stress at the steel surface. You should definitely check with your customer to get approval or discuss this option with him/her because annealing may affect the performance and strength of the piece in its intended use. The second option is to keep the machined article in the bath longer to increase the coating thickness. This is likely to provide only a minimal increase in coating thickness. The best plan is to warn your customer and do the best you can to get coatings that meet the specification.
© 2025 American Galvanizers Association. The material provided herein has been developed to provide accurate and authoritative information about after-fabrication hot-dip galvanized steel. This material provides general information only and is not intended as a substitute for competent professional examination and verification as to suitability and applicability. The information provided herein is not intended as a representation or warranty on the part of the AGA. Anyone making use of this information assumes all liability arising from such use.